-
- News
- Books
Featured Books
- smt007 Magazine
Latest Issues
Current IssueWhat's Your Sweet Spot?
Are you in a niche that’s growing or shrinking? Is it time to reassess and refocus? We spotlight companies thriving by redefining or reinforcing their niche. What are their insights?
Moving Forward With Confidence
In this issue, we focus on sales and quoting, workforce training, new IPC leadership in the U.S. and Canada, the effects of tariffs, CFX standards, and much more—all designed to provide perspective as you move through the cloud bank of today's shifting economic market.
Intelligent Test and Inspection
Are you ready to explore the cutting-edge advancements shaping the electronics manufacturing industry? The May 2025 issue of SMT007 Magazine is packed with insights, innovations, and expert perspectives that you won’t want to miss.
- Articles
- Columns
- Links
- Media kit
||| MENU - smt007 Magazine
Estimated reading time: 12 minutes
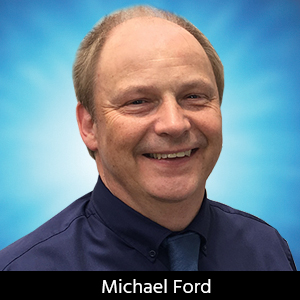
The Truth Behind AI
The term "artificial intelligence" or "AI" has become a source of confusion for many—heralded as part of Industry 4.0, yet associated with the threat of automation replacing human workers. AI is software rather than hardware, and not yet the entity that destroys civilization, as Hollywood movies would have us believe. It’s time to put these elements of AI into context, enabling us as an industry to embrace the opportunities that so-called AI represents without being drawn in, or pushed away, by the hype.
What is AI to You and Me?
There are two distinct flavors of AI in people’s minds. The first came in for many as plotlines in Hollywood movies where futuristic machines would take over the world. The critical element of the story is not the machines that do harm, but the software that drives them where a sophisticated algorithm became able to think for itself in a way that was likely not intended. It is this aspect of achieving thought without the specific coding of such thought processes that define true intelligence. Humans are credited with having intelligence already, though there may be exceptions. Machines, on the other hand, are guided only by their software, which is limited to being reactive to events that take place and are communicated to them today. They follow a set of rules designed to achieve the desired result.
It is claimed that general human behavior can also be modelled, albeit by a far more sophisticated and evolved process. The achievement of, or at least the perception of intelligence, could well be simply an extension of the ways computer software algorithms work, which would have to be the case if machines were ever to think for themselves. This allows many to claim “intelligence” in our current assembly machines and related software. Such claims are designed to set customer expectation that newer products are much cleverer than before, creating more value and performance, which in most cases, is a neat and accurate description of new machines and robots we see coming into the market.
Becoming smarter and more intelligent step by step is great, but how many steps are there left to take before we reach a truly artificially intelligent process that can think for itself? The continuous investment in AI is bankrolled from sales of continuously enhanced machines and software. With things moving so fast, when is the best time to invest in smart solutions when the next step may be just around the corner? If an investment is made into state-of-the-art smart software solutions today, would it become obsolete in the very near term?
No, and the reason is that there is a growing distinct difference between the hardware and software elements of smart solutions. The difference has so far been hidden, as most physical tools that we purchase for use in assembly manufacturing consist of a package of both hardware and software. To evolve hardware requires a long lead time due to physical product development cycle constraints, whether mechanical or electronic. Meanwhile, evolving software can be done orders of magnitude faster. We all have experience with devices, ranging from smartphones and PCs to the latest SMT placement or inspection machines, to find that there are frequent software updates that change and (usually) enhance the operation of the hardware device. Don’t think that the machine vendor missed the opportunity to add value at the start, or that there was any problem with the original machine or device software; those days are largely passed.
As software is not a physical entity, it evolves more as a flow rather than large step by step iterations of hardware, so new values can be introduced as they become available. This fundamentally changes the way we invest in software solutions. We see today that Microsoft has stopped releasing new versions of Windows, and instead, is providing incremental updates continuously to customers who see what they use as being Windows 10. If each change to Windows had a major release, we would probably be running something like Windows 42 by now with each new release bringing with it costs and concerns. Instead, improvements are introduced gradually, with minimal impact on usage. Hardware has a limited rate of evolution seen as products evolving in discrete steps, whereas software is free to roam in a far more flexible way, delivering greater flexibility and greater opportunity for becoming smarter and faster. This all comes for an initial investment, or preferably these days, a subscription that allows us to pick and choose exactly what software we would like to use as time progresses. This is quite critical as the pace towards AI in software picks up momentum.
