-
- News
- Books
Featured Books
- pcb007 Magazine
Latest Issues
Current IssueInventing the Future with SEL
Two years after launching its state-of-the-art PCB facility, SEL shares lessons in vision, execution, and innovation, plus insights from industry icons and technology leaders shaping the future of PCB fabrication.
Sales: From Pitch to PO
From the first cold call to finally receiving that first purchase order, the July PCB007 Magazine breaks down some critical parts of the sales stack. To up your sales game, read on!
The Hole Truth: Via Integrity in an HDI World
From the drilled hole to registration across multiple sequential lamination cycles, to the quality of your copper plating, via reliability in an HDI world is becoming an ever-greater challenge. This month we look at “The Hole Truth,” from creating the “perfect” via to how you can assure via quality and reliability, the first time, every time.
- Articles
- Columns
- Links
- Media kit
||| MENU - pcb007 Magazine
Estimated reading time: 7 minutes
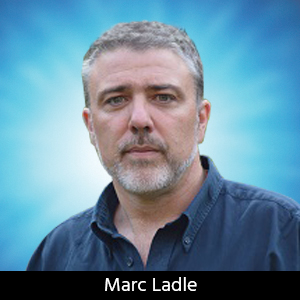
Ladle on Manufacturing: UV Cure LED Energy Saver
The solder mask (also known in some regions as solder resist) that protects the surface of the circuit boards we make has to stand up to a very wide range of process conditions. The same type of solder mask is typically expected to perform just as well in a superheated lead-free solder levelling process as it is in a chemically aggressive chemical nickel gold finish. Thankfully, the material has a wide process window, and with some care, it can usually handle everything that is thrown at it.
The normal application process involves first cleaning the circuit board surface. This could be abrasively cleaned, using an abrasive brush process, or if you are very old like me, you may remember scrubbing the copper surface with a pumice compound in a butler’s sink. Currently, the more common cleaning processes would involve chemical cleaning the surface with a micro-etch solution to create a good key to which the solder resist could adhere.
The methods of application for the solder resist are just as varied. The liquid types of solder mask could be applied by screen printing, spraying, or curtain coating, to name a few. Each of these processes has its own advantages and drawbacks. The resulting coverage may vary a lot in thickness and surface finish, depending on how it was applied. The corporate tastes of the companies that purchase circuit boards mean that there is also a wide range of colours that need to be applied, which adds a further element of variation.
I would like to concentrate on the most common type of solder mask material, which is the photoimageable type. It contains photoreactive elements in the ink that link together to form strong bonds when exposed to UV light. This allows a phototool or UV laser process to be used to selectively expose the mask. The photoselective process means that the whole surface of the production panel can be covered in the solder mask material.
Once the solder mask is applied to the production panel, it has to be surface-dried to enable it to be handled and allow contact with the phototool without creating cosmetic damage. Now, the ink can be selectively exposed to UV light to create the final pattern required by design. After the exposure process, the PCB is then run through a developing process that uses a chemical solution to dissolve the unexposed areas of solder mask where they are not wanted on the final design.
So far, so good. The vast majority of modern printed circuits are manufactured by this type of process. What happens next depends on the final metal finish of the circuit. For metal finishes, such as HASL or solder leveling, the level of UV exposure received during photoprocessing is enough. There is no further aggressive chemical processing usually involved, and the solder mask will be robust enough to achieve a long service life after receiving a final oven bake to fully dry it.
The reason I have taken this preamble through the processes of applying, exposing, and developing is to illustrate that there can be a lot of variation in the thickness, colour, and surface finish of the solder mask. When all of these components are considered together, it means that there can be a considerable range with regards to what is required from the final curing process to achieve the desired result.
For the more aggressive processes, more UV exposure may be needed. I have always called this process a UV bump, but it is just a blanket exposure to UV light at a process point following the development of the image. This is required because the photoimage exposure only creates enough crosslinks of the photoinitiators to stop them from being washed away by the developer solution. If you expose too hard at this stage, there is a tendency for the crosslinks to extend beyond the exposed edge, which can make the final feature size a little hard to control. There is also a risk of embrittling the mask, which could lead to failure during the heat process.
