-
- News
- Books
Featured Books
- smt007 Magazine
Latest Issues
Current IssueMoving Forward With Confidence
In this issue, we focus on sales and quoting, workforce training, new IPC leadership in the U.S. and Canada, the effects of tariffs, CFX standards, and much more—all designed to provide perspective as you move through the cloud bank of today's shifting economic market.
Intelligent Test and Inspection
Are you ready to explore the cutting-edge advancements shaping the electronics manufacturing industry? The May 2025 issue of SMT007 Magazine is packed with insights, innovations, and expert perspectives that you won’t want to miss.
Do You Have X-ray Vision?
Has X-ray’s time finally come in electronics manufacturing? Join us in this issue of SMT007 Magazine, where we answer this question and others to bring more efficiency to your bottom line.
- Articles
- Columns
- Links
- Media kit
||| MENU - smt007 Magazine
Estimated reading time: 1 minute
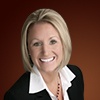
The Short Scoop: Printing Two-level PCBs in One Step with a 3D Electroform Stencil
The requirements for two-level PCBs with components on both levels have seen a recent increase. Stencil printing on both levels requires special stencil and squeegee blade designs. Recently, we participated in two experiments. The purpose was to determine if a 3D electroform stencil, in just one printing step, could be used to print a two-level board with cavities. The tests consisted of:
- Printing solder paste for 0.3µm µBGAs with pads on two levels (steps) of a flexible PCB separated by 7 mils (175µm).
- Printing flux and solder paste into a recessed area on a PCB for an embedded flip-chip with a cavity depth of 14 mils (350µm).
The printing tool used was a single thickness 4 mil (100µm) thick 3D electroform stencil with apertures consisting of 10 mil (250µm) circles. Printing was done in two modes: A step mode for the two levels and a reservoir mode for the recessed pocket. Although two-step stencils are commonly used for these applications, our tests used 3D electroform stencils for both print experiments.
In this The Short Scoop, I will present the printing results obtained from the step print mode. Next month’s column will present the print test results from the reservoir print mode.
For the step print mode we used four different squeegee blades. We found that the squeegee blade was a significant factor in determining the printing quality and results.
Stencil, Board, and Squeegee Blade Set-Up
The step print test vehicle was a flex circuit having a 7 mil (175µm) thick stiffener attached to the back side of the circuit as a step-up. The front side of the flex circuit was flat with a 0.260 mm pitch flip-chip component and several µBGAs. The flex and stiffener surfaces were separated by the stiffener height. µBGA patterns printed on top of the stiffener were positioned at 25 mils (0.64 mm), 50 mils (1.28 mm), and 100 mils (2.54 mm) from the step edge of the stencil. A shim was attached to the flex to simulate a flip-chip cavity embedded 14 mils (355µm) deep.
The task was to use a 3D electroform stencil to print on two surfaces of the backside of the flex at the same time. Solder bricks were printed on the 0.4 mm µBGA on the left side of the flex and on the surface of the stiffener.Read the full column here.Editor's Note: This column originally appeared in the December 2014 issue of SMT Magazine.
More Columns from The Short Scoop
Adapting Stencils to Manufacturing Challenges in 2015The Short Scoop: Stencil Printing in PCB Cavities
The Short Scoop: Improving Stencil Printing Results
The Short Scoop: More Stencil Questions (and the Answers!)
The Short Scoop: Selecting a Stencil Frame
The Short Scoop: Screen Printing Solutions for Small Die & Precision
The Short Scoop: 10 Common Stencil Questions
The Short Scoop: Electroformed Stencils