-
- News
- Books
Featured Books
- design007 Magazine
Latest Issues
Current IssueShowing Some Constraint
A strong design constraint strategy carefully balances a wide range of electrical and manufacturing trade-offs. This month, we explore the key requirements, common challenges, and best practices behind building an effective constraint strategy.
All About That Route
Most designers favor manual routing, but today's interactive autorouters may be changing designers' minds by allowing users more direct control. In this issue, our expert contributors discuss a variety of manual and autorouting strategies.
Creating the Ideal Data Package
Why is it so difficult to create the ideal data package? Many of these simple errors can be alleviated by paying attention to detail—and knowing what issues to look out for. So, this month, our experts weigh in on the best practices for creating the ideal design data package for your design.
- Articles
- Columns
- Links
- Media kit
||| MENU - design007 Magazine
Estimated reading time: 4 minutes
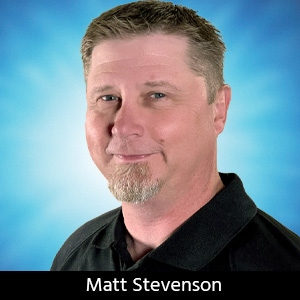
Connect the Dots: Build Quality Into Your Boards and Processes
To the procurement clerk, a PCB may seem like it is just a line item on a bill of materials (BOM) or parts list during the production of an electronic device. At Sunstone, we know differently. The PCB is the building block for all of the components and parts in your electrical project.
Boards are more than the sum of their parts—the epoxy, glass, copper, polymers, and holes are not the board. The board is the custom-made end product for a designer, layout engineer, entrepreneur, or team who has taken hours, days, or even weeks of time crafting the perfect PCB design. If the design turns out to not be perfect or the manufacturer doesn’t produce quality boards, delay and cost over-runs are the result. In the worst-case scenario, the boards don’t function properly, and nobody needs that many PCB coasters!
Committing to quality and best practices at the outset will help you limit the potential for design errors or manufacturing problems during your PCB project. More than lip service, quality management should be integral to your process. Choosing reputable PCB manufacturers at the beginning of each design phase is critical and a great first step towards a high-quality outcome.
It is unlikely that one manufacturer will fit all of your PCB needs. We each have our sweet spots with respect to each type of manufacturing project. By performing due diligence with your manufacturers and designing to their individual sweet spots, you position yourself for effective collaboration on those cutting edge or capability-taxing pieces. This can pay dividends in the overall manufacturability and re-liability of your project.
We don’t hide what we are good at. Most every PCB manufacturer goes to great lengths to promote their sweet spot, as well as maxi-mum and minimum capabilities, to the marketplace. This makes it easier for you to choose the right manufacturing partner for each board. Of primary concern at the outset is to confirm that the manufacturer accepts industry-standard file formats, specifically Gerber files and/or ODB++.
Accurate Gerber files are mission-critical for smooth PCB manufacturing. Converting to Gerber files can reveal design issues ahead of the quote process and ensure your manufac-turer has everything needed to produce your boards correctly and on time. Of course, what you put in those files will determine the final outcome, so perform design rule checks before you convert. Just because your soft-ware will let you design a board in a certain way doesn’t make it easily man-ufacturable. Keep manufacturability at the forefront as you set up and perform your design rule check before converting to Gerber.
By confirming the number of board layers, proper spacing, drill hole to size and placement aspect ratio, spacing, and proper tolerances, you can be assured you are indeed de-signing a board that can be built by your manufacturer without delays or errors. Some manufacturers even offer a set of DRC settings that can be added directly to your software, saving you the time and effort to create these rules. By taking these into consideration early in the process, you are building the quality right into your PCB.
Assuming your manufacturers are prioritizing quality and you are producing files that are compatible with their process, look for other production elements that are important to you. Does the manufacturer have the capacity and capability to build your board as designed? Without the right technology, equipment, process, and key personnel, you might not get a quality product, and you might not get it delivered on time.
Quality PCBs require the best materials. Manufacturers sourcing cheaply not only produce a mediocre product but they can also leave you in a lurch with respect to safety. Make sure your manufacturing partner can de-liver a UL-marked board that confirms its safe operability.
The UL mark tells you that the boards have been carefully monitored and will withstand thermal stress without failure, within reasonable limits. UL certification will give you confidence that your boards can with-stand temperatures required for soldering, as well as some rework, without delamination or decomposition. You can also be sure your PCBs will not catch fire under reasonable, and sometimes even unreasonable, operating conditions. This is an important safety concern if your boards will be used in a commercial product.
Since no two projects or boards are exactly alike, you will need different levels of support for each. Look for partners with multiple service levels. Sometimes, you just need a quick turn for proof of concept or a fast prototype run to keep an established manufacturing pro-cess moving along. In other cases, like new product development, more collaboration can help you get the job done right the first time.
More Columns from Connect the Dots
Connect the Dots: Sequential Lamination in HDI PCB ManufacturingConnect the Dots: The Future of PCB Design and Manufacturing
Connect the Dots: Proactive Controlled Impedance
Connect the Dots: Involving Manufacturers Earlier Prevents Downstream Issues
Connect the Dots: Stop Killing Your Yield—The Hidden Cost of Design Oversights
Connect the Dots: Designing for Reality—Routing, Final Fab, and QC
Connect the Dots: Designing for Reality—Surface Finish
Connect the Dots: Designing for Reality—Solder Mask and Legend