UV bump is not a new idea. Many years ago, I used a standard solder mask exposure machine to give a healthy second dose of UV light following the solder mask develop process. It was a bit of a pain bringing the panels back into the printing room after they had exited via the developer, but for the circuits I was making at the time, it was enough to ensure the mask would stand up to the electroless nickel or immersion tin chemistry.
An easy simplification of this process is to use a conveyorized dedicated UV cure machine that can be attached to the end of the developer or used following final thermal bake of the solder mask. To achieve enough exposure energy to run the process, 1 m per minute for a single vapour lamp is usually needed. If you want to go faster, you need more lamps.
Mercury vapour bulbs have a few negative issues. They degrade over time, which means the process has to be regularly adjusted to ensure that the exposure energy remains the same. They also are power-hungry, as they produce a lot of heat. Further, they require a long warm-up period and need to be shut down carefully to ensure the bulbs are not damaged prematurely.
UV LED is a useful step in the right direction (Figure 1). Modern LEDs are capable of outputting high power, and they are certainly a lot more efficient than the vapour lamp process. Each LED outputs a distinct light wavelength. Different LED wavelengths can be mixed to give an array, which is useful for the UV cure process. The length of the array can be manufactured for pretty much any width, which removes the need for any type of reflector or lens to cover the width of a typical process conveyor.
LED may appear to be the ideal solution, but there can be a problem with their use due to the way that solder mask materials work. The wide spectrum output of the traditional vapour lamp includes some Infrared wavelengths, which are also often required to complete the cure process by heating the solder mask. The LED with its distinct single wavelength output cannot match this aspect of the vapour lamp.
The good news is that the two processes can be combined pretty easily. A hybrid machine with a single vapour lamp and one or two LED arrays will still save more than 50% of the power consumed by a conventional machine. Maintenance is also reduced, and there is very little degradation of the LED output over time, giving a more consistent process.
Like so many parts of the printed circuit manufacturing process, the solder mask materials and basic production methods are stolen from larger and better-funded industries. In time, solder masks may be “tuned up” to better suit the defined wavelength output of LED machines.
A further advantage is the more adjustable nature of the LED system where certain wavelengths can be increased or reduced. Typically, LEDs output at 365-, 385-, 395-, 405-, or 415-nanometer wavelengths. With a careful design of the LED array, it is possible to control the intensity of each wavelength (Figure 2). This may become useful when attempting to cure different colours, particularly white solder mask, which is very reflective. The thickness of the solder mask can also cause some problems due to a lack of UV light penetration to the full depth of the material.
A cure machine using only UV LEDs can work with some solder mask materials, but it is important to make a realistic trial before machine purchase to ensure that it will meet all of your process requirements. If it works for you, the advantages are a nearly instant start-up and shut-down time and energy savings of more than 80% compared to a vapour lamp process (Figure 3). The maintenance of an LED-driven machine is also greatly reduced, as the diodes typically last for many production years and do not require changing every few months. LED process is also completely suitable for the reduction of ionic contamination, which is an increasing requirement for certain types of circuit manufacturing.
If you can make it work for you, changing to an LED-driven process is an easy decision. The power savings alone will ensure a quick payback on investment, and a well-designed system will add a new and improved level of control to the process.
This column originally appeared in the November 2019 issue of PCB007 Magazine.
More Columns from Ladle on Manufacturing
Ladle on Manufacturing: LED UV Cure—Does It Really Work?Ladle on Manufacturing: Sharing an Idea for Christmas
Ladle on Manufacturing: Behind the Scenes at productronica 2019
Ladle on Manufacturing: Sunday Afternoon in Dongguan
The Travelling Engineer, Installment 2
Ladle on Manufacturing: VCP—The Future of Plating
Developments in Wet Processing: Beyond Spraying and Dipping
Ladle on Manufacturing: What’s New?