-
- News
- Books
Featured Books
- design007 Magazine
Latest Issues
Current IssueProper Floor Planning
Floor planning decisions can make or break performance, manufacturability, and timelines. This month’s contributors weigh in with their best practices for proper floor planning and specific strategies to get it right.
Showing Some Constraint
A strong design constraint strategy carefully balances a wide range of electrical and manufacturing trade-offs. This month, we explore the key requirements, common challenges, and best practices behind building an effective constraint strategy.
All About That Route
Most designers favor manual routing, but today's interactive autorouters may be changing designers' minds by allowing users more direct control. In this issue, our expert contributors discuss a variety of manual and autorouting strategies.
- Articles
- Columns
- Links
- Media kit
||| MENU - design007 Magazine
Estimated reading time: 4 minutes
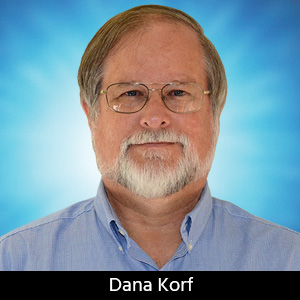
Dana on Data: The DFM/Data Transfer Process Is Broken
In a world that is showing great strides toward implementing a Factory 4.0 world, why can’t a design be passed from a designer to the fabricator without errors every time? The current PCB design transfer process assumes that an OEM/ODM/CM can send an incomplete and/or incorrect data package to be fabricated with the knowledge that the fabricator will fix it (Figure 1).
Figure 1: Design and DFM data flow.
Somewhere back in time, a fabricator didn’t find a design or documentation error during pre-engineering, built boards that didn’t work, and then said, “I’m sorry. We’ll rebuild it for free for not finding and fixing your mistake.” Then, this became the standard. However, this fundamental premise needs to change. Let’s cause a paradigm shift to change the goal to “transfer designs without any technical queries (TQs) being created.”
Companies have spent hundreds of millions of dollars on PCB layout, DFM review, and documentation systems, but less than 2–20% of the designs transfer to manufacturing perfectly without any deviation requests or TQs being generated and negotiated. And fabricators have spent tens of millions of dollars on analysis software to detect many of these errors.
Board fabricators perform pre-release design DFM reviews that highlight issues and have experienced field application engineers (FAEs) work directly with layout designers and engineers to “eliminate” the design/documentation errors. However, the PCB designs still arrive with issues, so TQs are sent to the data provider to determine how to resolve the issues before production release. Often, 25–50% of a PCB fabricator’s front-end engineering capacity is utilized to perform pre-design release DFM reviews, but to no avail; they still show up with issues. This capacity could be used to release new revenue instead.
There have been many good articles written and presented on how to improve this. I would like to move the responsibility up in the food chain. What will it take to create this cultural change? Let’s take at a 30,000-foot view of key design package error categories (Figure 2).
Figure 2: Error categories.
Design and Documentation Errors
- Missing documents: A fabrication print is not provided with notes and stackup, and a required netlist and/or referenced specifications are not provided.
- Conflicting documentation: Gerber data has a hole, and the fab print has a slot at the same location; provided and extracted netlists don’t match; both an ODB++ file and a Gerber file are provided, but they don’t match.
- Un-corrected design issues: Legend on pad, dangling traces, and intentional netlist shorts are not identified.
- New revisions don’t fix approved changes noted in the down revision.
- Stackup is provided with impedance constraints that can’t be built (law-of-physics problem).
- Assembly documentation added after the data package is released.
Non-conformance to Fabricator Capability
- Fabricators only provide basic capability rules because they are considered proprietary, but the DFM or TQ process will eventually provide the “proprietary” rules for resolution.
- Designers perform DFM checks after the layout is complete, but it is too late to implement the required changes due to schedule/resource limitations.
- Material impedance dielectric constants (Dks) are different between the designer and fabricator; impedances are requested at frequencies that the fabricator can’t validate in production.
- Fabricators will fix issues without notifying the designer, so the designer is surprised when a second source identifies the issue because the initial fabricator “didn’t have that problem.”
- Fabricator design rules can’t be automatically loaded into the layout software before starting the layout, so they don’t get used.
Complex Supply Chain
- The designer may not know who the fabricator(s) will be before layout because the CM or procurement team selects the supplier based on price and/or lead-time requirements after the design is complete.
- The CM array drawing is not provided during the initial fabrication quote; an assumption is made for quoting, which differs from the production data package.
- The volume fabricator is not selected until after the design has been built by a different prototype supplier who uses different rules.
- Multiple sources are not selected until after the design has been fully characterized, released, and certified.
Can this new goal be achieved? The answer is, “Yes.” I have worked for global fabricators who closely collaborated with their customers to create “zero TQ” designs consistently. This won’t happen overnight, but we need to change our collective behavior and start putting new methods in place to get there.
Proposed Cultural Changes
- Fabricators provide complete capability rules to the designer.
- Layout software automatically loads fabricator rules directly into the software before layout starts.
- Layout software and processes resolve all documentation and design issues before release.
- Procurement lets the designer know who the sources could be before layout.
In a Factory 4.0 world, let’s create this paradigm shift to provide design files to a fabricator without errors, every time.
Dana is the principal consultant at Korf Consultancy LLC.
More Columns from Dana on Data
Dana on Data: Best Practices in Interpreting Drawing Notes—‘Use Latest Revision’Dana on Data: The Missing AI-NPI Link
Dana on Data: Merging 2D Electrical, 3D Mechanical Worlds
Dana on Data: Resurrecting IPC Class 1
Dana on Data: The Evolution of Fabrication Drawing
Dana on Data: The Insane PCB DFM Process
Dana on Data: eCAD PCB Design Deficiencies
Dana on Data: Nuke the Netlist