-
- News
- Books
Featured Books
- design007 Magazine
Latest Issues
Current IssueShowing Some Constraint
A strong design constraint strategy carefully balances a wide range of electrical and manufacturing trade-offs. This month, we explore the key requirements, common challenges, and best practices behind building an effective constraint strategy.
All About That Route
Most designers favor manual routing, but today's interactive autorouters may be changing designers' minds by allowing users more direct control. In this issue, our expert contributors discuss a variety of manual and autorouting strategies.
Creating the Ideal Data Package
Why is it so difficult to create the ideal data package? Many of these simple errors can be alleviated by paying attention to detail—and knowing what issues to look out for. So, this month, our experts weigh in on the best practices for creating the ideal design data package for your design.
- Articles
- Columns
- Links
- Media kit
||| MENU - design007 Magazine
Estimated reading time: 4 minutes
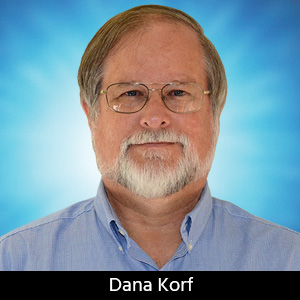
New Column—Dana on Data: IPC-2581 Intelligent Bi-directional Data Flow
PCB designs are significantly increasing in complexity, NPI cycle times are being shortened, and there is no time for back-and-forth questions and answers during DFM reviews. Prototype-to-mass-production transitions don’t have additional NPI cycles to perform radical design updates to improve yields and/or reliability. Higher-speed, lower-loss 5G products require that the designer control all edits and materials. Further, undocumented changes may make the circuit non-functional.
These producibility or capability matching edits may not have caused any functional issues in the past, but data transfer to an assembler and fabricator requires that significant information and constraints be incorporated into the data package. The common data files utilize non-intelligent RS-274X (Gerber) graphical data with “ePaper” PDF, RS274X, Excel spreadsheet, email, and other forms of non-machine-readable information to transmit notes and tolerances. CAD systems also export the ODB++ format to add intelligence to the graphical information, which requires humans to read, interpret, and transpose this information into their internal databases and CAM/engineering software to create production files (Figure 1).
Figure 1: Automated data transfer functional status.
It is also common in today’s global environment that a person in a non-English-speaking country must translate the manufacturing documentation into English, which is then translated from English into another language. These translations may create wrong requirements and lead to potentially confusing communication that can be misinterpreted or ignored. Misinterpretation creates PCBs that do not meet the documentation or performance requirements, requiring a root-cause analysis and re-build. In turn, this adds to the NPI cycle time.
The IPC-2581 open, non-proprietary, XML-based data format is structured to eliminate these additional files and have bi-directional information transmitted between OEMs/ODMs and assembly and fabrication teams. It was established more than 10 years ago and used the Valor ODB++ XML format as its basis, which was donated to the industry. The data format can incorporate SMT assembly, BOM, test, and PCB fabrication data, as required (Figure 2).
Figure 2: Intelligent, single-file open standard.
There are over 100 global companies that are active members of the IPC-2581 Consortium (find out more at www.ipc-2581.com). The supporting member companies are from the following industries:
- CAD
- CAM
- PLM
- Analysis
- Manufacturing software
- Manufacturing
IPC-2581 complements the new CFX IPC-2591 factory automation protocol and is currently being used globally. Focusing on the bi-directional PCB fabrication information content, the format is structured to integrate the following information (Figure 3).
Figure 3: Existing fabrication files.
Graphical Layers
Intelligent graphical data has been in use for many years. Individual trace electrical and mechanical constraint properties are automatically loaded into the CAM and engineering systems.
Stackup and Impedance
There is no need to send a stackup picture embedded with the trace width/space constraint table from the designer to the fabricator. The PDF or Excel file that is handed off is typed into the fabricator’s stackup modeler and possibly a third-party impedance simulation tool in the fabricator’s format to evaluate if the provided constraints can be fabricated per the requested requirements. If not, a new set of proposed modifications are then typed into the format that the designer requires and sent back to them for review.
IPC-2581 just sends the material, impedance, and loss constraints in an XML file, which are loaded directly into the CAM/engineering system for review in the fabricator’s format. The proposed changes are then sent back as an XML file to the designer who automatically loads it into their format. Thus, transcription time and errors are eliminated.
Fabrication Print Notes and Tolerances
Drilled hole and slot tolerances, for example, can be automatically entered into the fabricator’s system from the IPC-2581 file. It eliminates them having to type the tolerances that are manually read from the embedded Gerber or PDF file. Cycle time is reduced, and errors are eliminated.
Industry, OEM, ODM, and CEM Specifications
IPC-2581 can incorporate industry, OEM, ODM, and CEM specifications. This is currently being defined.
Fabricator Capability Attributes and Rules
Fabricator design rules can be electronically sent and loaded into the CAD system if the interface is available. An industry-standard naming convention is currently being defined by the IPC Consortium (Figure 4).
Figure 4: IPC-2581 stackup data transfer.
How do I convert from a Gerber/PDF file-based process to an IPC-2581-based process? Most major CAD and CAM systems can export and import IPC-2581 files. The conversion process generally involves sending existing file formatted files along with IPC-2581 files to your supplier to be compared to ensure that they are converted properly. This process has been performed for many years for both Gerber to ODB++ and Gerber to IPC-2581 conversions. Free viewers are available and can be obtained from the IPC Consortium website.
The IPC Consortium is nearing completion of transferring notes on drawings and working with IPC on converting key IPC specifications into attributes that can be automatically loaded into CAD and CAM systems. This format is extendable to created automated company-specific acceptance files that can be automatically loaded into the CEM’s or fabricator’s engineering systems. IPC-2581 data format is being widely used globally and now needs to become the standard to reduce NPI cycle times by associating critical design information automatically to the physical features.
Dana is the principal consultant at Korf Consultancy LLC.
More Columns from Dana on Data
Dana on Data: The Missing AI-NPI LinkDana on Data: Merging 2D Electrical, 3D Mechanical Worlds
Dana on Data: Resurrecting IPC Class 1
Dana on Data: The Evolution of Fabrication Drawing
Dana on Data: The Insane PCB DFM Process
Dana on Data: eCAD PCB Design Deficiencies
Dana on Data: Nuke the Netlist
Dana on Data: Simplify PCB Documentation