-
- News
- Books
Featured Books
- smt007 Magazine
Latest Issues
Current IssueMoving Forward With Confidence
In this issue, we focus on sales and quoting, workforce training, new IPC leadership in the U.S. and Canada, the effects of tariffs, CFX standards, and much more—all designed to provide perspective as you move through the cloud bank of today's shifting economic market.
Intelligent Test and Inspection
Are you ready to explore the cutting-edge advancements shaping the electronics manufacturing industry? The May 2025 issue of SMT007 Magazine is packed with insights, innovations, and expert perspectives that you won’t want to miss.
Do You Have X-ray Vision?
Has X-ray’s time finally come in electronics manufacturing? Join us in this issue of SMT007 Magazine, where we answer this question and others to bring more efficiency to your bottom line.
- Articles
- Columns
- Links
- Media kit
||| MENU - smt007 Magazine
Estimated reading time: 1 minute
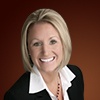
The Short Scoop: Screen Printing Solutions for Small Die & Precision
The Short Scoop this month discusses one of our more demanding customer applications. As discussed in previous articles, when selecting stencils, the trick is choosing the right tool for the right job; but sometimes the need for tailoring a stencil for a specific application can take a bit more engineering time and several iterations to get the desired results.As a case study, consider this: Recently, a customer was trying to print solder fillets on gold Kovar tabs. The Kovar tab measured just 0.063 +/- 0.002 x 0.125 +/- 0.002 inches. The tab was finish plated with 150 µin (minimum) of nickel and then over-plated with 100 µin (minimum) of gold. When the component was attached, the solder fillet needed to align precisely with the tab and the solder reflow had to be perfect. For this demanding application, there could be no gas pockets or voids anywhere on the fillet, which meant that ensuring sufficient venting for flux residue from under the part was a priority. The plan was to use a stencil and a squeegee to transfer the solder onto the fillet. However, getting a successful plot was extremely difficult.
Previously, the customer had been processing the parts by hand-soldering them onto the assembly. At this point in their manufacturing process, they decided to use machine placement for a more accurate and repeatable result and to speed throughput to accommodate increasing volumes.
The stencils they had been working with had six apertures distributed over the large pad for the Kovar tab (slug). Using the initial design configuration of apertures to print the solder paste did not allow sufficient solder paste solvent to escape during reflow. This lack of adequate solvent escape was causing voids under the Kovar tab as well as poor solder fillets on the edge of the Kovar tab during reflow. Both of these defects were unacceptable conditions for the exacting assembly standards required for the end product.
In the customer’s own words, “We had set extremely high standards because the fillet of the solder on this part needed to be perfect. We had tried many stencils and made many plots, but they all resulted in failures.” Read the full column here.Editor's Note: This column originally appeared in the April 2014 issue of SMT Magazine.
More Columns from The Short Scoop
Adapting Stencils to Manufacturing Challenges in 2015The Short Scoop: Stencil Printing in PCB Cavities
The Short Scoop: Printing Two-level PCBs in One Step with a 3D Electroform Stencil
The Short Scoop: Improving Stencil Printing Results
The Short Scoop: More Stencil Questions (and the Answers!)
The Short Scoop: Selecting a Stencil Frame
The Short Scoop: 10 Common Stencil Questions
The Short Scoop: Electroformed Stencils