The Origin of Digital Intelligence
The chicken-and-egg discussion of whether hardware development leads to software or vice versa is more interesting now that we see software evolution as a flow compared to the stepped changes in hardware. However, software enhancement has begun to break away from the hardware where AI applications and smart operations are concerned. An interesting example, historical to many, is the evolution of the smart warehouse. Without software, the typical original warehouse model was to organize locations by part number with some sort of bin allocated for each. These were arranged in alphabetical order so that human materials operators could easily find materials to create kits. Unfortunately, this has never been an efficient use of space in a warehouse. As new part numbers were introduced and others became obsolete, gaps would need to be physically created or closed up. Many bins would overflow or go for long periods of little utilization as consumption rates varied over time. Changing bin sizes and moving the bins around represents a major physical challenge, creating significant temptation to simply work around the exceptions and rely on human flexibility to cope.
The first simple warehouse management software came to the rescue, as it was realized that computers were usually far better than humans at remembering where materials had been stored to the extent that alphabetized order was no longer required. Materials could be put away anywhere usually into any unused bin—which was a model known as random storage. The selected location would be recorded against the part number and quantity so the software would later direct material operators when the materials were needed.
On the hardware side, this triggered the step change in the development of automated logistics with things such as automated guided vehicles and cranes. Knowing exactly where materials were, and the adoption of standard bins or racks, made automation viable. The evolution of the hardware has been progressive ever since to the state of the art we currently see in the warehouses of the largest online retailers. This hardware replaces the work that many people used to do. This is mechanical automation based on standardization, effectively Industry 3.0. However, it is true that the control mechanisms within such machines have become smarter based again on hardware development; specifically, sensors mimicking our own innate senses and connectivity allow the machines to make a wider variety of automated decisions. These are not necessarily smart in themselves until the addition of AI in terms of software.
The Digital Sixth Sense
The evolution of smart software is dependent on the availability of understandable data. As humans, we have a huge amount of data input to process through our already evolved five senses continuously. A sixth sense may need to be artificially introduced if people wish to become connected such as to the internet directly without the need to see, hear, speak, or type in the future. Unlike people, machines today are acquiring and evolving their sixth sense very quickly, with, for example, the revolutionary IPC’s Connected Factory Exchange (CFX) now in place that enables machines and systems of all types and from all vendors to talk freely with each other through a commonly defined language. As human intelligence came out of data from the five senses, digital intelligence starts primarily with the evolution of the sixth.
The Evolution of Digital Intelligence
Continuing with the smart warehouse solution, once the Industry 3.0 hardware was in place, software AI stepped in with Industry 4.0. The idea of the word random immediately puts a question in many people’s minds as to how efficient a system can be based on anything that is random. Having operators searching around for an available empty location to put materials is quite a major waste. The intelligence of digital warehouse systems comes from the need to address that. The warehouse solution software knows the content of each location and can direct putting away materials, either by human or machine, to specifically chosen locations.
The cleverness comes with the selection of the location. If the software developer knows the travelling distance between bins and the material checkout point is an issue, the software can be developed to look at which materials are more commonly used and locate them closer to the checkout, for example; it can even start to optimize the path of travel to collect sets of materials as needed. This speeds up the access of materials, decreasing the material replenishment cycle times. The size, type, and form of materials can be considered as well as whether the materials have specific storage constraints, such as electrostatic or moisture sensitivity. Material storage location decisions may also be affected by the ownership of the material, cost, whether new or used, whether on a carrier such as a feeder, tax exemption, or critical for specific industry sectors, etc. Materials are being stored optimally rather than randomly—an automated process performed by an AI—but is just a software algorithm where decisions are based on the knowledge of the programmer to make certain things happen in certain ways.
