-
- News
- Books
Featured Books
- design007 Magazine
Latest Issues
Current IssueProper Floor Planning
Floor planning decisions can make or break performance, manufacturability, and timelines. This month’s contributors weigh in with their best practices for proper floor planning and specific strategies to get it right.
Showing Some Constraint
A strong design constraint strategy carefully balances a wide range of electrical and manufacturing trade-offs. This month, we explore the key requirements, common challenges, and best practices behind building an effective constraint strategy.
All About That Route
Most designers favor manual routing, but today's interactive autorouters may be changing designers' minds by allowing users more direct control. In this issue, our expert contributors discuss a variety of manual and autorouting strategies.
- Articles
- Columns
- Links
- Media kit
||| MENU - design007 Magazine
Estimated reading time: 3 minutes
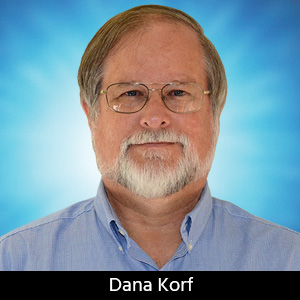
Dana on Data: The Insane PCB DFM Process
This industry just doesn’t like to change. Line width/space is consistently narrowed; layer counts are now over 120 layers; via diameters constantly shrink. But a fabricator still can’t build per the supplied data package because of design, document, and capability mismatch errors.
I have been writing for I-Connect007, and of the 41 articles and interviews I have done, 39 have focused on highlighting designer-to-fabricator data transfer issues with proposed solutions. Little has changed to improve the transfer. This industry seems to accept receiving erroneous PCB data.
Let’s use an airplane trip as an example. Image that I wanted to travel from Seattle to Atlanta on KorfAir. I provide reservations with instructions and payment to travel via the ferry from Seattle to Bremerton. They send the documents to KorfAir. But prior to booking the ticket they respond with a TQ stating that they only use airplanes and that’s the wrong direction. They propose that they re-book a flight before they can accept the reservation. I respond it’s okay.
I classify issues that inhibit a data packaged to be released, as provided, into three generic categories:
- Plant capability misalignment
- Documentation issues
- Design errors
Plant Capability Misalignment
This is not always the designer’s fault because they may not know which fabricator will be the manufacturer. They are often selected after the design is complete by procurement or being sourced from an EMS partner that will select the fabricator after receiving the data package and performing their assembly and test DFM review. When the designer does know who the fabricator(s) are (will be), a complete set of design rules are not provided to them or are not available prior to the design start.
The travel corollary is I booked the flight and I’m requesting seat 32C. The problem is the plane only has 20 rows. KorfAir obviously didn’t provide the correct capability.
Documentation Issues
There are many manufacturing documents provided in the procurement package with the graphical file to provide the remaining design manufacturing intent. Documents examples are fabrication drawings, stackup/impedance requirements, netlist, and drill files. These files often have revision control synchronization issues, cut-and-paste issues, etc. This creates conflicting specifications from the same requirement, e.g., PCB outline dimensions.
The travel corollary is: The traveler provided two documents to KorfAir. One stated that they wanted to travel to Atlanta and another document stating that they want to travel to Macon, Georgia. Both cities are close to each other. KorfAir can pick the destination or send a TQ asking which city is correct.
Design Errors
Let’s focus on design errors in the data package. The fabricator could build per the documentation. Fortunately, advanced DFM reviews will request further input.
What do I classify as a design error? Here are a few common errors:
- Solder mask on pad
- Drilled hole inner layer pad misalignment
- Legend on pad
- Impedance value that does not match the stackup and graphical data
- Solder mask covered test points
- Specified IPC Class violations
- Non applicable drawing notes
- Conflicting documentation and files
The Hidden Cost and a Radical Proposal
There are millions of dollars wasted every year by the fabricator having talented people and software systems identifying and proposing resolution for these issues. Unfortunately, this cost is buried in the fabricator's cost. The designer’s company doesn’t directly see this cost. One radical idea is to move this cost back to the data provider. One idea that has been floated is to charge more for Gerber-based packages than for IPC-2581 or ODB++-based packages due to the additional time it takes to review the associated documents and resolve issues. But this hasn’t been well received.
I would like to propose a radical change in thinking. Manufacturers should not spend any time correcting design and documentation errors. The fabricator should build the PCB per the supplied data package and ship it to the requestor. They should only absorb the cost/time correcting capability DFM issues where insufficient design rules were provided to the designer. This way the cost for bad design data will be borne by the data owner. This moves the correction cost back to the source, hopefully motivating them to improve their design release process.
Then, there may be more motivation to provide correct data without design issues or conflicting documentation. The industry would need to change en masse because if any individual company used this process they would go out of business because the customer would just move to another company. This is a problem because PCB manufacturing is perceived as a commodity business, like buying paper towels, or airline tickets.
Dana Korf is the principal consultant at Korf Consultancy LLC.
More Columns from Dana on Data
Dana on Data: Best Practices in Interpreting Drawing Notes—‘Use Latest Revision’Dana on Data: The Missing AI-NPI Link
Dana on Data: Merging 2D Electrical, 3D Mechanical Worlds
Dana on Data: Resurrecting IPC Class 1
Dana on Data: The Evolution of Fabrication Drawing
Dana on Data: eCAD PCB Design Deficiencies
Dana on Data: Nuke the Netlist
Dana on Data: Simplify PCB Documentation