-
- News
- Books
Featured Books
- pcb007 Magazine
Latest Issues
Current IssueSales: From Pitch to PO
From the first cold call to finally receiving that first purchase order, the July PCB007 Magazine breaks down some critical parts of the sales stack. To up your sales game, read on!
The Hole Truth: Via Integrity in an HDI World
From the drilled hole to registration across multiple sequential lamination cycles, to the quality of your copper plating, via reliability in an HDI world is becoming an ever-greater challenge. This month we look at “The Hole Truth,” from creating the “perfect” via to how you can assure via quality and reliability, the first time, every time.
In Pursuit of Perfection: Defect Reduction
For bare PCB board fabrication, defect reduction is a critical aspect of a company's bottom line profitability. In this issue, we examine how imaging, etching, and plating processes can provide information and insight into reducing defects and increasing yields.
- Articles
- Columns
- Links
- Media kit
||| MENU - pcb007 Magazine
Estimated reading time: 4 minutes
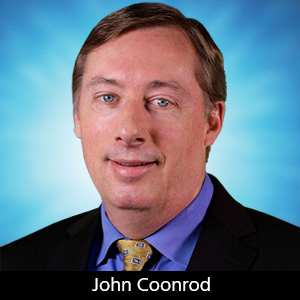
Lightning Speed Laminates: An Overview of Copper Foils
Copper foils used in the PCB industry are deceptively complex. Copper is an excellent electrical conductor and thermal conductor, which makes copper foil ideal for the conductive layers of most PCB applications. There are many other copper foil properties which are important for an engineer to understand.
The copper foils used in the PCB industry are typically made as rolled wrought copper (rolled annealed copper or RA) or as electro-deposited (ED) copper. Rolled copper is made by starting off with a copper billet and then going through successive rolling processes to reduce the copper billet to a copper foil at the desired thickness. ED copper is made with an electrolytic plating process, where copper is plated on a large drum and peeled off as copper foil while the drum rotates. The speed of the drum rotation will dictate the thickness of the copper foil. After the copper foils are made, both RA and ED copper go through several processes to apply treatments to the copper.
There are many varieties of treatments applied to the copper and for many different reasons. Some treatments are a passivation treatment to ensure the copper does not oxidize until the consumer uses it. Other treatments are applied to the copper to help with good chemical bonding with certain resin systems (e.g., PPE vs. PTFE). Due to differences in the resin system, the materials react differently to the various treatments. Since each resin system has different bonding characteristics, some treatment/resin combinations will be better than others for achieving a good bond. There are also copper treatments used to ensure proper bonding when exposed to high temperatures. Additionally, there are other treatments that can be applied to the copper foil to support a reliable bond interface when considering long-term elevated temperature exposures.
For most rigid PCB applications, ED copper is the most popular, however RA copper is used as well. Generally, RA copper is typically more expensive than ED copper. RA copper is often not used unless there are specific properties of rolled copper that can be beneficial to the application. Due to the nature of how RA copper is made, it has a very smooth surface. A smooth copper surface is advantageous for high frequency and very high-speed digital applications, where having lower insertion loss is desired. Another property of rolled copper that is innate to the copper manufacturing process is the in-plane grain structure that is very good for applications where bending the circuit is necessary. One technical drawback to RA copper, which is also related to the grain structure, is that the etching of fine circuit features can be problematic. This can be overcome to some degree, with specific etching conditions tailored to RA copper.
ED copper is widely used throughout the PCB industry. There are many different types of ED copper and typically they are classified by surface roughness and/or treatment. IPC has different classifications for ED copper based on copper roughness. Examples of a few of the classifications are LP (low profile), VLP (very low profile), and HVLP (hyper very low profile).
Copper roughness measurements can be confusing due to different methodologies. Generally, there are two categories for roughness measurements: contact measurements and non-contact measurements. The contact measurements use a physical probe, a stylus, to measure the peaks and valleys of the copper surface. The non-contact measurements are typically using reflected light or laser measurements to determine the peaks and valleys of the surface.
The contact profilometers can be less accurate due to the stylus tip size, where the stylus may not be able to resolve the depth of a very narrow valley. Also, the stylus can “plow” through the peaks and not get an accurate measurement. Those who are experienced with this technique understand these issues and there are some adjustments that can be done to mitigate the accuracy concern. However, as a general statement, the non-contact profilometers are typically more accurate than the contact profilometers for fine-grain copper types.
There are many ways to describe the surface roughness profile. Engineers working directly with the PCB fabrication will typically want to use the Rz profile, which is the peak-to-valley measurement over a sample area, defined by multiple line measurements. If the Rz profile is measured as an area (not a line measurement), the Rz profile would be designated as Sz. The engineers working with electromagnetic modeling software for high frequency or high-speed digital (HSD) will often want the Rq or Sq profile of the surface. The electromagnetic modeling industry has found good correlations between the Rq or Sq profiles and the surface impact on RF or HSD performance. The Rq and Sq are basically the root mean square of the surface roughness when measured with many samples.
There is also another property of surface roughness which the modeling industry is interested in: the surface area index (SAI), sometimes called the surface area ratio. This roughness number can be used for a specific electromagnetic model which has shown good accuracy across very wide bandwidths. The SAI is basically the roughness of a scan area as compared to that same area with an ideal flat surface.
This column gives a simple introduction to copper foils for PCBs. For more information on the copper foils used in the PCB industry, visit the Rogers Technology Support Hub on the Rogers’ website, and view the Application Note, “Copper Foils for High Frequency Materials.”
This column originally appeared in the June 2022 issue of Design007 Magazine.
More Columns from Lightning Speed Laminates
Lightning Speed Laminates: Millimeter-wave Properties and PCB Design ChallengesLightning Speed Laminates: Optimizing Thermal Management for Wireless Communication Systems
Lightning Speed Laminates: Test Vehicles for PCB Electrical Material Characterization
Lightning Speed Laminates: Optimum Thermal Stability Considerations
Lightning Speed Laminates: Thermal Management Isn’t Getting Easier
Lightning Speed Laminates: Benefits of High-Performance Hybrid Multilayer PCBs
Lightning Speed Laminates: The Importance of Circuit Features for Millimeter-Wave Applications
Lightning Speed Laminates: Prepreg Choices for Millimeter-wave PCB Applications