-
- News
- Books
Featured Books
- design007 Magazine
Latest Issues
Current IssueAll About That Route
Most designers favor manual routing, but today's interactive autorouters may be changing designers' minds by allowing users more direct control. In this issue, our expert contributors discuss a variety of manual and autorouting strategies.
Creating the Ideal Data Package
Why is it so difficult to create the ideal data package? Many of these simple errors can be alleviated by paying attention to detail—and knowing what issues to look out for. So, this month, our experts weigh in on the best practices for creating the ideal design data package for your design.
Designing Through the Noise
Our experts discuss the constantly evolving world of RF design, including the many tradeoffs, material considerations, and design tips and techniques that designers and design engineers need to know to succeed in this high-frequency realm.
- Articles
- Columns
- Links
- Media kit
||| MENU - design007 Magazine
Estimated reading time: 1 minute
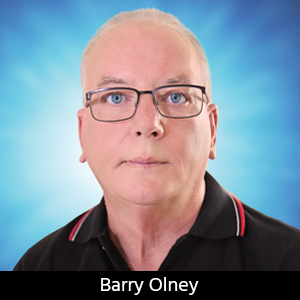
Surface Finishes for High-Speed PCBs
The Nickel Doesn’t Make Cents!
PCB surface finishes vary in type, price, availability, shelf life, assembly process, and reliability. While each treatment has its own merits, electroless nickel immersion gold (ENIG) finish has traditionally been the best fine pitch (flat) surface and lead-free option for SMT boards over recent years. But unfortunately, nickel is a poor conductor with only one third the conductivity of copper. Also, nickel has a ferromagnetic property that can adversely affect electromagnetic fields in the high-frequency domain.
The PCB industry has addressed the issue of the ferromagnetic properties of nickel by introducing a nickel/gold (NiAu) alloy. Gold is slightly less conductive than copper, and has no ferromagnetic properties, so it has relatively little impact on the conductor's loss characteristics at high frequencies.
Microstrip (outer) layers of a multilayer PCB suffer from wide variations in both trace width and thickness. This is due to the additional fabrication process of electroplating the through-holes. Copper barrel thickness is generally specified as a minimum of 1 mil (25.4 µm), and so extra copper plating is applied to the surface in order to produce the correct barrel wall thickness. This, unfortunately, is also added to the traces. But as the thickness and width varies, so does the impedance. This is one of the reasons why routing controlled impedance signals, on the microstrip layers, should be avoided.
It is also very important not to pour copper fills on the signal layers of the board, as these will dramatically change the impedance of the traces rendering the impedance control ineffective.
Read the full column here.
Editor's Note: This column originally appeared in the June 2014 issue of The PCB Design Magazine.
More Columns from Beyond Design
Beyond Design: The Metamorphosis of the PCB RouterBeyond Design: Radiation and Interference Coupling
Beyond Design: Key SI Considerations for High-speed PCB Design
Beyond Design: Electro-optical Circuit Boards
Beyond Design: AI-driven Inverse Stackup Optimization
Beyond Design: High-speed Rules of Thumb
Beyond Design: Integrated Circuit to PCB Integration
Beyond Design: Does Current Deliver the Energy in a Circuit?