-
- News
- Books
Featured Books
- pcb007 Magazine
Latest Issues
Current IssueInventing the Future with SEL
Two years after launching its state-of-the-art PCB facility, SEL shares lessons in vision, execution, and innovation, plus insights from industry icons and technology leaders shaping the future of PCB fabrication.
Sales: From Pitch to PO
From the first cold call to finally receiving that first purchase order, the July PCB007 Magazine breaks down some critical parts of the sales stack. To up your sales game, read on!
The Hole Truth: Via Integrity in an HDI World
From the drilled hole to registration across multiple sequential lamination cycles, to the quality of your copper plating, via reliability in an HDI world is becoming an ever-greater challenge. This month we look at “The Hole Truth,” from creating the “perfect” via to how you can assure via quality and reliability, the first time, every time.
- Articles
- Columns
- Links
- Media kit
||| MENU - pcb007 Magazine
Estimated reading time: 4 minutes
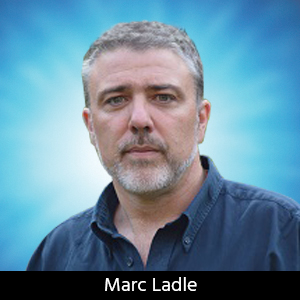
Ladle on Manufacturing: Time to Show our Hand?
It can be quite tough to satisfy the product requirements of the military and aviation industries, and rightly so. There are not many other parts that we manufacture that could result in a life-threatening situation should they fail when they are in use.
Once a product has been qualified, the process route may leave very little room for maneuver. The nature of many of these products is that they may have a long life-cycle so these restrictions can make process changes very difficult.
Some processes such as tin-lead solder have had to be maintained just for this type of application and there are no signs that the requirement is going to disappear soon.
For fabricators, this puts them in quite a difficult position. If they want to be able to compete for this type of work, they must maintain a process or multiple processes that may only be called into action when there are military or aerospace boards in manufacture. Real estate inside the factory is expensive so this is a big ask for any company.
There is also a large time commitment to manufacturing these products. The maintenance of the approvals and the inspection and testing which relate to these circuits mean that many working hours are required, regardless of whether you make one batch of boards or one hundred. To make things worse, there is never any guarantee that you will get the contract. You can commit 100% to meeting the required standards and still fail to get a single order.
I have spent plenty of time working directly in bare board fabrication plants—enough time to know that the salesmen have a tough job to do. They have targets to meet and sales is a competitive sport. If your profit margins are too large you will never get the order! To some ex tent the same is true when manufacturing mil/aero products. When the salesman delivers the quote, it is critical that he understands the extra commitment and time which will be demanded to manufacture these products.
I am not directly involved in this process anymore so I feel reasonably comfortable suggesting that, as an industry, we need a more joint approach to the whole process. We are all in business to make a reasonable profit. I think all too often it is easy to lose sight of the actual costs of manufacturing occasional batches of special boards. You may be competing against a company who have not considered the whole picture when they have put forward their quote.
Even worse, with the buyer dangling the carrot of future batches and related projects, loss leaders and special prices may hit the table. In the long term, it is impossible to compete against this type of approach—nobody wins. The buyer gets a very false impression of the true cost of their boards. It is simply not sustainable.
I would not usually be the person to suggest that extra red tape be added to the process, but in this case perhaps it could help. The manufacturing standards for these products are very detailed and each important process must be carried out in a way that is approved and assures the quality of the end product.
Why not have a detailed standard for the purchase cycle? An approved method for the calculation of process costs and inclusion of the detailed costs for the inspection and verification processes. Putting these prices forwards as an open book to the buyer. What would I propose in return? A reasonable specified profit margin which reflects the effort and commitment put in by the fabricator. Only with this
type of open policy is it possible for the buyer to understand if a pricing model is sustainable and correctly calculated. Then we can truly compete on a level playing field.
Particularly for the military applications, I feel quite strongly that we should be supportive as an industry to make sure they have access to products manufactured to the very best of our ability. The nature of conflicts around the world is changing and there is ever more reliance on specialised electronics to keep both military personnel and civilians safe.
My perspective has changed as I have gotten older. As a teenager, I had friends who joined the UK armed forces. Some of them joined the elite Royal Marines and Paratroop regiments. At the time, I respected the physical commitment they gave to their job. As my children have grown up and some of their friends joined the armed forces I feel I understand better the nature of the job they are doing for their country. Young men and women who are prepared to make huge sacrifices to protect the innocent.
I may not agree with the politics involved but I absolutely support every member of our military who is prepared to offer their service and potentially their life for our benefit. If we can improve our service to them, we must!
Marc Ladle is director at Viking Test Ltd. To contact him or to read past columns, click here.
Editor's Note: This column originally appeared in the July 2017 issue of The PCB Magazine, click here.
More Columns from Ladle on Manufacturing
Ladle on Manufacturing: LED UV Cure—Does It Really Work?Ladle on Manufacturing: UV Cure LED Energy Saver
Ladle on Manufacturing: Sharing an Idea for Christmas
Ladle on Manufacturing: Behind the Scenes at productronica 2019
Ladle on Manufacturing: Sunday Afternoon in Dongguan
The Travelling Engineer, Installment 2
Ladle on Manufacturing: VCP—The Future of Plating
Developments in Wet Processing: Beyond Spraying and Dipping