-
- News
- Books
Featured Books
- design007 Magazine
Latest Issues
Current IssueAll About That Route
Most designers favor manual routing, but today's interactive autorouters may be changing designers' minds by allowing users more direct control. In this issue, our expert contributors discuss a variety of manual and autorouting strategies.
Creating the Ideal Data Package
Why is it so difficult to create the ideal data package? Many of these simple errors can be alleviated by paying attention to detail—and knowing what issues to look out for. So, this month, our experts weigh in on the best practices for creating the ideal design data package for your design.
Designing Through the Noise
Our experts discuss the constantly evolving world of RF design, including the many tradeoffs, material considerations, and design tips and techniques that designers and design engineers need to know to succeed in this high-frequency realm.
- Articles
- Columns
- Links
- Media kit
||| MENU - design007 Magazine
AltiumLive Summit—Munich, Germany, Part 2
November 13, 2017 | Pete Starkey, I-Connect007Estimated reading time: 8 minutes
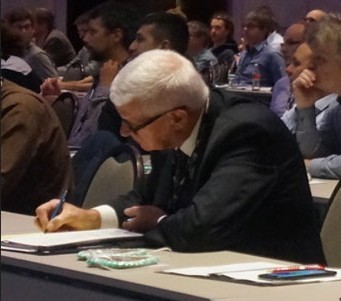
Editor's Note: To read the part 1 of this article, click here.
The second day commenced with a new product launch. “Working together is hard” it read on the screen. Statistics indicated that 33% of new products were late getting to market, of which 28% were late due to insufficient collaboration, and up to 50% of potential revenue could be lost through being late to market. Then the screen read “NEXUS makes it easy!”
Dan Fernsebner introduced Altium’s system-level design-collaboration tool, built to enable schematic, layout, MCAD, and PCB multi-board interactions between team members using a collaboration panel, and to record every action and decision as part of the design history. NEXUS was cloud-enabled and gave members of the design team access to a central database through which they could communicate directly and each view changes and accept or reject them. Whatever changes were made, the design files were immediately updated.
Fernsebner demonstrated the capability of the system with a live exercise. In his example, an end-of-life connector required to be replaced and re-positioned. Four engineers were involved: schematic design engineer, PCB designer, mechanical engineer and system design engineer. Each had the facility to interact with the cloud and push and pull the details relevant to his area of responsibility, whilst observing the consequences on every other engineer’s area. Once the changes had been made, agreed and accepted, everything was automatically updated and recorded and the task had been completed with no ambiguity and no waste of time.
The day’s first industry keynote, “PCBs for Computing Density, From Big Bang to the Automobile,” was delivered by research scientist Andreas Doering from the IBM Research Laboratory, technical design lead for the DOME microserver project, and now piloting the development of the world’s largest radio telescope for exploring the origins of the universe. He explained that DOME was a Dutch government-funded project between IBM and ASTRON in form of a public-private-partnership focusing on the Square Kilometre Array,
Even though the Big Bang was estimated to have taken place 13.8 billion years ago, there was believed to still be some evidence of its occurrence and its consequences, if there was big enough detector and a powerful enough computer to process all the data it collected, which would be more in one day than the whole internet produces in a year—although most of it would be noise. Rather than employing one enormous dish, the Square Kilometre Array would draw on more than one hundred thousand dishes and antennae spread across Africa and Australia to create a collecting area of one square kilometre. Construction was due to begin in 2018.
Based on Doering’s projections on the amount of computing capacity required to process a minimum of 14 exabytes of data per day (where one exabyte equals 1018 bytes), a conventional computer would need several gigawatts of power to drive it. So the demand was for higher computing density, higher performance per watt, and reduced complexity of systems. Enabled by the emergence of powerful embedded-processor cores, a new class of custom-designed “microserver” was in development, with non-enclosed modules comprising system-on-chip, plus DRAM, plus flash, plus power, mounted in multiples on a backplane.
The project required 21 different PCB designs, most of which had been produced on Altium Designer, and he listed the attributes of each. The switch mothercard was a 3.6 mm, 28-layer with back-drilling, six inner impedance-controlled signal layers, with shielding ground layers in-between, and four high-current power supply lanes. At its current state of development, the system consisted of a backplane for 32 compute nodes, of which eight were populated, one switch node, one management node and two storage nodes, with water-cooling. The next stage would be a unit containing two backplanes and a total of 64 compute nodes, representing 1536 cores, 1536 GB of DRAM and 64 SSDs. Besides the primary application in the Square Kilometre Array, Doering saw many potential market opportunities for microservers in scientific computing, internet-of-things, robots and autonomous vehicles.
