Estimated reading time: 3 minutes
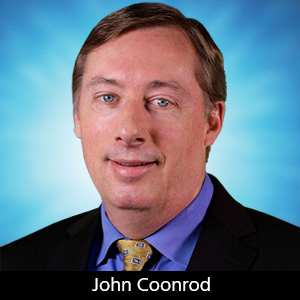
Lightning Speed Laminates: High-Frequency Laminates - Why the Wide Range of Dielectric Constants?
Editor's Note: This article originally appeared in the October 2012 issue of The PCB Magazine.
As an example of how the application of a circuit affects the Dk, let’s look at a PCB-based antenna, such as a double-sided microstrip patch antenna. This type of antenna typically will use a material with lower Dk values because it enables the antenna to be more efficient. When designed correctly, a thicker laminate using a low Dk will cause the patch circuit patterns (antenna-radiating elements) on the PCB to radiate energy. In the case of an antenna where transmitting power efficiently is important, the radiation of energy is desirable. However, the energy must get to the radiating elements; this is done through a feed line on the PCB, which can also radiate energy. In the case of the feed line, the designers would not want to lose energy due to radiation losses. Antenna designers face this dilemma frequently.
One solution is to make the antenna a multilayer PCB construction, where the outer layer is the radiating elements of the microstrip patch antenna, and the feed line is on an inner layer, using a different material and construction to minimize radiation losses. The dielectric materials used for the radiating elements of the patch antenna may have a Dk of 2.5, whereas the materials for the feed line may be around four. This example is a simplification of an issue that can be relatively complicated; however, it illustrates some reasons why materials of different Dk values are used in antenna applications.
Many RF microwave applications have filter elements designed on the PCB. These filter elements are designed with many considerations of wavelength. The wavelength is frequency-dependent as well as material-dependent. The material Dk has a dramatic effect on the wavelength and is inversely related. For example, using the same design at the same frequency, the circuit will have a much shorter wavelength on the PCB when using a high-Dk material, as compared to using a low-Dk material, as shown in Figure 1.
Figure 1: A simple illustration of the Dk vs. wavelength effect.
Many of the conductors on an RF microwave PCB, which are used as part of the filter design, have lengths that are ½ wavelengths for the frequency of concern. With each filter having several elements, the overall filter can be relatively large and take up valuable space on the PCB. One method to minimize the size of these filters calls for using materials with high Dk values. This means the wavelengths are shorter, which translates into shorter lengths for the filter elements.
Transmission line circuits are used on PCBs and basically connect different circuit features. Many times the transmission lines need to be a controlled impedance—typically 50 ohms. These transmission lines also have concerns with loss, and when the conductor is narrower, more losses result. When looking to improve the loss of a transmission line, sometimes a material with a lower Dk value is used.
Assuming the circuit is controlled impedance, when using a material with a lower Dk value, the conductor width will need to be wider in order to maintain the set value of the impedance. Another benefit is related to circuit fabrication yields. The material with the lower Dk value will enable the conductor widths to be wider when considering controlled impedance designs, and wider conductors typically are better for circuit fabrication yields. Figure 2 shows conductor widths as compared to the Dk of the material used for 50-ohm transmission line circuits.
Figure 2: Conductor widths as compared to the Dk of the material used for 50-ohm transmission line circuits.
There are many reasons high-frequency circuit materials offer several values of Dk. Some are related to achieving the optimum performance of an antenna circuit, while others are due to the physical size of the circuit. It is always recommended that the designer and fabricator contact their material supplier to learn more about the material properties and how they can impact circuit performance. Rogers Corporation works closely with circuit fabricators and the OEM designers, and your material supplier should welcome close collaboration when dealing with new circuit applications or optimizing current ones.
John Coonrod is a market development engineer for Rogers Corporation, Advanced Circuit Materials Division. About half of his 25 years of professional experience has been in the flexible PCB industry doing circuit design, applications, processing and materials engineering. Coonrod has also supported the high-frequency, rigid PCB materials for Rogers for the past 10 years. Coonrod may be reached at john.coonrod@rogerscorporation.com.
More Columns from Lightning Speed Laminates
Lightning Speed Laminates: Millimeter-wave Properties and PCB Design ChallengesLightning Speed Laminates: Optimizing Thermal Management for Wireless Communication Systems
Lightning Speed Laminates: Test Vehicles for PCB Electrical Material Characterization
Lightning Speed Laminates: Optimum Thermal Stability Considerations
Lightning Speed Laminates: Thermal Management Isn’t Getting Easier
Lightning Speed Laminates: Benefits of High-Performance Hybrid Multilayer PCBs
Lightning Speed Laminates: An Overview of Copper Foils
Lightning Speed Laminates: The Importance of Circuit Features for Millimeter-Wave Applications