-
- News
- Books
Featured Books
- design007 Magazine
Latest Issues
Current IssueShowing Some Constraint
A strong design constraint strategy carefully balances a wide range of electrical and manufacturing trade-offs. This month, we explore the key requirements, common challenges, and best practices behind building an effective constraint strategy.
All About That Route
Most designers favor manual routing, but today's interactive autorouters may be changing designers' minds by allowing users more direct control. In this issue, our expert contributors discuss a variety of manual and autorouting strategies.
Creating the Ideal Data Package
Why is it so difficult to create the ideal data package? Many of these simple errors can be alleviated by paying attention to detail—and knowing what issues to look out for. So, this month, our experts weigh in on the best practices for creating the ideal design data package for your design.
- Articles
- Columns
- Links
- Media kit
||| MENU - design007 Magazine
Estimated reading time: 1 minute
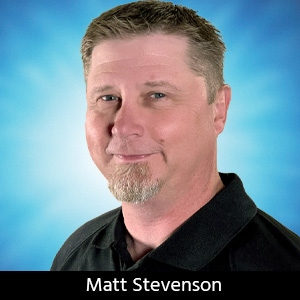
Connect the Dots: Five Best Practices to Ensure Manufacturability
Optimizing your board using design for manufacturability (DFM) techniques just makes sense. But without formal training, this isn’t as straightforward as one would hope. Every day, our team receives designs that are too complex, too thick, incomplete, with components placed too close together, among other things.
When something like this happens, rejection of your design is a best-case scenario because it means your manufacturing partner has your back. If your design is just dropped into an automated queue without concern for manufacturability, quality, or functionality, the output can be a batch of unusable boards.
This doesn’t have to happen because you are in control of your vendor choice. While not a replacement for good design practice, carefully picking a manufacturing partner and service level that meet your needs will help you achieve a quality result.
Now, let’s examine five design best practices that will help reduce costs, increase yield, and improve manufacturability.
1. Always Double Check Your Design
It will save you time on the front end. Regardless of which partner or service level you choose, I strongly encourage you to be sure to review your design, taking a second look for issues, such as insufficient power trace widths or blind vias. Ditto if components are laid out too close together. It is easy to accidentally cut holes or route slots too close to pads or traces.
Copper thickness is another biggie. Higher current may require thicker copper and narrow traces probably should be thinner, so be specific about what you need to ensure your design will not fail. Check land patterns against the part supplier’s manufacturer data sheets (MDS) as well. Often, that’s all it takes to avoid common design issues.
2. Always Consider Your Environment
When you send your design for manufacturing, your partner does not know what type of device the board will be part of nor the conditions in which it will have to perform. It’s common for harsh environments or exposure to mess up a board’s performance. If you call out materials that will not tolerate the end-product’s operating environment, bad things can happen—such as a smoking board, for example. Be sure your board can tolerate thermal stress or solder joints risk breaking and damaging components.
To read this entire column, which appeared in the July 2019 issue of Design007 Magazine, click here.
More Columns from Connect the Dots
Connect the Dots: Sequential Lamination in HDI PCB ManufacturingConnect the Dots: The Future of PCB Design and Manufacturing
Connect the Dots: Proactive Controlled Impedance
Connect the Dots: Involving Manufacturers Earlier Prevents Downstream Issues
Connect the Dots: Stop Killing Your Yield—The Hidden Cost of Design Oversights
Connect the Dots: Designing for Reality—Routing, Final Fab, and QC
Connect the Dots: Designing for Reality—Surface Finish
Connect the Dots: Designing for Reality—Solder Mask and Legend