-
- News
- Books
Featured Books
- design007 Magazine
Latest Issues
Current IssueProper Floor Planning
Floor planning decisions can make or break performance, manufacturability, and timelines. This month’s contributors weigh in with their best practices for proper floor planning and specific strategies to get it right.
Showing Some Constraint
A strong design constraint strategy carefully balances a wide range of electrical and manufacturing trade-offs. This month, we explore the key requirements, common challenges, and best practices behind building an effective constraint strategy.
All About That Route
Most designers favor manual routing, but today's interactive autorouters may be changing designers' minds by allowing users more direct control. In this issue, our expert contributors discuss a variety of manual and autorouting strategies.
- Articles
- Columns
- Links
- Media kit
||| MENU - design007 Magazine
Estimated reading time: 9 minutes
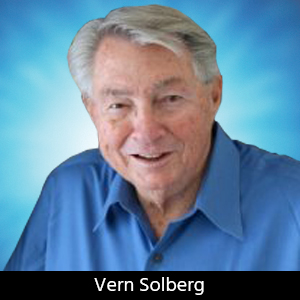
Designers Notebook: PCB Design and IPC-CFX for Assembly Automation
Surface mount technology (SMT) is a manufacturing process that, through the application of a wide range of small outline components, provides capability to design a printed circuit with higher component density. The assembly process offers the user a means of efficiently producing electronic products in high volume with robotic assembly processing. The circuit board designer can serve a vital role in developing a surface mount configured product that will be prepared for efficient assembly processing.
The thing is, we may not know whether the product will be produced in low or high volume, so the best suggestion is to “think positive” and anticipate a design ready for assembly automation, one that will conceivably be processed on an in-line system using conveyors to shuttle the board from one machine to the other.
Surface mount assembly processing is a sequence of events that involves a wide range of component types (passive and active, coarse-pitch, fine-pitch, BGA, CSP), many requiring specialized systems and strict process controls. Looking from the top, Figure 1 furnishes the basic “print-place-solder reflow” process sequence for a conveyor-linked surface mount assembly line.
Planning for Robotic Assembly Processing
The robotic systems developed for SMT applications are very efficient for the tasks they were designed to do, but getting them to function as a unified system when setting up the assembly line with equipment from multiple sources was a very complex task. This was because many companies developing these systems relied on different programming methods, often software that was proprietary to only the equipment they produced.
To streamline the process for integrating all functions of the assembly process, users needed to have a plug-and-play solution that simplified and standardized machine-to-machine communication. With the cooperation between the equipment developers and IPC member companies using these systems, the Connected Factory Initiative Subcommittee was formed. The ultimate goal of the subcommittee was to develop software tools that relied on a single, comprehensive, agreed-upon language and data set for all machine types.
The Connected Factory Exchange (CFX) was born: “Implementing CFX eliminates needless machine interface development costs, eliminates the need for middleware and reduces time, risk, and costs for solution deployment.”1
SMT Assembly Sequence
Step one: Solder deposition is the process of printing a precise volume of solder paste onto the land pattern features of individual components. The base material commonly used to prepare the stencil is a thin stainless-steel sheet. Land pattern features are laser cut using a program developed directly from the circuit board design file to form the openings for solder paste transfer. Solder alloy compositions selected for surface mount assembly typically combine tin and silver or tin, silver, and copper (Sn/Ag/Cu). The Sn/Ag/Cu combination has become the alloy of choice for a broad number of commercial electronics assembly applications. The so-called SAC alloys provide excellent solder joint reliability, fatigue resistance, minimized copper dissolution rates, and all elements within the compound comply with IPC, JEDEC, RoHS, and REACH lead-free (Pb-free) soldering standards.
To enable precise alignment of the stencil and circuit board, two globally positioned fiducial targets will be provided on the circuit board's surface. To accommodate camera access for stencil-to-board positioning, these target features will be partially etched into the bottom surface of the stencil panel.
Step two: Component placement employs robotic systems with vacuum pickup nozzles, using the coordinates and orientation furnished in the PCB design file to sequentially pick up each component from a carrier and place it onto the designated land pattern feature on the circuit board's surface. Placement systems have taken on a modular approach, with larger and smaller components assigned to different modules that are appropriately tooled. When circuit boards have a high quantity and wide value range of small passive components, two or more modules may be required.
Because most surface mount components are passive resistors and capacitors, the machine selected for assembly of these devices is likely to implement a high-speed “chip placer,” reserving the slower but significantly more accurate placement system for mounting the larger, high I/O lead-frame and BGA semiconductor packages, the smaller fine-pitch BGA devices, and even WLCSP (face-down bumped die elements).
Placement system selection criteria:
- Number of components
- Number of component values or types
- Component complexity (fine-pitch)
- Placement accuracy and repeatability
Although component placement speed is important, assembly systems may have differing levels of accuracy. The more complex and significantly heavier semiconductor devices will have a slower cycle time and will require vision capability to ensure component-to-land pattern alignment accuracy.
The following criteria for component placement accuracy will influence assembly system selection:
- Passive devices: ±70 micron
- Small outline ICs: ±70 micron
- Fine-pitch ICs: ±40 micron
- BGA and FBGA: ±40 micron
- Flip-chip/WLCSP: ±20 micron
As passive components become smaller and terminal pitch on semiconductor packaging shrinks, placement accuracy will be even more critical and precise.
Step three: The last step of the surface mount assembly sequence is the solder-reflow process. In this process, the circuit assembly is gradually heated to the temperature where the solder composition becomes liquidus, completing the joining of component terminals to the circuit land patterns.
