-
- News
- Books
Featured Books
- smt007 Magazine
Latest Issues
Current IssueWhat's Your Sweet Spot?
Are you in a niche that’s growing or shrinking? Is it time to reassess and refocus? We spotlight companies thriving by redefining or reinforcing their niche. What are their insights?
Moving Forward With Confidence
In this issue, we focus on sales and quoting, workforce training, new IPC leadership in the U.S. and Canada, the effects of tariffs, CFX standards, and much more—all designed to provide perspective as you move through the cloud bank of today's shifting economic market.
Intelligent Test and Inspection
Are you ready to explore the cutting-edge advancements shaping the electronics manufacturing industry? The May 2025 issue of SMT007 Magazine is packed with insights, innovations, and expert perspectives that you won’t want to miss.
- Articles
- Columns
- Links
- Media kit
||| MENU - smt007 Magazine
Estimated reading time: 13 minutes
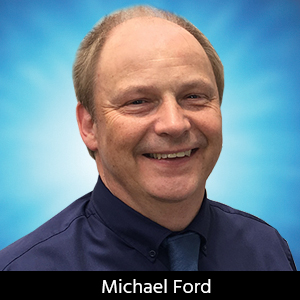
Resolving the Productivity Paradox
You would have thought that by now, with a few years of Industry 4.0 under our belt, that our German friends would be reveling in the success of Industry 4.0. However, recent reports show that overall factory productivity has continued to decline in German companies, even though investments have been made in new automation technology. This is being called the “productivity paradox.” To a growing number of people and companies, this does not come as a surprise because investment in automation alone is still just an extension of Industry 3.0. There has been a failure to understand and execute what Industry 4.0 really is, which represents fundamental changes to factory operation before any of the clever automation and artificial intelligence (AI) tools can begin to work effectively.
In the electronics manufacturing world, we experience the worst-case scenario of effects that change has on production operations. We have accepted deep down that higher product mix leads to reduced productivity. It is easy to simply write this off as a cost of doing business where there is the need to provide flexibility without an increased stock holding of finished goods.
However, this is not the complete story. For example, SMT machine vendors have long been making their equipment suitable for flexible production with hardware- and software-based solutions where feeders can be placed anywhere on the machines. Further, SMT machine vendors have been developing techniques to provide rapid changeovers with common feeder setups for groups of similar products, and even changeovers between disparate products with the simple swap out of removable feeder trolleys.
Even without these technology aids, the manual changeover time on a fully-loaded SMT placement machine time varies across companies from around five minutes to six hours, depending on the approach used. Take a look at the pit stop in a Formula One race to learn how to achieve the five-minute SMT turnaround. Huge losses to achieve flexibility are not a done deal. There are both technology and management options out there.
The productivity paradox continues to thrive. At an event in Scandinavia recently, I showed a slide of how high-volume productivity expectations of 80% or more are now replaced with 20–40% in today’s higher mix environment. I was approached afterwards by someone saying that I had the numbers wrong, as they dreamed of being able to achieve 20%. The real number in many companies is far less than that today, which appears to support the German report. The mix of products in production continues to increase. Additionally, with a more volatile demand requirement, customers of manufacturing want the ability to change delivery quantities and times immediately whilst also not accepting the cost of holding additional buffer stock. Factories are paying the price of the effect of fluctuating customer demand directly into their automated production lines.
To find the answer to this apparent conundrum, we start by looking at what is reported in terms of metrics within factories. Targets are the critical drivers for manufacturing performance. Around the factory, we see reports and charts explaining targets and achievement related to things such as on-time delivery, production rate, materials scrap, quality issues, etc. Pretty much everything in the factory is measured to some extent based on those statistics. Management wants to see that each process is under control and improvements are being steadily made. To focus on the productivity perspective, seeing what is posted in factories appears rather optimistic compared to what would be expected when thinking about the productivity paradox. Any schoolboy mathematician will quickly deduce that the metrics within the factory are based on a different dataset than the German report, which is where the problem lies.
The measurement of internal performance can be justifiably made in many different ways. Statistics can be made to show whatever specific perspective is needed. This style of reporting started when many enjoyed high-volume production. Dedicated production lines were making products as fast as possible. The emphasis was on getting more and more throughput from each square meter of line space. Performance was simply based on how many placements per hour could be achieved. Extreme effort went into the optimization of machine programs. However, to measure the machine performance accurately meant that machine downtime outside of machine responsibility should be ignored. If the line could potentially make 2,000 products per day, this was the rate against which performance was measured. It was extremely unlikely that the customer needed exactly 2,000 products per day.
Even in those days, demand fluctuated. When the finished goods warehouse started to fill to a bursting point, the line was taken down, unscheduled, and perhaps used this opportunity to perform maintenance. These times were excluded from the productivity calculation because it was an external, uncontrolled variable from the point of view of the machine engineers. This was the start of bad habits that developed and broadened over the course of time. More and more exclusions were made to reflect specific narrow scopes of responsibility as product mix increased. Productivity and capacity calculations became far more complex as techniques to manage higher mix came into play.
For example, the common setup of feeders on SMT placement machines was seen as a way to avoid the physical changing of locations of materials on the machines between different products. If two products running consecutively required the same materials, then why not keep the same materials in place on the machine and eliminate the time to change them? Unfortunately, this created a new restriction for machine program optimization. The path travelled by the machine head to pick the most commonly used materials to the points of placements could no longer be optimized through the choice of where the materials should be set up on the machine. As a result, the program execution time was longer and less efficient.
Page 1 of 3
More Columns from Smart Factory Insights
Smart Factory Insights: Making Rework a Smart Business OpportunitySmart Factory Insights: The Sustainability Gold Rush
Smart Factory Insights: Today’s Manufacturing Jobs Require a New Skill Set
Smart Factory Insights: Compose Yourself, Mr. Ford
Smart Factory Insights: The Smart Business Case for Local PCB Manufacturing
Smart Factory Insights: Manufacturing Digital Twin—Spanners in the Works
Smart Factory Insights: Machines, People, and AI
Smart Factory Insights: Is Sustainability in Manufacturing a Benefit or Burden?