-
-
News
News Highlights
- Books
Featured Books
- smt007 Magazine
Latest Issues
Current IssueSpotlight on India
We invite you on a virtual tour of India’s thriving ecosystem, guided by the Global Electronics Association’s India office staff, who share their insights into the region’s growth and opportunities.
Supply Chain Strategies
A successful brand is built on strong customer relationships—anchored by a well-orchestrated supply chain at its core. This month, we look at how managing your supply chain directly influences customer perception.
What's Your Sweet Spot?
Are you in a niche that’s growing or shrinking? Is it time to reassess and refocus? We spotlight companies thriving by redefining or reinforcing their niche. What are their insights?
- Articles
- Columns
- Links
- Media kit
||| MENU - smt007 Magazine
Estimated reading time: 5 minutes
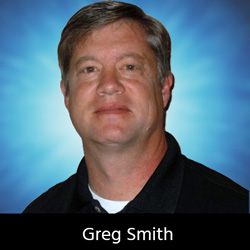
Overcoming the Challenges of Miniaturization with New Stencil Technologies–Solder Paste Release, Pt. 2
In today’s assembly environment, reducing first-pass defects is many times focused on smaller components and achieving repeatable solder paste deposits during the print process. If the stencil technology used is not matched to the component technology, insufficient solder paste and/or excess solder paste can result in increased first-pass defects.
As discussed previously in Part 1 of this column series, 0201 imperial components have become mainstream, 01005 imperial (0402 metric) components are being used more often, and 03015 metric components are on the near distant horizon. The challenge to release solder paste from these very small openings in the stencil is real. To overcome this challenge, I discussed how critical both the design software and the stencil foil is to this process. In this column, I will discuss the importance of stencil coatings to meet this challenge.
Nano Coatings
Figure 1: Nano coatings can repel water- and/or oil-based chemistry or flux.
Nano coatings offer several benefits. They are hydrophobic and repel water-based chemistry or flux, and some are also oleophobic and repel oil-based chemistry or flux (Figure 1). When applied to the bottom or board side of the stencil, these coatings will prevent solder paste squeeze-out during the print process between the stencil and PCB from sticking to the bottom of the stencil when the stencil separates from the board. As a result, the next print will be as good as the initial print, and bridging is reduced because there is no paste on the bottom of the stencil to transfer to the PCB during the next print. In addition, underside cleaning frequency can be reduced as there is much less solder paste to remove from the stencil. In some cases, I’ve seen customers move from cleaning after every print to cleaning after every 20 prints.
It is also very important to understand there are two primary types of nano coatings available to those using SMT stencils today in North America. The first and original coating available for SMT stencils is the self-assembled monolayer (SAM) coating (Figure 2). One example of this coating is MicroShield. As the term “monolayer” suggests, this type of coating is one layer thick and bonds directly to the surface of the stencil foil. The coating was introduced many years ago and is manually applied to the board side of the stencil. The thickness of the SAM coating is in the range of two to four nanometers, and because the coating is so thin, there is no color making it difficult to tell visually if the coating is present. The best way to determine if the coating is present on the stencil is to use a Dyne Pen to test the surface energy present.
Figure 2: SAM coating.
As shown in Figure 3, these pens are filled with a liquid that will show if the surface is hydrophobic or not when applied to a surface. In the right image, the liquid from the pen is not sticking to the foil and is being repelled into small droplets. In the same way, the coated surface will repel solder paste, preventing it from sticking to the underside of the stencil.
Perhaps the most misunderstood fact about these SAM coatings is they do not improve paste release from the stencil apertures. There are multiple papers available from different authors that show transfer efficiency or paste release is not improved with SAM coatings. These coatings, however, can be reapplied when the hydrophobic properties diminish. They are beneficial for underside cleaning, reduce bridging, and improve variation in the print process. But please understand, these coatings are not the solution to improve paste release.
The second type of nano coating available in North America is ceramic coatings made for SMT stencils. These coatings are proven to increase transfer efficiency of solder paste up to 25%; an example of this type of coating is NanoSlic Gold.
Figure 3: Dyne Pen examples.
Ceramic coatings are applied with precision spray equipment to the bottom or board side of the stencil and on the stencil aperture walls. The coating thickness is in the range of two to four microns, which is one thousand times thicker than SAM coatings. There is a yellow dye in the NanoSlic coating that will fluoresce under UV light. The purpose of this is to be able to validate the coating presence in the apertures walls using a scope and UV light source. After the coating is applied with precision spray equipment, a curing process is used creating a very hard, chemically resistant coating on the stencil.
Figure 4: Ceramic coating.
Figure 4 shows the three layers that form during this curing process. At the surface of the foil, a bonding layer is formed where the chemistry attaches itself to the stencil foil. A center layer is also formed giving the coating a strong, hard, durable structure. The top layer is hydrophobic and oleophobic, which repels the flux in the solder paste and prevents it from sticking in both the apertures and on the bottom surface of the stencil.
The primary benefits of this type of coating are reduced underside cleaning, reduced bridging, and improved paste release, especially in small area ratio printing.
I have spent a lot of time testing and documenting the benefits of these ceramic coatings and presented a paper “Stencil Nano Coatings: Do They Improve Repeatability and Uniformity in The Print Process?” at the 2018 IPC APEX EXPO Technical Conference including Figure 5. As you can see, ceramic nano coatings improve solder paste release as component sizes and aperture area ratios get smaller. We have many customers that specify ceramic nano coatings when stencils are ordered to print 0201 components or smaller. They experience more consistent paste deposits, less process variation, and less first-pass defects as a result.
Figure 5: Solder paste transfer efficiency based on component type and area ratio.
As discussed earlier, one reason ceramic nano-coated stencils provide improved solder paste release is the hydrophobic and oleophobic properties of the coating itself. Another reason is the coating fills in rough areas of the aperture walls and smooths them. This can be seen in the SEM photographs (Figures 6). The coating fills the peaks and valleys created during the laser cutting process and smooths the aperture wall surface. It is both the resulting smoother surface in combination with the surface energy created by the coating itself that repels the paste providing improved paste release and consistency of the printed solder paste brick, and reduced variation in the overall print process.
Conclusion
To conclude the second part of this column, I want to stress the importance of understanding that not all stencil nano coatings are the same.
Figure 6: (L) uncoated aperture, and (R) ceramic nano-coated aperture.
If the stencil user is wanting to improve process variation and there are no small area ratio apertures to address, SAM coatings work perfectly. However, if the use of stencil nano coatings is based on product miniaturization and there are apertures in the stencil with area ratios less than 0.66, it is important to understand only ceramic nano coatings will improve solder paste release or transfer efficiency.
Greg Smith is manager of stencil technology at BlueRing Stencils. To read past columns or contact Smith, click here.
More Columns from SMT Stencils 101
SMT Stencils 101: Root-cause Stencil Design, Part 3—Tearing Down BridgesSMT Stencils 101: Root-cause Stencil Design, Part 2—Tombstones
SMT Stencils 101: Root-cause Stencil Design, Part 1—Solder Balls
SMT Stencils 101: What Are Industry-standard Stencil Designs?
Overcoming the Challenges of Miniaturization with New Stencil Technologies, Part 1: Solder Paste Release
A Brief History of Solder Stencil Manufacturing