-
- News
- Books
Featured Books
- pcb007 Magazine
Latest Issues
Current IssueSales: From Pitch to PO
From the first cold call to finally receiving that first purchase order, the July PCB007 Magazine breaks down some critical parts of the sales stack. To up your sales game, read on!
The Hole Truth: Via Integrity in an HDI World
From the drilled hole to registration across multiple sequential lamination cycles, to the quality of your copper plating, via reliability in an HDI world is becoming an ever-greater challenge. This month we look at “The Hole Truth,” from creating the “perfect” via to how you can assure via quality and reliability, the first time, every time.
In Pursuit of Perfection: Defect Reduction
For bare PCB board fabrication, defect reduction is a critical aspect of a company's bottom line profitability. In this issue, we examine how imaging, etching, and plating processes can provide information and insight into reducing defects and increasing yields.
- Articles
- Columns
- Links
- Media kit
||| MENU - pcb007 Magazine
Estimated reading time: 4 minutes
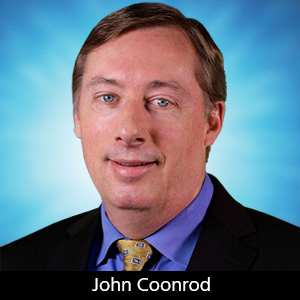
Lightning Speed Laminates: Thermal Management Isn’t Getting Easier
I haven’t written anything on thermal management for some time, and from my perspective, it continues to get more complicated as applications become more complex. Even applications at millimeter-wave frequencies, which typically use lower power, also have thermal management issues. It is a large topic, and this article will focus on practical issues related to PCB design and construction.
To start, heat can be generated for a circuit application in a variety of ways. Sometimes the heat is generated from an active device, sometimes from the resident power within the PCB, sometimes from the operating environment, and sometimes it is a mix of these issues. It is easier to deal with thermal management if you take one issue at a time.
Heating due to an active device usually occurs on the outside layer of a PCB and typically the heat needs to transfer through the PCB to a heat sink below. For this example, the main thermal issue is related to thermal conductivity of the PCB laminate(s) and the PCB design. For the PCB design, placing many grounding plated through-hole (PTH) vias near the heat source is commonly used. The via has copper plating. Copper is extremely high in thermal conductivity (~400 W/m?K) and the via can act like an efficient thermal path to the ground plane on the bottom of the circuit which would be in contact with the heat sink. In some cases, which often depends on the active device generating the heat, the grounding vias cannot be made and then the thermal conductivity of the laminate(s) becomes more critical.
Laminate thermal conductivity is typically in the range which would be regarded as a thermal insulator and not the desired thermal conductor. Most PCB laminates have a thermal conductivity of 0.2 to 0.4 W/m?K. There are some laminates which have higher thermal conductivity, and a laminate with one of the highest thermal conductivities comes from Rogers. This laminate has a thermal conductivity of 1.24 W/m?K and that is when testing the substrate only. In some evaluations for thermal conductivity, the laminate supplier will include the copper cladding and that will cause the reported thermal conductivity to be higher. Rogers does not test copper with the substrate and the thermal conductivity associated with this particular laminate is the value of the substrate only. Lastly on this subject, having a combination of PTH grounding vias that are used in conjunction with a laminate having high thermal conductivity is advantageous for thermal management.
A thermal management issue related to the circuit heating due to applied power is a different thermal management issue than previously discussed. In this case, the heat flow path through the circuit as previously mentioned still applies, however, there are other issues which need to be considered. In the case of the circuit being heated due to RF applied power, then the insertion loss becomes more important to consider. Basically, an increased insertion loss will cause an increase in heat generated. One tradeoff to consider is between thermal conductivity and insertion loss. If a circuit material has low thermal conductivity, it may still be acceptable if the material has very low loss. If the insertion loss is very low, there will be less heat generated and the thermal conductivity becomes less important. On the opposite end of that concern would be to use a material that has high thermal conductivity but is not as good for insertion loss. The poor insertion loss will generate more heat, but using a material with high thermal conductivity will have the heat move through the circuit efficiently. Ideally, it would be best to have a material that is very low for generating insertion loss and high for thermal conductivity.
Another complication with RF heating of the circuit is that different thicknesses of the circuit dielectric material will cause differences in insertion loss. A circuit using a thicker low loss substrate will generate less heat due to lower insertion loss, however the heat flow path through the material is now longer due to the substrate being thicker. The heat flow formula is thickness-dependent, and a thicker circuit will have a longer heat flow path and will not be more efficient at moving the heat through the circuit to the heat sink.
Additionally, the dielectric constant of the material can have an impact on thermal management. A circuit using a material with a low dielectric constant will cause the conductors to be wider. Having wider conductors will generate less insertion loss and less heat. Also, a wide conductor will have more surface area on the signal plane. Increased surface area on the signal plane will cause a wider heat flow path and the heat flow will be more efficient from the signal plane to the planes below.
The Rogers circuit material mentioned earlier is a high-frequency circuit material that is formulated to have good qualities for thermal management. When the laminate is evaluated at 10 GHz, it has a Dk of about 3.5, and dissipation factor of 0.0017. It has a thermal conductivity of 1.24 W/m?K, which is considered very good, and it is available in a variety of thicknesses. Additionally, the laminate is available with different copper types, and the reverse-treated copper foil that is available has a relatively smooth copper surface. The smoother copper can also support lower insertion loss, which will help to decrease the heat generated and make thermal issues better.
This column originally appeared in the October 2022 issue of Design007 Magazine.
More Columns from Lightning Speed Laminates
Lightning Speed Laminates: Millimeter-wave Properties and PCB Design ChallengesLightning Speed Laminates: Optimizing Thermal Management for Wireless Communication Systems
Lightning Speed Laminates: Test Vehicles for PCB Electrical Material Characterization
Lightning Speed Laminates: Optimum Thermal Stability Considerations
Lightning Speed Laminates: Benefits of High-Performance Hybrid Multilayer PCBs
Lightning Speed Laminates: An Overview of Copper Foils
Lightning Speed Laminates: The Importance of Circuit Features for Millimeter-Wave Applications
Lightning Speed Laminates: Prepreg Choices for Millimeter-wave PCB Applications