-
- News
- Books
Featured Books
- smt007 Magazine
Latest Issues
Current IssueMoving Forward With Confidence
In this issue, we focus on sales and quoting, workforce training, new IPC leadership in the U.S. and Canada, the effects of tariffs, CFX standards, and much more—all designed to provide perspective as you move through the cloud bank of today's shifting economic market.
Intelligent Test and Inspection
Are you ready to explore the cutting-edge advancements shaping the electronics manufacturing industry? The May 2025 issue of SMT007 Magazine is packed with insights, innovations, and expert perspectives that you won’t want to miss.
Do You Have X-ray Vision?
Has X-ray’s time finally come in electronics manufacturing? Join us in this issue of SMT007 Magazine, where we answer this question and others to bring more efficiency to your bottom line.
- Articles
- Columns
- Links
- Media kit
||| MENU - smt007 Magazine
Estimated reading time: 1 minute
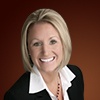
The Short Scoop: The Ins and Outs of Step Stencils
The demand for step stencils is increasing, but why? The answer: shrinking components. In the early days of SMT assembly, step stencils were used to reduce the stencil thickness for 25 mil pitch leaded device apertures. However, as SMT requirements became more complex and, consequently, more demanding, so did the requirements for complex step stencils. Today, fine-pitch components, which necessitate a thin stencil for acceptable paste release, are sandwiched beside a variety of devices and components that require higher paste height. Getting the solder paste volume needed for larger components, while still having an area ratio that allows for good paste release on small components, can be challenging. Step stencils offer the SMT process engineer significant flexibility in achieving the proper solder paste height and volume for the overall paste printing process.
Step stencils range from simple designs to complex multi-thickness steps. With them you can print different paste heights, with one stencil, in one print. Without them, a separate print run and stencil might be needed for each solder paste height or a manual application for additional paste deposit required. Using a step stencil is much faster, prints an actual solder brick, and allows for solder paste volume control. Dispensing and other printing methods are slower, many times more manual, yield less control on solder paste volume, and usually require a second step, after initial printing.
Step stencils are available in all stencil technologies: Electroformed, laser cut, and chemical etched. These steps are usually etched or electroformed depending on the application and the area ratio. Although traditionally etching was used for most stencil manufacturing and aperture formation, etching is now predominantly used for step stencils. The thickness of the step areas and the overall thickness of the stencil are determined by the area ratio of the component. Step stencils have a primary base thickness and step-up or step-down areas across the board pattern depending on the thickness and volume of solder paste a particular component requires. Read the full column here.Editor's Note: This column originally appeared in the August 2013 issue of SMT Magazine.
More Columns from The Short Scoop
Adapting Stencils to Manufacturing Challenges in 2015The Short Scoop: Stencil Printing in PCB Cavities
The Short Scoop: Printing Two-level PCBs in One Step with a 3D Electroform Stencil
The Short Scoop: Improving Stencil Printing Results
The Short Scoop: More Stencil Questions (and the Answers!)
The Short Scoop: Selecting a Stencil Frame
The Short Scoop: Screen Printing Solutions for Small Die & Precision
The Short Scoop: 10 Common Stencil Questions