-
- News
- Books
Featured Books
- pcb007 Magazine
Latest Issues
Current IssueInventing the Future with SEL
Two years after launching its state-of-the-art PCB facility, SEL shares lessons in vision, execution, and innovation, plus insights from industry icons and technology leaders shaping the future of PCB fabrication.
Sales: From Pitch to PO
From the first cold call to finally receiving that first purchase order, the July PCB007 Magazine breaks down some critical parts of the sales stack. To up your sales game, read on!
The Hole Truth: Via Integrity in an HDI World
From the drilled hole to registration across multiple sequential lamination cycles, to the quality of your copper plating, via reliability in an HDI world is becoming an ever-greater challenge. This month we look at “The Hole Truth,” from creating the “perfect” via to how you can assure via quality and reliability, the first time, every time.
- Articles
- Columns
- Links
- Media kit
||| MENU - pcb007 Magazine
Estimated reading time: 5 minutes
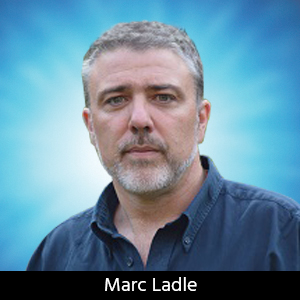
Ladle on Manufacturing: Sharing an Idea for Christmas
I have been considering the possibilities of the idea I am going to describe in this column for quite a few years now. There is a good opportunity here, but I think it may be of more use to other people than it is for me, so I have decided to share in an open forum and hope that it turns out to be useful (or at least interesting) for some of you circuit people or electronic material manufacturers out there.
Many years ago, while working in a U.K. PCB factory, I inspected some panels after they had come through a multilayer lamination process and found some resin spots on the surface. Nothing particularly surprising there! From time to time, small pieces of prepreg find their way onto the surface of the copper foil during the layup stage, and when the press cycle is run, they cure themselves onto the surface of the foil.
In this case, rather than remove them, I wanted to track them through the subsequent processes to see exactly how they may turn into faults on the panels. And, if I am honest, there were no big surprises. The resin stood up to the etch process with no signs of deterioration, and the spot of resin turned into exactly the same shape of excess copper. The conclusion: Cured prepreg definitely works as well as an etch resist.
From time to time, the same idea kept coming back to me: Could it be possible to substitute dry-film etch resist for a resin (prepreg) etch resist at the inner layer stage? It could be an opportunity to reduce the complexity of the inner layer manufacturing process.
I made a very low-key trial of the basic process sequence I had in mind. I used a thin layer of resin (as thin as I could screen print), and heat cured it onto the surface of a piece of copper-clad inner layer base material. I then removed some of the resin to make a pattern using a cheap fibre laser and ran it through a normal etch process afterward. It took me a few goes to get a respectable result, as the laser ablation process produced enough by-product (which stuck pretty well to the copper) to prevent a clean etch the first time. But it was not too tough to solve, as the laser waste was nowhere near as resilient as the rest of the cured resin; after a light, abrasive clean, I was able to get a respectable etching result.
At this point, I considered the possibilities of the new process route, and it occurred to me that the base material could be supplied in a pre-coated state. This certainly would offer the advantage that the copper surface would be well protected and completely clean at the point of delivery to the manufacturing process. It also removes the requirement for any kind of chemical or abrasive pre-clean, as the laser process is not sensitive to this type of surface contamination. Straightaway, one process stage would be removed, along with the fact that there’s no need:
- To laminate dry film
- For mylar peeling or dry film developing
- For dry film stripping
- For pre-lamination copper treatment (alternative oxide or similar)
Finally, the part that got me interested in the first place was because the resin is part of the normal build-up of the circuit board, there is no need to remove it before putting the sandwich of layers together. The same pre-prepared copper surface that was locked in underneath the resin as delivered from the material supplier can pass directly to the bonding process to be made into a multilayer panel.
Processing inner layers with blind and buried via holes may need some significant thought to adopt a similar production route. I have a few ideas for this, but, for the moment, I will stick to the basic concept of improving the print and etch method of inner layer production. The basic idea still seems very appealing to me. The removal of quite a number of process stages, and the liberation of a decent area of real estate within a multilayer PCB factory, has to be a decent win.
But that is probably not the most attractive part. New technologies require faster and faster signal speeds. As the signal speed increases the roughness of the copper surface becomes more and more relevant to the quality of the end result. High-speed signals travel closer to the surface the faster they go and follow the topography of the copper. So, the rougher the copper is, the further the signal needs to go to get to its destination dragging down the performance.
Normally, during circuit manufacturing, each time you do anything with the copper surface, you have to start with a chemical or mechanical surface preparation, which eats away at the copper. This usually has to be done at least twice during the production of a typical inner layer, and the resulting surface finish may not be easy to control. The amount of copper reduction may also not be easy to guarantee. If you are dealing with very thin copper to begin with, this can become very relevant to the final cross-sectional area of the conductors that you produce.
If you were to use a resin-coated material and laser process, as I am suggesting, the properties of the copper would largely be fixed at the time they are encapsulated with resin by the material supplier. This means, for the first time, there could be a guarantee of the final performance. The material supplier would be able to “lock in” the desired surface finish and, therefore, the effect on the signal speed. The adhesion of the resin to the copper surface could also be predetermined, as the surface preparation of the copper would be completed before delivery to manufacturing. Typically, this is increasingly hard to control as well since you are forced to deal with smoother and smoother copper finishes to achieve higher and higher signal speeds.
The way I see it, smaller manufacturers would be able to achieve pretty much the same results as much larger companies as long as they are using a similar laser process. Prototypes would be much more reflective of the results that would be achieved during large batch manufacture simply because the inner layer process would largely be the same in both cases.
I may have missed a significant downside due to the rose-tinted spectacles that I am wearing to read through my own ideas. But I have shared my thoughts and put them “out there,” so I guess I will find out pretty soon.
Happy Christmas!
Marc Ladle is a director at Viking Test Ltd.
More Columns from Ladle on Manufacturing
Ladle on Manufacturing: LED UV Cure—Does It Really Work?Ladle on Manufacturing: UV Cure LED Energy Saver
Ladle on Manufacturing: Behind the Scenes at productronica 2019
Ladle on Manufacturing: Sunday Afternoon in Dongguan
The Travelling Engineer, Installment 2
Ladle on Manufacturing: VCP—The Future of Plating
Developments in Wet Processing: Beyond Spraying and Dipping
Ladle on Manufacturing: What’s New?