-
- News
- Books
Featured Books
- design007 Magazine
Latest Issues
Current IssueProper Floor Planning
Floor planning decisions can make or break performance, manufacturability, and timelines. This month’s contributors weigh in with their best practices for proper floor planning and specific strategies to get it right.
Showing Some Constraint
A strong design constraint strategy carefully balances a wide range of electrical and manufacturing trade-offs. This month, we explore the key requirements, common challenges, and best practices behind building an effective constraint strategy.
All About That Route
Most designers favor manual routing, but today's interactive autorouters may be changing designers' minds by allowing users more direct control. In this issue, our expert contributors discuss a variety of manual and autorouting strategies.
- Articles
- Columns
- Links
- Media kit
||| MENU - design007 Magazine
Estimated reading time: 4 minutes
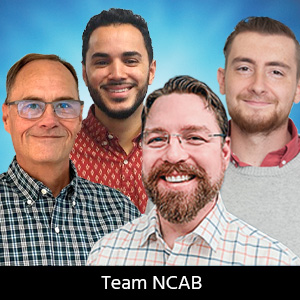
Fresh PCB Concepts: Getting It Right From the Start
When faced with critical time-to-market situations, it is all too easy to say, “It doesn’t matter because this is just the prototype; we can fix this later.” However, if the design is perfected from the beginning, cost savings can be applied, and manufacturability can be ensured. Perhaps most importantly, the design can be adapted with reliability in mind, leaving a seamless transition from prototype to production. How do we get it right from the start?
One way NCAB does this is by not just supporting the customer but also the integral part of the product—the PCB designer. It is critical for feedback to flow from the designer to the assembly house and all the way to the PCB fabricator. The majority of the cost is built into the product in an early stage of the chain before either EMS companies or the PCB factory has sight of the design; we see that 80–90% of the cost originates here. Not only does this apply to cost but also to manufacturability and reliability. Simple suggestions like base materials, surface finish, and copper weights can have a major impact on the ease of build and longevity of the end product. It is essential to involve your PCB manufacturer at the initial concept stage to help ensure the right questions are raised and answered.
This is all part of the concept of design for excellence, or DFX (Figure 1); 50–60% of the cost is related to or built in by the design of the PCB. When customers are involved in the DFX analysis, we can find and correct problems much earlier. The later the problem is discovered, the more the cost and cycle will be impacted. The value of DFX is reflected in the design phase to anticipate and solve most of the production problems. Figure 2 details some of the elements of DFX.
By designing for manufacturing right from the start and following design guidelines, fewer materials are used, and waste is also reduced. This benefits both the environment and production costs. Here are some of the main factors that influence cost:
- The size of a single unit
- The thickness of PCB
- The surface treatment, including thick gold
- The copper thickness
- Panel size/low material utilization
- General specifications, underspecifying or overspecifying
- Material selection
- Factory selection
- The manufacturability of the design
Some design attributes can push up to or exceed the PCB manufacturer’s capabilities, which is territory no one wants to step into. Generating a design that is manufacturable no matter where the supply chain sends it to be built should be everyone’s goal. Thus, DFM gives consideration to the following areas (Figure 3):
- Problems in documentation
- Good designs vs. bad designs
- Required tolerances
- Factory capabilities
Our experience shows that misinformation in the design occurs in about 30% of all the new articles that are handled by our company. Engineering questions are raised that take time to clarify and can affect delivery dates, which ultimately results in increased costs.
So, what if there was a way to reduce engineering questions and improve manufacturability? NCAB has created detailed design guidelines with our recommendations for everything from spacing to surface finish. These recommendations account for the gap between prototype and production facilities and help ensure a design that can be manufactured globally (Figure 4).
Again, aiming for better PCB designs, stable production, improved yields, and shorter time to market helps bridge the gap between prototype and volume production. This way of working is applicable to all stages, from design to prototypes and volume production. Here are some of the reasons it’s important to look at the big picture when it comes to designing a board from prototype through production:
- Prototype cost drivers are not always optimal for volume production
- The disconnect between prototype and volume producer leads to an inefficient process and increases time to market
- There are often differences between the technology capabilities of the prototype and volume factory; with the prototype being purchased first, such aspects can be incorporated into the design
- Gap = additional resources to solve = more questions = redesign? = delay = higher total cost
The aim is to consider volume production and technical competence at the design stage, utilizing options available in the supply chain. Engaging with a partner who has this knowledge and capabilities benefits the design at every stage reduces risk, and the potential cost and time of product redesign after volume production has started.
We have found our design guidelines to be helpful with improving manufacturability and reducing engineering questions when our customers design to our specification. In addition to producing our own design guidelines for multilayer, HDI, and flex/rigid-flex boards, we recently teamed up with Cadence Design Systems to provide a set of criteria that can be used within Cadence’s DesignTrue DFM design software. Using this software can help ensure that the design adheres to the most up-to-date capabilities and provides which suppliers can manufacture a PCB.
Overall, following a solid set of DFX guidelines will ensure that the PCB is manufactured in the best way possible for efficiency, cost, and production. With DFX analysis, PCB designers can truly “get it right the first time.”
Jeff Beauchamp is a field application engineer at NCAB Group.
More Columns from Fresh PCB Concepts
Fresh PCB Concepts: More Than Compliance—A Human-centered Sustainability ApproachFresh PCB Concepts: Assembly Challenges with Micro Components and Standard Solder Mask Practices
Fresh PCB Concepts: The Power of a Lunch & Learn for PCB Professionals
Fresh PCB Concepts: Key Considerations for Reliability, Performance, and Compliance in PCBs
Fresh PCB Concepts: Traceability in PCB Design
Fresh PCB Concepts: Tariffs and the Importance of a Diverse Supply Chain
Fresh PCB Concepts: PCB Stackup Strategies—Minimizing Crosstalk and EMI for Signal Integrity
Fresh PCB Concepts: PCB Plating Process Overview