-
- News
- Books
Featured Books
- smt007 Magazine
Latest Issues
Current IssueMoving Forward With Confidence
In this issue, we focus on sales and quoting, workforce training, new IPC leadership in the U.S. and Canada, the effects of tariffs, CFX standards, and much more—all designed to provide perspective as you move through the cloud bank of today's shifting economic market.
Intelligent Test and Inspection
Are you ready to explore the cutting-edge advancements shaping the electronics manufacturing industry? The May 2025 issue of SMT007 Magazine is packed with insights, innovations, and expert perspectives that you won’t want to miss.
Do You Have X-ray Vision?
Has X-ray’s time finally come in electronics manufacturing? Join us in this issue of SMT007 Magazine, where we answer this question and others to bring more efficiency to your bottom line.
- Articles
- Columns
- Links
- Media kit
||| MENU - smt007 Magazine
Estimated reading time: 1 minute
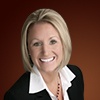
Electroformed Stencils
The continued drive in electronics to place increasingly smaller components on boards poses continuing challenges to board manufacturers. Tight pad spacing as well as placement of small 0201 and 01005 components is becoming more commonplace on board assemblies. Not only are the parts nearly invisible when placed, but their small size causes challenges with the solder paste application and release needed to yield reproducible, low-defect solder joints. The short scoop this month is that you can meet the challenges of paste application for difficult assembly printing processes by using electroformed stencils.
It may seem that a stencil is a rather simple device; after all, in its basic form it is just a sheet of metal stretched taught with hole patterns placed in it to allow application of solder paste in the open areas. The stencil and its fabrication have a great influence over the ability of the circuit board assembly manufacturer to reliably reproduce the desired depositions necessary for paste application.
Stencils can be laser cut with or without post-processing, which for many applications is sufficient to get the paste application process completed reliably. Both of these fabrication techniques are currently employed in mainstream stencil production, but they both start to exhibit their limitations as pattern features decrease in size. The roughness of the stencil wall is one of the major influences on how well paste will release from the stencil. The rougher the sidewall of the aperture, the more the paste is prone to sticking onto the edge of the wall. The apertures used with larger pad features are somewhat more tolerant to edge roughness due to usually higher area ratios. As the pattern features decrease in size, the amount of paste that does not release due to a rough edge becomes an increasingly larger portion of the target application volume. So as feature size decreases, the fabrication of the stencil needs to be constructed for enhanced release capability.
Read the full column here.
Editor's Note: This column originally appeared in the January 2014 issue of SMT Magazine.
More Columns from The Short Scoop
Adapting Stencils to Manufacturing Challenges in 2015The Short Scoop: Stencil Printing in PCB Cavities
The Short Scoop: Printing Two-level PCBs in One Step with a 3D Electroform Stencil
The Short Scoop: Improving Stencil Printing Results
The Short Scoop: More Stencil Questions (and the Answers!)
The Short Scoop: Selecting a Stencil Frame
The Short Scoop: Screen Printing Solutions for Small Die & Precision
The Short Scoop: 10 Common Stencil Questions