The four primary methods used for solder termination of surface mount components in medium- and high-volume production operations are:
- Convection dominant reflow
- Infrared (IR) reflow
- Conduction transfer
- Wave solder
The convection-dominant solder-reflow process is favored by many high-volume manufacturers. These systems have been developed for in-line solder processing, transporting the circuit board (with placed SMT components) through a series of heat zones and progressively converting the deposited solder paste to a liquidus state. The temperature of the assembly will gradually rise upward to a peak temperature between 240°C and 260°C, promoting wetting between the components’ terminals and the circuit board’s land patterns.
Preparing for Conveyor Board Transfer
Placement systems commonly have belt conveyors to transfer the board through each stage of the assembly process. The belt system supports the board or panel on two edges.
Key factors that will influence assembly system compatibility:
- Board thickness (thin boards may require a smaller panel)
- Weight of components (may require support)
- Maximum board outline limit (machine dependent)
Panel development: From a process efficiency standpoint, multi-unit panels can increase line throughput, sometimes significantly, by allowing simultaneous parallel processing of multiple circuit boards, especially during stencil solder paste printing, reflow-solder processing, and, when required, post-process cleaning operations.
During the planning stage of the board design, the designer will be responsible for recognizing the conveyor edge keep-out zones and, when developing the two-sided SMT circuit board, observing the maximum height profile for components mounted on the bottom surface of the circuit board.
When developing the panel for conveyor handling, the designer must extend the width of the panel to prevent physical contact between component elements and the conveyor transport mechanism. The panel detailed in Figure 2 represents a typical circuit board outline for conveyor transfer between the systems.
The goal is to ensure a smooth, unencumbered flow from one system to the next. The 5.0 mm wide “Keep out zone” noted in the detail represents the surface area of the panel reserved for conveyor transfer mechanisms. Tooling holes are to be located near the corners of the panel. Because these holes are reserved for post-assembly processing, they must be specified on the fabrication detail as “non-plated.” The non-plated tooling holes may also be used during the electrical testing of the assembled unit(s) and later, during the de-panel operations.
Fiducial targets: Most of the systems developed for surface mount assembly have a built-in vision system that can identify key features on the circuit board’s surface. There are “global” fiducial targets and features designated as “local” fiducial targets. Global fiducial targets are to be located in areas outside the component mounting zone. These target features are initially used to enable precise alignment of the solder stencil to the surface mount component’s land patterns.
Fiducial targets are small-diameter copper features formed during the final circuit etching process. The size of the fiducial target (Figure 3) can range from 0.5 mm to 1.0 mm in diameter. To allow unobstructed access for vision-assisted solder paste and component placement processes, the fiducial must be clear of solder mask coating. The solder mask opening will be two to three times the diameter of the fiducial target profile to ensure vision system recognition.
Following solder paste printing or solder paste deposition, these same global fiducials will serve as the 0-0 reference for the precise X-Y location for robotic SMT component placement.
Additional fiducial targets located within the component’s mounting zones are often required to assist in accurate placement of the more complex semiconductor packages. For example, two or more fiducial targets may be needed near the mounting sites for “fine-pitch” semiconductors (BGAs, CSP, flip-chip), particularly those with ball terminal centers less than 0.4 mm. These local fiducial targets may also be furnished in close proximity to a grouping of micro-passives (0201s, 01005s, and smaller devices).
When possible, review the fiducial target locations with the assembly process engineer and those responsible for assembly system program development.
In developing the optimum multiple-unit panel dimensions for assembly processing, the designer must first consider minimizing material waste while maximizing assembly process efficiency. Medium to large system-level circuit boards can be designed as a single rectangular-shaped unit or panel typical of that shown in Figure 2. This format will enable efficient in-line conveyor transfer of the smaller circuit board as well, but the circuit board’s laminate material must be extended away from the basic board outline in order to furnish a more uniform panel-like format. The uniform panel outline facilitates efficient conveyor transport of the multiple unit panels between assembly systems.
To further maximize assembly process efficiency for the irregular-shaped circuit boards, the designer can better utilize material by alternating the orientation of each board to create a uniform panel format typical of that shown in Figure 4.
Small, thin, rigid circuit boards, carrier-backed flexible circuits, as well as rigid-flex circuits, are ideal candidates for panel processing. The following five examples represent common multiple-unit panel layout variations:
- Single row format (side by side of uniform shaped boards)
- Nested single-row format (alternating sides)
- Simple array format (row and column layout)
- Nested array format (maximizing area utilization)
- Opposing orientation array format (minimizing material waste)
Note: The final configuration of the multiple-unit panel will require input from the circuit board manufacturer (supplier) and the assembly process specialists (user) responsible for producing the end product. From their input, the designer can prepare the documentation showing the agreed-upon panel configuration.
In closing, the circuit board design specialist will find that the IPC-CFX standard means that the factory and circuit board designer can be fully “connected” through the CAD system used in developing the circuit board and all the machines and software used in the assembly process. For more details regarding CFX protocols, visit IPC to learn more about how IPC-2591 is enabling "plug and play" IoT communication across the manufacturing environment, where all equipment, manufacturing processes, and transactional stations can communicate without the need for specialized software.
References
1. IPC-2591, Connected Factory Exchange (CFX), ipc.org.
This column originally appeared in the July 2024 issue of Design007 Magazine.
More Columns from Designer's Notebook
Designers Notebook: Basic PCB Planning Criteria—Establishing Design ConstraintsDesigners Notebook: Layer Stackup Planning for RF Circuit Boards
Designers Notebook: Addressing Future Challenges for Designers
Designers Notebook: Impact of Advanced Semiconductor Packaging on PCB Stackup
Designers Notebook: Implementing HDI and UHDI Circuit Board Technology
Designer's Notebook: Heterogeneous Integration and High-density SiP Technologies
Designer’s Notebook: What Designers Need to Know About Manufacturing, Part 2
Designers Notebook: What Designers Need to Know About Manufacturing, Part 1