-
- News
- Books
Featured Books
- pcb007 Magazine
Latest Issues
Current IssueInventing the Future with SEL
Two years after launching its state-of-the-art PCB facility, SEL shares lessons in vision, execution, and innovation, plus insights from industry icons and technology leaders shaping the future of PCB fabrication.
Sales: From Pitch to PO
From the first cold call to finally receiving that first purchase order, the July PCB007 Magazine breaks down some critical parts of the sales stack. To up your sales game, read on!
The Hole Truth: Via Integrity in an HDI World
From the drilled hole to registration across multiple sequential lamination cycles, to the quality of your copper plating, via reliability in an HDI world is becoming an ever-greater challenge. This month we look at “The Hole Truth,” from creating the “perfect” via to how you can assure via quality and reliability, the first time, every time.
- Articles
- Columns
- Links
- Media kit
||| MENU - pcb007 Magazine
Estimated reading time: 7 minutes
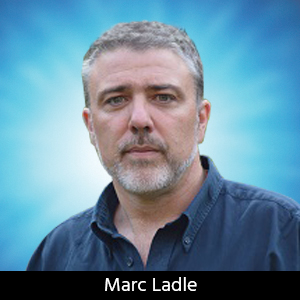
Ladle on Manufacturing: Behind the Scenes at productronica 2019
Once every two years, I am involved with setting up our company stand and exhibiting some of the machines we work with at productronica—the electronics industry trade show in Munich, Germany. It is still the largest show of this type in Europe, and you would have to go quite a lot further to see anything bigger with a greater number of exhibitors.
If you have been in the industry for a long time, you may remember the days of three full halls packed with PCB equipment suppliers all doing good business. Now, it is down to a single hall of equipment and services for bare board fabricators, and some of that space is given up to the lecture and meeting area. There is still a good justification for visiting, even if the show is not as large as it was years ago. The opportunity to get up close and familiar with the newest equipment and products available and the companies who manufacture and service it is an attraction for many printed circuit people.
If you wanted to see more variety, you would have to travel to one of the shows in Asia where the scale of the industry is very large compared to the manufacturing we have left in Europe. In my opinion, productronica is still the best place if you want to connect with people who have a proven track record working to the standards and specialisms required in Europe. To put the size of the show in perspective, the HKPCA show in Shenzhen this December will have over four halls of exhibitors and be pretty crowded, but in my opinion, it is less relevant to most people outside of Asia.
The show planning for our company usually starts around April. We need to consider if the equipment enquiries we are working on may be suitable for display at the show and if the customer may be amenable to allowing us to use their machine for this purpose. Often, there is a deal to be done here. Usually, we can offer some small financial incentives to help compensate for any inconvenience and delay caused. Once the basic equipment plan has been put together, the stand build and services have to be arranged as well as the logistics of moving equipment around the world to arrive in Munich at just the right time.
This year, the British nearly had Brexit to contend with, and I have to admit that I breathed quite a large sigh of relief when a further extension was made to the U.K.’s European membership. The watershed date of October 31 would have been just before our machines arrived in the U.K. from Asia; the threatened queues at the English Channel crossings and increased paperwork that was being talked about could have had quite a negative effect on our plans. I had bad dreams about arriving at the show to set up the stand and having nothing to display!
The run-up to the show this year has been very busy for me. Viking has been going through a very busy period of customer machine installations, which meant there was very little time available for planning and preparation. I am glad to have been through the process quite a few times before, so I had a good idea about how best to get the job done.
On November 4, a 40-foot shipping container arrived at our headquarters full of most of the equipment we intended to take to the show. Most of the machine modules had to be un-palleted and partly unwrapped to make sure we were not overrun with packing materials when we unloaded in Germany. Like most things at productronica, there is a substantial cost involved for the storage of pallets and materials, so it is a good idea to keep this to a minimum.
Then, a 40-foot curtain-sided trailer arrived at our offices on November 7 to pick up items for the show. Steve and Ben (two of the younger members of the Viking team—the latter being my youngest son) carefully loaded and secured the machines and other show materials ready for the Road trip from the U.K. to Munich (Figure 1). The trip takes most of two days for the heavy vehicle planned to arrive at the showground on Friday evening.
