-
- News
- Books
Featured Books
- pcb007 Magazine
Latest Issues
Current IssueInventing the Future with SEL
Two years after launching its state-of-the-art PCB facility, SEL shares lessons in vision, execution, and innovation, plus insights from industry icons and technology leaders shaping the future of PCB fabrication.
Sales: From Pitch to PO
From the first cold call to finally receiving that first purchase order, the July PCB007 Magazine breaks down some critical parts of the sales stack. To up your sales game, read on!
The Hole Truth: Via Integrity in an HDI World
From the drilled hole to registration across multiple sequential lamination cycles, to the quality of your copper plating, via reliability in an HDI world is becoming an ever-greater challenge. This month we look at “The Hole Truth,” from creating the “perfect” via to how you can assure via quality and reliability, the first time, every time.
- Articles
- Columns
- Links
- Media kit
||| MENU - pcb007 Magazine
Estimated reading time: 5 minutes
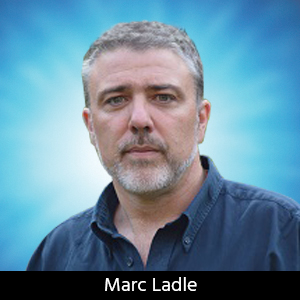
Ladle on Manufacturing: Back to Basics
Many companies in the printed circuit industry are based in a single factory. When everything is going well, this can really help to get the best out of people and machinery. The main drawback is that seeing the same issues day after day, it can be easy to accept your manufacturing problems as being normal.
I installed an AOI machine for a customer in a small factory which employs around 10 people in the manufacturing area. I would describe everyone who works there as multi-skilled. Processes would run only as they were required and the factory was busy and reasonably efficient for the type of work that was being completed. Most of the equipment had been in place for quite a few years, but generally everything looked well maintained.
Installing inspection or test equipment is a great opportunity for an outsider to get an idea of the range of typical faults that are occurring in the manufacturing processes. In this case we were inspecting panels after outer layer etch. Training was going well and we were picking out the types of faults that the customer was interested in catching.
We saw quite a few examples that I thought looked like the dry film had lifted either before or during the electroplating process, resulting in excess copper between tracks. Because the factory was small and production was not a constant flow, I suggested we look back through the preceding processes when we ran out of panels to inspect.
The idea was sound enough. I thought it would be a good opportunity to see if we could find an underlying cause for the poor dry film adhesion which would account for the faults we detected on the AOI. As I was intending to be onsite for a couple of days, I thought we may be able to see an improvement before I left.
We started at drilling and worked our way through the production process as far as the carbon through-hole line. We could see some cleanliness issues with residues on the rollers, which were far from ideal. We discussed the machine cleaning regime and the customer admitted that things may slowly have slipped with the care of this process.
There were still no further panels to AOI, so we carried on with what had turned into a very low-key process audit. By this time, most of the production had wound down for the day and the factory was rather quiet. We had become a group of four—myself and three of the more senior production staff in the factory. We were getting on quite well and it was a good opportunity to look at each stage of the production process.
We had reached the pattern plating line and I was looking down the tanks from the loading end. It was a small transporter line using stick jigs, and the last few panels for the day were on their way through the final stages. Small batch production is always difficult to load to this type of jig arrangement. The last few panels often must be run in a compromised arrangement on the jigs to fill the space. But looking down the line I could see that the anodes were in different positions in each of the plating tanks. I asked the question: Have you moved the anodes to help get a better distribution when you have a small area loaded to the flight bar? I could tell from the puzzled expression that the arrangement was not due to any special technical intent.
After a few questions about the panel sizes and the way that the panels were loaded to the jigs, I realised that the edges of the panels were probably always over-plated, as some of the anodes were well outside the plating window they were using.
Now, here was the surprise for me. My suggestion to move the anodes was met with quite a degree of skepticism. There was a detectable change in atmosphere and I could tell that all was not well in the world of informal audits! I like to think that I have a gentle “lineside manner” and I tried again suggesting that at least the arrangement in each of the plating cells should match each other to ensure a consistent result.
After an amount of discussion, a few pencil drawings and a cup of coffee, I left the guys from the factory to their thoughts. I retreated to the local bed & breakfast to consider what I could have done better. Production issues can be delicate subjects. In this case I have an idea that the plating operator may not have been the easiest guy to deal with and at least some of the problem would be the drawing of straws to see who got the job of telling him that his setup was not perfect.
Twelve hours can be a long time in circuits and the following morning, when I arrived at the factory, I was met by a delegation rushing out of the factory door. Any worries were only momentary as I could tell by the smiles that things were OK this morning.
The guys had stayed for quite a while after I left and tried making the changes we had discussed together. The results were a significant improvement in copper distribution. We saw some tenable benefit from the time we had taken to look at the processes. The improvement in this process would have many benefits for the quality of the parts being manufactured so it made our efforts very worthwhile. There was no huge expense involved—my time was free for the agreed duration of the AOI installation and the guys at the factory were salaried staff. The real benefit was a renewed enthusiasm to question if best practice was being followed throughout the factory.
For me, the main advantage was the added kudos with the customer. It certainly adds some gravity to your advice if you can show some practical benefit. If I am 100% truthful, I really enjoy the problem-solving aspect of process engineering and when a customer allows me to be involved in this way, it is therapeutic time for me. Happy days!
Marc Ladle is director at Viking Test Ltd. To contact Ladle, or to read past columns, click here.
Editor's Note: This article originally appeared in the September 2017 issue of The PCB Magazine, click here.
More Columns from Ladle on Manufacturing
Ladle on Manufacturing: LED UV Cure—Does It Really Work?Ladle on Manufacturing: UV Cure LED Energy Saver
Ladle on Manufacturing: Sharing an Idea for Christmas
Ladle on Manufacturing: Behind the Scenes at productronica 2019
Ladle on Manufacturing: Sunday Afternoon in Dongguan
The Travelling Engineer, Installment 2
Ladle on Manufacturing: VCP—The Future of Plating
Developments in Wet Processing: Beyond Spraying and Dipping