-
- News
- Books
Featured Books
- pcb007 Magazine
Latest Issues
Current IssueInventing the Future with SEL
Two years after launching its state-of-the-art PCB facility, SEL shares lessons in vision, execution, and innovation, plus insights from industry icons and technology leaders shaping the future of PCB fabrication.
Sales: From Pitch to PO
From the first cold call to finally receiving that first purchase order, the July PCB007 Magazine breaks down some critical parts of the sales stack. To up your sales game, read on!
The Hole Truth: Via Integrity in an HDI World
From the drilled hole to registration across multiple sequential lamination cycles, to the quality of your copper plating, via reliability in an HDI world is becoming an ever-greater challenge. This month we look at “The Hole Truth,” from creating the “perfect” via to how you can assure via quality and reliability, the first time, every time.
- Articles
- Columns
- Links
- Media kit
||| MENU - pcb007 Magazine
Estimated reading time: 5 minutes
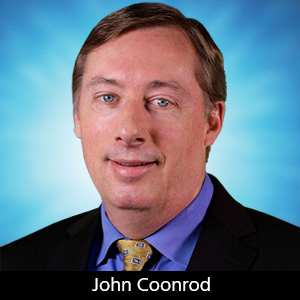
Lightning Speed Laminates: The Importance of Circuit Features for Millimeter-Wave Applications
Over the past several years there has been a steady increase in millimeter-wave (mmWave) applications. This was probably sparked by the chip industry, which has the capability to produce chips in large volume that have good mmWave performance. As the mmWave applications increased, most aspects of the electronics industry, including the PCB industry, were forced into a steep learning curve. As a general statement, the quality of the circuit board is more critical to mmWave applications as compared to lower frequency applications. To be more specific, the quality concerns are mostly related to consistency of circuit features such as conductor widths, conductor shapes, conductor spacing, substrate thickness, copper thickness, and final plated finishes.
Millimeter-wave applications are more sensitive to circuit features, due to wavelength. Wavelength is the physical length of a propagating wave and, as an example, the physical length of a wave at 3.3 GHz is about 2.3 inches. That is assuming a microstrip built on a thin laminate with a Dk of approximately 3.0. Within that 2.3 inches, the wave is made up of 360 degrees, which is also referred to as phase angles. If the propagating wave encounters an anomaly which is 0.023" in size, this is the same thing as 1% of the wavelength or about 3.6 degrees. This small anomaly, in relation to the wavelength, will have very little effect on the propagating wave. However, at a mmWave frequency, such as 77 GHz, the physical length of the wave is about 0.095" and if the same 0.023"-sized anomaly is part of the propagating wave path, it is now equivalent to 24% of the wavelength or about 87 degrees of the wave. Having a 24% portion of the wave affected by an anomaly may have an impact on the propagating wave and cause distortion and other unwanted wave properties.
Additionally, at mmWave frequencies, the high frequency material used in the PCB construction is typically thin. A thin laminate will translate to a narrower conductor to maintain a certain impedance. A typical conductor etching tolerance of ± 0.5 mil is usually acceptable for most lower frequency applications, but with mmWave applications this tolerance may not be tight enough to give good RF results. The reason is a narrower conductor with a total variation of 1 mil will have more impedance shift, as compared to a wider conductor. Some impedance matching networks in the antenna array areas of the auto radar sensor have conductors as small as 5 mils in width. A difference of 5 to 6 mils on a thin substrate can be a difference of 6 ohms impedance. However, when using a thicker substrate for lower frequencies and the appropriate wider conductor to maintain a given impedance, a 1 mil difference in conductor width will make an impedance difference of less than 1 ohm. There are many items in circuit fabrication which can alter the impedance of a circuit and having very good etching control is a major advantage for a PCB fabricator working with mmWave applications.
There are several different RF structures used in mmWave applications, and the structure that is normally least affected in RF performance by the normal variations in circuit fabrication processes is microstrip. The microstrip construction is typically the top two conductor layers on a multilayer RF board and has a signal conductor on top and a ground plane below. Another structure often used in mmWave circuitry is grounded coplanar waveguide (GCPW). This structure is also a two-copper layered circuit; however, the top signal plane has three conductors electrically oriented as ground/signal/ground. This configuration is very good to minimize certain unwanted wave characteristics at mmWave frequencies, however this structure may be impacted more by normal variations of circuit fabrication.
The space between the ground/signal/ground in the GCPW is critical and if that space varies much, so will the RF performance of the circuit. However, it is more complicated than that. On the top signal plane, there are strong electric fields between the neighboring ground planes which are on both sides of the signal conductor. In a cross-sectional view, if the sidewalls of these conductors are straight, there will be more fields in air. However, if the conductors are trapezoidal shaped, there will be fewer fields in air and more fields in the substrate. The difference of these fields being in air impacts the effective Dk the propagating wave experiences. Air has a Dk of about 1 and when the fields use more air, the wave will experience a lower effective Dk, and that can impact multiple RF circuit properties. That is especially true at mmWave frequencies. To have more consistent RF performance when using a GCPW at mmWave frequencies, controlling the conductor width and spacing is important, but having a consistent conductor shape is also very important.
There are many things to consider in the circuit fabrication process for achieving a consistent conductor width, space, and shape. The image and etching process using an additive process is often better than a subtractive process for conductor shape consistency. However, even with the additive process, there can be concerns for trapezoidal shaped conductors. It is usually a flipped trapezoidal shape as compared to the same concern when using the subtractive process.
Another item which can assist in consistent conductor shape and etching control is using thinner copper. Thinner copper will naturally give less trapezoidal shape and controlling the etching of the conductor width and space is easier. Rogers Corporation has several high frequency circuit materials which are used in mmWave applications with a laminate available with one-quarter ounce (9 µm) copper. Using this laminate with very thin copper can be beneficial for the PCB fabricator to have more consistent conductor shape, width, and spacing.
Millimeter-wave applications are more sensitive to circuit feature variability, as well as small circuit anomalies, which may have been acceptable for lower frequency applications. The PCB fabricator is challenged to control conductor widths and spacing to a tighter requirement and the shape of the signal conductor also needs to be more consistent. Additive processing at the PCB fabricator can be beneficial for these mmWave circuit requirements and using a laminate with thin copper can also be advantageous.
This column originally appeared in the April 2022 issue of Design007 Magazine.
More Columns from Lightning Speed Laminates
Lightning Speed Laminates: Millimeter-wave Properties and PCB Design ChallengesLightning Speed Laminates: Optimizing Thermal Management for Wireless Communication Systems
Lightning Speed Laminates: Test Vehicles for PCB Electrical Material Characterization
Lightning Speed Laminates: Optimum Thermal Stability Considerations
Lightning Speed Laminates: Thermal Management Isn’t Getting Easier
Lightning Speed Laminates: Benefits of High-Performance Hybrid Multilayer PCBs
Lightning Speed Laminates: An Overview of Copper Foils
Lightning Speed Laminates: Prepreg Choices for Millimeter-wave PCB Applications