Figure 1: Loading for Germany.
Ben and I left home at 5 a.m. on Saturday morning in our largest company van and headed for the Channel Tunnel. Ben had prepared in the normal way that 22-year-olds do—by drinking heavily with his friends the previous night, so he subsequently slept all the way to Folkstone. He managed to revive during the train journey and took over the driving to Munich. We arrived at our hotel at 8 p.m. in time to have a quick bite to eat and get our heads down.
November 10 was the main set-up day. We had to build a modular film stripping machine, which we would usually assemble in three days at a customer site. It is fair to say that not every part of the machine is complete when it is built for the show, but it is still a tall order to get the machine into a respectable state for demonstrations with the conveyor running and panels passing through it (Figure 2).
Figure 2: Hoping the machines arrive on time.
We were also joined by Jermin and Millar from Viking in China, who came directly from the airport after a 12-hour flight and got straight down to work assembling, powering up, and checking a UV LED curing machine. November 11 gave us time to check things over and make sure we would be ready for duty when the doors opened the following morning (Figure 3). Then, it was time for the main event.
Figure 3: Nearly ready.
I honestly enjoy the show. It is a mixture of meeting up with old friends and acquaintances (some of whom I regard as industry legends), as well as a few business rivals, and, of course, an opportunity to connect with existing and potential future customers. The show provides a chance to gain a snapshot of what are currently hot topics in the industry based on what we are being asked for.
This year, there was definitely a strong interest in vertical continuous plating both for conventional copper plating purposes but also how we may be able to apply the same technology to enable other processes to benefit from the special transport and distribution opportunities enabled by this special machine format. Vacuum etch also continues to be a strong topic, offering considerable benefits for top side etch performance. And more customers are considering pushing the boundaries of line width capability and exploring etching machine developments, which can deliver the special results they are looking for.
A special mention and vote of thanks has to go out to Storming Norman Furgusson from MPK Kemmer, who managed to keep my son fed and entertained for pretty much the whole show. Norman is full of useful information regarding all aspects of making holes in and cutting electronic base materials, and I have to admit that I still use many of the snippets of wisdom he imparted to me more than 20 years ago while I was struggling to achieve the perfect deep hole drilling cycle through more than 12 mm of FR-4.
The award for special fright for this year’s show was definitely when I was given 30 seconds of warning for my video interview—an opportunity to explain the finer details of UV LED technology regarding the solder mask bump process. If I look a little like a rabbit in the headlights on the published video, I am not exactly surprised, as it felt a little like being put in front of the headmaster to explain how 12 pupils were seen getting out of my five-seat car at lunchtime.
Breaking down the stand is pretty much the reverse of the set-up process, but it is completed after standing on your feet for what feels like a whole week without many breaks (Figure 4). I have to admit that we started to take a few things apart as the crowd thinned out around 3 p.m. on Friday. Even with that running start, we were still on site until 10 p.m., trying to have everything ready for loading the vehicle at 9 a.m. the following morning.
Figure 4: Negotiating the breakdown logjam.
Any visitors to the show would not recognise the place on Saturday morning after the show when it is impossible to walk down some of the corridors between stands due to the packing boxes and debris. Hats off to the forklift drivers on the show floor who had to get past the mayhem of the breakdown process by lifting expensive machines high above the packing boxes and people to get them safely outside of the halls for loading (Figure 5). They definitely have some precision driving skills!
Figure 5: Coming through at a high level.
I almost breathed a sigh of relief as the full trailer pulled away. and the show was over for another two years, but there was not much opportunity to draw breath. Ben and I were back on the road to head to Berlin to begin the installation of an immersion tin machine.
Marc Ladle is a director at Viking Test Ltd.
More Columns from Ladle on Manufacturing
Ladle on Manufacturing: LED UV Cure—Does It Really Work?Ladle on Manufacturing: UV Cure LED Energy Saver
Ladle on Manufacturing: Sharing an Idea for Christmas
Ladle on Manufacturing: Sunday Afternoon in Dongguan
The Travelling Engineer, Installment 2
Ladle on Manufacturing: VCP—The Future of Plating
Developments in Wet Processing: Beyond Spraying and Dipping
Ladle on Manufacturing: What’s New?