Back to parallel technical breakout sessions: the choice was between Willem Gruter’s “Verifying your FPGA is correctly connected on a PCB,” Martin Schuster’s “Boost your Altium Design Efficiency with Templates and Shortcuts,” or Jürgen Wolf’s “Embedding Technology—Design and Layout of Printed Circuit Boards with Embedded Components in Altium.” The first two appeared to me to be experts-only advanced tutorials for professional designers. I could identify directly with embedding technology, so I chose Wolf’s session and made sure to grab a seat early because it turned out to be a standing-room-only event.
It was a good choice! Würth Elektronik product manager Jürgen Wolf gave an enlightening insight into three different embedding technologies, ET solder, ET microvia and ET flip-chip and their typical applications, with detailed manufacturing process sequences and design guidelines. He reviewed the benefits of embedding technology in terms of miniaturisation, functionality and reliability, and listed the indicators for choosing a particular technology: ET solder was suitable for active components not available as bare die, and a range of solid SMD components. ET microvia was a highly reliable assembly and packaging technology which could be used for a combination of active and passive components, provided they had copper or nickel-palladium pad metallisation. ET flip-chip was used for fine-pitch components which would otherwise have been wire-bonded. It was not appropriate for passive components.
The process flow for ET solder was to structure the innerlayer core with the SMD component footprint, then to reflow lead-free solder as in typical SMD assembly, then to laminate as a multilayer PCB and finish according to customer requirements.
The process flow ET microvia offered two options: either start with copper foil as substrate and assemble the components face-down with non-conductive adhesive, then laminate as a multilayer and make contact to the components by laser drilling, metallising and copper plating, followed by structuring of the outer layers. Alternatively, assembling the components face-up on the innerlayer core with isotropic conductive adhesive, then laser drilling, metallising, copper plating and outer layer structuring.
The process flow for ET flip-chip began with an innerlayer core structured with the flip-chip footprint, followed by flip-chip assembly using anisotropic conductive adhesive, then multilayer lamination and finishing according to customer requirements.
Wolf gave a comprehensive series of suggestions for project planning, design rules, layout, thickness tolerances and bills of materials for the embedded components, and showed with a live demonstration how Altium Designer could be used for defining the stack-up, the component layer and the component placement and orientation, together with calculation of dimensions and clearances for cavities and workarounds for designing innerlayer solder mask and solder paste images. There were particular rules about grouping of components and safe distances from edges. An in-depth knowledge of prepreg resin flow characteristics was needed to ensure void-free encapsulation.
Page 1 of 2
Suggested Items
Driving Innovation: Direct Imaging vs. Conventional Exposure
07/01/2025 | Simon Khesin -- Column: Driving InnovationMy first camera used Kodak film. I even experimented with developing photos in the bathroom, though I usually dropped the film off at a Kodak center and received the prints two weeks later, only to discover that some images were out of focus or poorly framed. Today, every smartphone contains a high-quality camera capable of producing stunning images instantly.
Hands-On Demos Now Available for Apollo Seiko’s EF and AF Selective Soldering Lines
06/30/2025 | Apollo SeikoApollo Seiko, a leading innovator in soldering technology, is excited to spotlight its expanded lineup of EF and AF Series Selective Soldering Systems, now available for live demonstrations in its newly dedicated demo room.
Indium Corporation Expert to Present on Automotive and Industrial Solder Bonding Solutions at Global Electronics Association Workshop
06/26/2025 | IndiumIndium Corporation Principal Engineer, Advanced Materials, Andy Mackie, Ph.D., MSc, will deliver a technical presentation on innovative solder bonding solutions for automotive and industrial applications at the Global Electronics A
Fresh PCB Concepts: Assembly Challenges with Micro Components and Standard Solder Mask Practices
06/26/2025 | Team NCAB -- Column: Fresh PCB ConceptsMicro components have redefined what is possible in PCB design. With package sizes like 01005 and 0201 becoming more common in high-density layouts, designers are now expected to pack more performance into smaller spaces than ever before. While these advancements support miniaturization and functionality, they introduce new assembly challenges, particularly with traditional solder mask and legend application processes.
Knocking Down the Bone Pile: Tin Whisker Mitigation in Aerospace Applications, Part 3
06/25/2025 | Nash Bell -- Column: Knocking Down the Bone PileTin whiskers are slender, hair-like metallic growths that can develop on the surface of tin-plated electronic components. Typically measuring a few micrometers in diameter and growing several millimeters in length, they form through an electrochemical process influenced by environmental factors such as temperature variations, mechanical or compressive stress, and the aging of solder alloys.