Discrete software algorithms for the majority optimization application were originally developed to mimic the ways that humans would approach a problem, and then do it faster and more accurately. Over time, as humans no longer wanted to approach increasingly complex optimization problems in this discrete fashion, digital modelling of operations took over. Rather than create a specific logical procedure in software to follow, starting with so-called “genetic” algorithms, the software was developed to define a set of rules that would measure the effectiveness of a solution through a process of scoring what worked and what didn’t against the targets.
Random combinations of solutions criteria were set up, each of which was measured by the software. This was then repeated with different combinations, often millions of times, until the best result was found, which was very much a trial-and-error process. This method was found to be less suitable than expected for more complex problems because with each additional element to the problem, the number of iterations required to reach the best result increased exponentially. However, on the measurement side, software became easier to develop an application of these kinds of algorithms to different problems simply meant the alteration of the measurement system. Techniques were created to reduce the randomness of the criteria arrangement in attempts to speed up the process. Even so, the best optimization of an SMT machine program would take hours. Compromises to finish early were introduced to allow the customer to accept a fairly good optimization in a reasonable time.
Frustratingly State of the Art
In the warehouse, we cannot wait hours, minutes, or even seconds for any smart software to make decisions, even with the addition of tons of digital horsepower in the computer hardware to make things appear in real time. The decision-making needed with Industry 4.0 such as guiding materials to be put away in a warehouse, analyze the result of a visual inspection, etc., requires us to take a different approach, potentially combining the discrete algorithms and those based on the trial-and-error approach. We are still a few steps away from seeing the software making fast and complex intelligent decisions in automated Industry 4.0 for the whole factory. The levels of investment into doing so have to be reasonable and based on incremental added customer value.
True Digital Intelligence
To achieve the state where software developers can once again relax and let the truly intelligent software take over is something that perhaps can be learned from humans, specifically, very young humans. As children develop, it is through a natural process of trial and error. Our five senses are there to communicate pain and pleasure. Our human algorithms prefer the latter in most cases, and we continuously learn and modify our actions built on the experience gained.
With software having access to more and more data, utilizing their sixth sense connection of connectivity, there is the potential to start to do similar activities. Creating the will to try things in different ways, to see whether “pleasure” can be gained by doing something new, is the genesis of the true AI algorithm. AI software developers need to define what defines pain and pleasure, that is, the reward structure for any given digital solution. Factory managers around the world already have a wealth of this experience, and if we are truthful, will have earned it based on many cases of trial and error. The cool thing about AIs in the digital age is that unlike the human manager, there is no need to relearn experiences as people rotate in and out of roles. Even though it may seem crazy to put the intelligence of a baby in charge of a factory at the start, it only needs to happen once. It may not even need to start off in the physical world.
Conclusion
Being a part of the AI evolution journey is beneficial to factory operations and interesting. Evolution towards cleverer software algorithms, and even to real AI, is already unlike that of hardware in terms of the way value is added. Investment into a progressive, digital MES software package provides way more value than generic MES solutions. Being a subscriber to digital MES today will prove to be the most rewarding investment a factory could make as we see the dawn of intelligence applied into more and more aspects of factory operational decision-making as well as operator process augmentation.
Solutions with such capability need to be chosen with care, looking towards those who lead the industry in terms of the vision of such technologies. With the advent of technologies such as IPC CFX, it may just seem like a smarter and more cost-effective way to do interfacing to many. However, in reality, CFX opens up the potential for a far greater step forward in AI, for which some of us are prepared. This is a clear differentiator between entities that have been key contributors and leaders throughout the development of CFX and those who will simply provide a new interface for their old software. It is not hard to see which path leads to a greater reward.
More Columns from Smart Factory Insights
Smart Factory Insights: Making Rework a Smart Business OpportunitySmart Factory Insights: The Sustainability Gold Rush
Smart Factory Insights: Today’s Manufacturing Jobs Require a New Skill Set
Smart Factory Insights: Compose Yourself, Mr. Ford
Smart Factory Insights: The Smart Business Case for Local PCB Manufacturing
Smart Factory Insights: Manufacturing Digital Twin—Spanners in the Works
Smart Factory Insights: Machines, People, and AI
Smart Factory Insights: Is Sustainability in Manufacturing a Benefit or Burden?