-
- News
- Books
Featured Books
- design007 Magazine
Latest Issues
Current IssueShowing Some Constraint
A strong design constraint strategy carefully balances a wide range of electrical and manufacturing trade-offs. This month, we explore the key requirements, common challenges, and best practices behind building an effective constraint strategy.
All About That Route
Most designers favor manual routing, but today's interactive autorouters may be changing designers' minds by allowing users more direct control. In this issue, our expert contributors discuss a variety of manual and autorouting strategies.
Creating the Ideal Data Package
Why is it so difficult to create the ideal data package? Many of these simple errors can be alleviated by paying attention to detail—and knowing what issues to look out for. So, this month, our experts weigh in on the best practices for creating the ideal design data package for your design.
- Articles
- Columns
- Links
- Media kit
||| MENU - design007 Magazine
Estimated reading time: 4 minutes
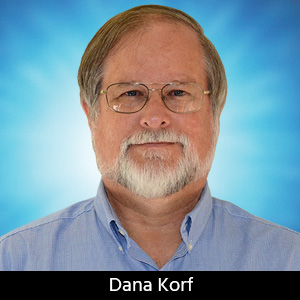
Dana on Data: IPC AME Standards Development Launched
An important element of design requirement determination and manufacturing requirements involves qualification, performance, and inspection standards. These are critical to ensure that the product’s electrical, mechanical, and reliability requirements are met without expensive over/under specification.
Additively manufactured electronics (AME) technology is progressing from proof-of-concept, quick-turn circuit board production into volume shipped circuits. These are true pure additively manufactured (AM) PCBs which may incorporate formed 3D passive components, antennas, coax, and twisted pair interconnect.
As volumes increase, users are asking what industry specifications these can comply with and how production volume quality and reliability will be validated. For example, they are looking at how to populate the following drawing note:
“This PCB shall comply with the Class (1, 2, or 3) requirements of IPC-ABCD and IPC-A-XYZ, unless otherwise noted.”
There currently aren’t any AME performance, qualification, or acceptance standards published by any international standards organization.
There are very good IPC standards in place for rigid, flexible, and rigid-flex boards for design, performance, qualification, and acceptance. So, why doesn’t AME just use them? The reason is there are many substantial differences between how AME and traditional PCBs are manufactured; Table 1 presents some key differences.
New IPC Standards Development
The IPC TAEC recently approved the request for the formation of a new subcommittee (D-67) and three new task groups to create three initial standards. As their basis, these standards are derived from the existing IPC-6012, IPC-6013, IPC-A-600, and IPC-2221 standards.
IPC-6905 Qualification and Performance Specification for AME
Many users of AME boards consider them to be a traditional PCB or as a component to potentially mount onto a PCB. IPC-6905 requirements are derived from the existing PCB IPC-6012 and IPC-6013 rigid, flexible, and rigid-flexible qualification and performance specifications. Requirements are removed that are not applicable for AME boards (Table 1). Requirements for potential AM-specific failure mechanisms are added, such as slice-to-slice voids and delamination.
Embedded formed, packaged, and unpackaged components, along with surface components, are typically fabricated in these structures. The goal will be to reference the IPC-6017 Embedded Standard requirements and test methods as much as possible.
IPC-6911 Acceptability of AME
This is an important document as it will provide visual surface and cross-sectional acceptance and rejection requirements. Its structure is derived from the IPC-A-600 Acceptability standard. The task group may potentially acknowledge AI inspection and real time process adjustments. As with IPC-6905, views have been removed from the IPC-A-600 standard that are not applicable for additively manufactured boards. Additional views will be included to match the new IPC-6905 requirements.
IPC-B-XX AME Coupons
IPC has been using 2D Gerber file-based coupons for decades. These are documented in IPC-2221 along with associated data files. These coupons are based on manufacturing processes for horizontally routed conductors and vertically drilled/ablated plated holes. AME does not remove material and has 3D-formed passive components, such as coils, 3D antennas, coax, and twisted pair wiring along with vertical traces routed in the X, Y, and Z axes. This standard will create new 3D coupons that will be utilized as the test vehicles confirming AME performance and used as qualification test vehicles. AME boards may consist of functional components and interconnect which present a challenge because testing will advance from interconnect reliability testing to incorporation for functional component parametric validation.
The Teams
The subcommittees and task groups have a wide breadth of volunteers from Europe, North America, and Asia to form these standards. Industries such as military, PCB fabricators, consumer, AME equipment manufacturers, and AM material suppliers are represented. IPC is always looking for more volunteers to review and develop standards to ensure they accurately specify industry requirements for electronic interconnects. Join the teams that are developing these new standards for this exciting AME technology.
Dana is the AME standards manager at Nano Dimension where he is responsible for working with the industry to create additively manufactured electronics (AME) standards. He is chair of IPC D-67 AME subcommittee and vice chair of the ASTM F24-07-06 AM Applications, Electronics subcommittee.
Dana is the principal consultant at Korf Consultancy LLC, working with companies to improve PCB fabricator front-end engineering processes. He works with OEMs and ODMs to create design rules and technology roadmaps, assist with supplier selection/qualification, and reduce DFM cycles. Dana previously worked for more than seven years in China at Multek in Zhuhai as senior director of manufacturing engineering and NPI and at Huawei Technologies in Shenzhen as director of PCB technology, where he was responsible for PCB technology ranging from mobile phones to RF antennas, base stations, and high-speed digital servers and switches.
Before that, he worked for Samina-SCI, HADCO, and Zycon as director of product engineering. He has been awarded the IPC President’s Award, chaired many high-speed IPC committees, and was a co-chair for the iNEMI Data Convergence project, which became IPC-2581. Dana graduated from Washington State University with a BSEE, and he enjoys following college and professional football and golf.
This column originally appeared in the October 2023 issue of Design007 Magazine.
More Columns from Dana on Data
Dana on Data: The Missing AI-NPI LinkDana on Data: Merging 2D Electrical, 3D Mechanical Worlds
Dana on Data: Resurrecting IPC Class 1
Dana on Data: The Evolution of Fabrication Drawing
Dana on Data: The Insane PCB DFM Process
Dana on Data: eCAD PCB Design Deficiencies
Dana on Data: Nuke the Netlist
Dana on Data: Simplify PCB Documentation