-
- News
- Books
Featured Books
- design007 Magazine
Latest Issues
Current IssueAll About That Route
Most designers favor manual routing, but today's interactive autorouters may be changing designers' minds by allowing users more direct control. In this issue, our expert contributors discuss a variety of manual and autorouting strategies.
Creating the Ideal Data Package
Why is it so difficult to create the ideal data package? Many of these simple errors can be alleviated by paying attention to detail—and knowing what issues to look out for. So, this month, our experts weigh in on the best practices for creating the ideal design data package for your design.
Designing Through the Noise
Our experts discuss the constantly evolving world of RF design, including the many tradeoffs, material considerations, and design tips and techniques that designers and design engineers need to know to succeed in this high-frequency realm.
- Articles
- Columns
- Links
- Media kit
||| MENU - design007 Magazine
Communication, Part 5: Internet Impedance Calculators for Modeling
November 5, 2019 | Steve Williams, The Right Approach Consulting LLCEstimated reading time: 4 minutes
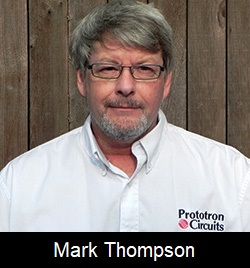
Bob Chandler of CA Design and Mark Thompson of Prototron Circuits address how new engineers use internet impedance calculators for modeling (e.g., formulas versus recipes) in Part 5 of this series.
Steve Williams: Today, we want to talk today about a phenomenon that I wasn’t personally aware of until Mark brought it to my attention, which surrounds engineers going on the internet, searching for impedance modeling calculators, and using that to come up with their impedance calculations. Bob, what do you think about that?
Bob Chandler: It is definitely happening. I like to talk to about it as formulas versus recipes, and engineers love to deal with formulas, where they key in the numbers and come up with the solution. They’re not used to dealing with recipes, where you take the basic ingredients, and depending on how you process those, come up with totally different products. Once, the same board with the same data was manufactured at two different fab houses and had completely different controlled impedances, even though the trace widths, materials, etc., were identical. One shop fabricated it at a slightly different temperature and pressure than the other one, which resulted in a completely different controlled impedance. So, talk to your fabricator because the process has as much impact on the controlled impedance as the material and trace width do.
Williams: We’ve talked in the past about some designers just throwing out boilerplate notes and requirements on drawings. This sounds like the same thing, but there are a lot more consequences if that happens.
Mark Thompson: Absolutely. And Bob brings up a great point. Even if you have the same stackup of the same material and the same trace and space sizes, because of different press parameters and environmental conditions, all kinds of other factors can combine to make deviations in those impedances. And that’s where the conversation between the designer and the fabrication house takes place.
First, I see that some folks use online calculators, like those provided by the Missouri University of Science & Technology [formerly the University of Missouri-Rolla]. However, if you look at it and the Z-axis shape of the trace, it has vertical walls; it’s a rectangular slab. There is no etchant in the world that works perfectly with 90° corners. Second, calculations are frequently made without any solder mask or polymer mask plastic over the top of the traces, which will also affect the impedances. Third, sometimes, a wrong dielectric constant is used.
Williams: How should companies do their modeling? Should it be based on experience, software, or working with the design bureau?
Thompson: The best way to do it is, as Bob said, is to start with a conversation between the engineer and designer and agree on the material, copper weight, color of the solder mask, whether or not there will be free space structures, and whether or not there will be coplanar structures. Beyond that, I can provide that information, and include all the effective dielectric contents of all of the subsections based on Prototron Circuits.
Chandler: The main thing is to go back to the fabrication house and ask them what they would prefer. Because if you design your board was a certain setup, and then you send it to the fabrication house for a three-day turn, and they can’t manipulate the numbers, your three-day turn turns into a one week and three-day turn, as they have to special order materials.
Williams: That’s a great point.
Thompson: And in today’s world, where people are designing with 0.1-millimeter lines and spaces, any deviation where I have to increase or decrease that trace or space may throw us out of the game and make it not producible for a fabrication house. Nothing ruins a designer’s day more than having a fabrication house calling and saying, “I’m sorry, but we can’t get there from here.”
Williams: Out of all the business that you do, Mark, how much of it requires controlled impedance and modeling?
Thompson: That’s a great question. When I started here 23 years ago, I brought controlled impedance on board; we didn’t do any—only four and six layers. We started out with four- and six-layer impedances, very simple stripline constructions and dual asymmetrics, some at 50 ohms, others at 100 ohms, etc.. Now, over 70% of all the jobs that come through Prototron today are signal integrity.
Williams: So, it’s a big deal.
Thompson: Yes.
Williams: Bob, how does that match up to your designs as far as how many have controlled impedance and people’s requirements?
Chandler: It’s very similar, probably 70–80%, depending on our current customer base. Some of our customers have many more requirements for it, and others are much less requirement-driven.
Williams: It sounds like you and Bob are on the same page, at least.
Thompson: Without a doubt.
Editor’s note: Read Part 1, Part 2, Part 3, and Part 4, and stay tuned for the final installment of this series.
Steve Williams is the president of The Right Approach Consulting and an I-Connect007 columnist.
Bob Chandler is CTO of CA Design (cadesign.net) and a senior Allegro/OrCAD trainer and consultant.
Mark Thompson, CID+, is in engineering support at Prototron Circuits and an I-Connect007 columnist. Thompson is also the author of The Printed Circuit Designer's Guide to… Producing the Perfect Data Package. Visit I-007eBooks.com to download this book and other free, educational titles.
Suggested Items
Driving Innovation: Direct Imaging vs. Conventional Exposure
07/01/2025 | Simon Khesin -- Column: Driving InnovationMy first camera used Kodak film. I even experimented with developing photos in the bathroom, though I usually dropped the film off at a Kodak center and received the prints two weeks later, only to discover that some images were out of focus or poorly framed. Today, every smartphone contains a high-quality camera capable of producing stunning images instantly.
Hands-On Demos Now Available for Apollo Seiko’s EF and AF Selective Soldering Lines
06/30/2025 | Apollo SeikoApollo Seiko, a leading innovator in soldering technology, is excited to spotlight its expanded lineup of EF and AF Series Selective Soldering Systems, now available for live demonstrations in its newly dedicated demo room.
Indium Corporation Expert to Present on Automotive and Industrial Solder Bonding Solutions at Global Electronics Association Workshop
06/26/2025 | IndiumIndium Corporation Principal Engineer, Advanced Materials, Andy Mackie, Ph.D., MSc, will deliver a technical presentation on innovative solder bonding solutions for automotive and industrial applications at the Global Electronics A
Fresh PCB Concepts: Assembly Challenges with Micro Components and Standard Solder Mask Practices
06/26/2025 | Team NCAB -- Column: Fresh PCB ConceptsMicro components have redefined what is possible in PCB design. With package sizes like 01005 and 0201 becoming more common in high-density layouts, designers are now expected to pack more performance into smaller spaces than ever before. While these advancements support miniaturization and functionality, they introduce new assembly challenges, particularly with traditional solder mask and legend application processes.
Knocking Down the Bone Pile: Tin Whisker Mitigation in Aerospace Applications, Part 3
06/25/2025 | Nash Bell -- Column: Knocking Down the Bone PileTin whiskers are slender, hair-like metallic growths that can develop on the surface of tin-plated electronic components. Typically measuring a few micrometers in diameter and growing several millimeters in length, they form through an electrochemical process influenced by environmental factors such as temperature variations, mechanical or compressive stress, and the aging of solder alloys.