-
- News
- Books
Featured Books
- design007 Magazine
Latest Issues
Current IssueProper Floor Planning
Floor planning decisions can make or break performance, manufacturability, and timelines. This month’s contributors weigh in with their best practices for proper floor planning and specific strategies to get it right.
Showing Some Constraint
A strong design constraint strategy carefully balances a wide range of electrical and manufacturing trade-offs. This month, we explore the key requirements, common challenges, and best practices behind building an effective constraint strategy.
All About That Route
Most designers favor manual routing, but today's interactive autorouters may be changing designers' minds by allowing users more direct control. In this issue, our expert contributors discuss a variety of manual and autorouting strategies.
- Articles
- Columns
- Links
- Media kit
||| MENU - design007 Magazine
Estimated reading time: 2 minutes
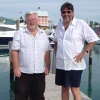
Bob and Me: Tarzwell's First--and Last--Lean Meeting
Dan Beaulieu: While we were working with one or our clients a few years back, the firm decided to get involved in the whole Lean manufacturing thing. They were a big enough company that they were able to hire the real guys: The ones who had gone to Japan to work with Toyota and then had written a book about it. They later sold their ideas to a number of large companies including the one we were working with. Now they were here and in our face! We were told that as part of our gig, we were going to have to play nice with these guys.
Out of all my guys, Bob Tarzwell was the first of my team to attend one of these Lean meetings. This was possibly the worst guy we could have sent, but I knew that and our contact at the client’s office knew it too, so they could play their games and we could play ours.
I’ll let Bob tell you all what happened, in his own inimitable way.
Bob Tarzwell: First, the “Lean lady” asked everyone what they did and how long it took them to do it. Then there was someone who, for some reason that I could not figure out, brought up the fact that the shelves were in the wrong place and that if they were in the right place it would increase the efficiency of the department. So, acting as proactively as they could, they took all of us to stare at those shelves and then held a brainstorming session on what we should do. Have you ever seen a decision tree? A fish scale pattern thingy? Well, they started working on one of those for those shelves. Actually, I have to say that moving the shelves was a pretty good idea, and they should have just done it instead of talking about it for hours.
But there was only one problem with moving the shelves: A fire extinguisher hung exactly where we wanted to move them. Now, that brought everything to a stop.
First, there was a big discussion about where fire extinguishers were supposed to go, how they were supposed to be hung, how high they were supposed to be hung, and how near the door frame they were supposed to be.
They sent someone out to find an OSHA rule booklet and then they started looking at that. It was such a waste of time. I wanted to kill somebody--either myself or maybe the facilitator.Read the full column here.Editor's Note: This column originally appeared in the October 2014 issue of The PCB Design Magazine.
More Columns from Bob and Me
Controlled Impedance: A Real-World Look at the PCB SideBob and Me: The Key to Increasing Quality - Bribe Your Employees
Bob and Me: A PCB Potpourri
Bob and Me: Spacing is Irrelevant Below 270 Volts
PCB 101: Coefficient of Thermal Expansion
The Bleeding Edge: Serious as a Heart Attack
PCB101: Fabricating High-Voltage Boards
New Column: PCB 101