-
- News
- Books
Featured Books
- pcb007 Magazine
Latest Issues
Current IssueInventing the Future with SEL
Two years after launching its state-of-the-art PCB facility, SEL shares lessons in vision, execution, and innovation, plus insights from industry icons and technology leaders shaping the future of PCB fabrication.
Sales: From Pitch to PO
From the first cold call to finally receiving that first purchase order, the July PCB007 Magazine breaks down some critical parts of the sales stack. To up your sales game, read on!
The Hole Truth: Via Integrity in an HDI World
From the drilled hole to registration across multiple sequential lamination cycles, to the quality of your copper plating, via reliability in an HDI world is becoming an ever-greater challenge. This month we look at “The Hole Truth,” from creating the “perfect” via to how you can assure via quality and reliability, the first time, every time.
- Articles
- Columns
- Links
- Media kit
||| MENU - pcb007 Magazine
Estimated reading time: 2 minutes
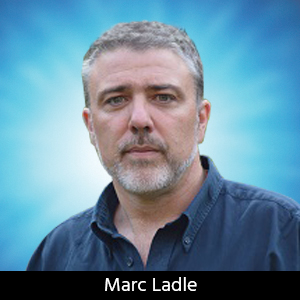
Ladle on Manufacturing: VCP—The Future of Plating
Electroplating copper has been a standard part of the PCB manufacturing process for more than 50 years. The basic technology has not changed very much in that time. Normal arrangements involve a series of chemical and rinse tanks into which panels are dipped first to clean the copper surface and then to electroplate copper onto the surface and through the drilled holes and vias.
Some smaller manufacturers still use a manual process where an operator moves the panel(s) being plated from tank to tank to complete the process. Larger manufacturers use machines that may have a very similar arrangement of tanks but on a larger scale, and an automatically controlled transporter moves the panels.
The normal process options for the plating operation are either panel or pattern plating. Either way, the panels are prepared by drilling all of the holes required and then making a thin conductive deposit such as electroless copper or carbon/graphite. This will be used as the base for electroplating through the holes. If you panel plate, the whole of the surface is electroplated as well as the drilled holes. If you pattern plate, then a plating resist is used to make an image on the surface, and the copper is electroplated selectively.
Over the years, developments have been made from time to time that have helped to refine the process. For instance, floating shields within the copper tanks have helped to deal with panels of different lengths. Pulse rectification has enabled high aspect ratio panels to be produced with an even deposit of copper through the holes. However, if you had run one of the original processes back in the day, you would still recognise a more modern version of the process.
Even with the best available traditional plating line, there are still some shortcomings that are difficult to overcome. It is not efficient to plate panels one at a time—you would need a lot of plating tanks, and throughput would be pretty low. Most machines are based on plating several panels at a time either using a jig to hold them in position or hanging them from top clamps in a long row. In both methods, each panel has a slightly different plating effect, and therefore, a different copper thickness.
This variation in copper thickness means that circuit performance is compromised. The target should always be for each circuit produced to be exactly the same.
The vertical continuous plating (VCP) process offers a good solution to this problem of variation. Instead of dipping panels in a succession of tanks, the VCP process moves the panel in a linear motion through the critical process stages. In the case of the copper tank, this means that the panel is moved through a very long plating tank from one end to the other, and every panel in the batch has exactly the same process path; thus, the variation from panel to panel is absolutely minimal.
This article originally appeared in the January 2019 issue of PCB007 Magazine, click here.
More Columns from Ladle on Manufacturing
Ladle on Manufacturing: LED UV Cure—Does It Really Work?Ladle on Manufacturing: UV Cure LED Energy Saver
Ladle on Manufacturing: Sharing an Idea for Christmas
Ladle on Manufacturing: Behind the Scenes at productronica 2019
Ladle on Manufacturing: Sunday Afternoon in Dongguan
The Travelling Engineer, Installment 2
Developments in Wet Processing: Beyond Spraying and Dipping
Ladle on Manufacturing: What’s New?