-
- News
- Books
Featured Books
- pcb007 Magazine
Latest Issues
Current IssueSales: From Pitch to PO
From the first cold call to finally receiving that first purchase order, the July PCB007 Magazine breaks down some critical parts of the sales stack. To up your sales game, read on!
The Hole Truth: Via Integrity in an HDI World
From the drilled hole to registration across multiple sequential lamination cycles, to the quality of your copper plating, via reliability in an HDI world is becoming an ever-greater challenge. This month we look at “The Hole Truth,” from creating the “perfect” via to how you can assure via quality and reliability, the first time, every time.
In Pursuit of Perfection: Defect Reduction
For bare PCB board fabrication, defect reduction is a critical aspect of a company's bottom line profitability. In this issue, we examine how imaging, etching, and plating processes can provide information and insight into reducing defects and increasing yields.
- Articles
- Columns
- Links
- Media kit
||| MENU - pcb007 Magazine
Estimated reading time: 4 minutes
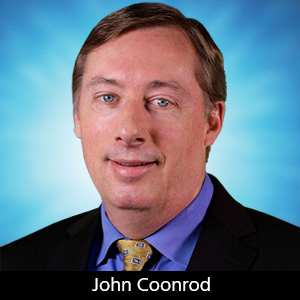
Lightning Speed Laminates: Test Vehicles for PCB Electrical Material Characterization
Electrical characterization of high frequency circuit materials can be done in a variety of ways. Some characterization methods use a fixture to test the raw dielectric material, while other methods use circuits. The Dk and Df results shown on material datasheets are commonly obtained by a fixture test method. However, when comparing results from circuit evaluations, the Dk results from the fixture tests occasionally do not agree with the Dk results of the circuit tests.
The reasons for these differences vary and are often situation dependent. In general, however, a fixtured test method will not have the same variables which will impact the Dk extraction, as compared to a circuit test. When using a circuit test, the Dk extraction will be affected by various aspects of PCB fabrication processing, such as conductor width control, copper thickness variations, final plated finish, and copper surface roughness.
A typical fixture test method will not have these PCB variations; instead, it may have variations due to entrapped air, fixture alignment variations, electrical coupling differences, and some tolerancing effect due to the machining of the fixture components. Additionally, the electromagnetic fields applied to the material under test can vary across test methods. The different field orientation also can be problematic when evaluating anisotropic circuit material. Most circuit materials used in the PCB industry are anisotropic, meaning that the Dk is not the same on all three axes of the material.
If the electrical characterization to be done is related to a PCB being built in large volume, the best test method and/or best test vehicle will be the one that is most like the actual circuit being built in volume production. If the electrical characterization is a project that will consider many different types of circuit materials for qualification for future projects, it may be best to use the same fixtured test method for all materials. If the same test method is used and is well understood, the evaluation should be relatively impartial to the materials being tested. However, since different circuit materials have different processing needs for the circuit fabrication process, it may not be a good comparison to evaluate different circuit materials using the same circuit test method.
There are many test vehicle options available for circuit test methods. Some of the more common circuit test vehicles include ring resonators and transmission line circuits with different lengths; antenna patch radiators, 180-degree hybrids, edge-coupled filters, and delay lines are additional options.
Ring resonators have been used for material characterization for many years and with good success. But over the past several years, and with more applications using millimeter-wave (mmWave) frequencies, obtaining accurate results when using ring resonator test vehicles has become problematic. Wavelength can be a simple way to think about these challenges, as related to lower and higher frequency. At mmWave frequencies, wavelengths are very small, and the propagating wave will be more sensitive to circuit anomalies, which can cause RF disturbances. These small circuit anomalies may be normal for circuit fabrication and may not cause any difference in RF performance when operating at lower frequencies with longer wavelengths.
Many ring resonators are gap coupled; differences in the gap coupling can influence the ring resonator’s center frequency, which impacts the Dk extraction accuracy. The RF differences due to the gap are usually related to etching and copper thickness variation. If the same ring resonator design is used for two circuits built at different times and one circuit has thicker copper than the other, the circuit with the thicker copper will have more fields fringing in air than the circuit with thinner copper. Air has a very low Dk and having more fields in air will naturally lower the extraction of the Dk value. The lower Dk result will be related to the circuit fabrication process rather than the circuit material. The conductor trapezoidal shape and its normal variation from circuit to circuit can also impact the RF performance due to affecting the fields in the gap coupled areas. Again, at lower frequencies, these small differences due to coupling will be less significant, but at mmWave frequencies the differences can be substantial.
There are also copper surface roughness effects to consider for Dk extraction. The copper surface in this case refers to the copper surface at the substrate-copper interface as the laminate is made. When the copper is rough, it will slow the wave propagation and alter the RF performance. The copper surface roughness is not perfect and there is normal variation in roughness from batch to batch of the same copper foil. For a microstrip ring resonator, the copper roughness will not be the same for the signal plane as the ground plane, due to this normal variation in roughness. At lower frequencies, the differences in roughness are less significant than at mmWave frequencies. The copper roughness and its variation are other issues to consider for the test vehicle being used at higher frequencies.
There are many test methods and test vehicles that can be used to characterize high frequency circuit materials. Designers should contact the material supplier to inquire how the published Dk was obtained, as well as ask for test method recommendations that are appropriate to the RF design being considered.
This column originally appeared in the February 2023 issue of Design007 Magazine.
More Columns from Lightning Speed Laminates
Lightning Speed Laminates: Millimeter-wave Properties and PCB Design ChallengesLightning Speed Laminates: Optimizing Thermal Management for Wireless Communication Systems
Lightning Speed Laminates: Optimum Thermal Stability Considerations
Lightning Speed Laminates: Thermal Management Isn’t Getting Easier
Lightning Speed Laminates: Benefits of High-Performance Hybrid Multilayer PCBs
Lightning Speed Laminates: An Overview of Copper Foils
Lightning Speed Laminates: The Importance of Circuit Features for Millimeter-Wave Applications
Lightning Speed Laminates: Prepreg Choices for Millimeter-wave PCB Applications