-
-
News
News Highlights
- Books
Featured Books
- smt007 Magazine
Latest Issues
Current IssueSpotlight on India
We invite you on a virtual tour of India’s thriving ecosystem, guided by the Global Electronics Association’s India office staff, who share their insights into the region’s growth and opportunities.
Supply Chain Strategies
A successful brand is built on strong customer relationships—anchored by a well-orchestrated supply chain at its core. This month, we look at how managing your supply chain directly influences customer perception.
What's Your Sweet Spot?
Are you in a niche that’s growing or shrinking? Is it time to reassess and refocus? We spotlight companies thriving by redefining or reinforcing their niche. What are their insights?
- Articles
- Columns
- Links
- Media kit
||| MENU - smt007 Magazine
Estimated reading time: 5 minutes
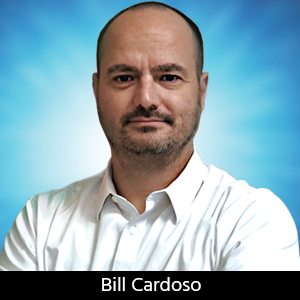
X-Rayted Files: Will Radiation Damage My Electronic Component?
Before I start talking about radiation damage on electronic components, let me warn you: if you are looking for a simple “yes” or “no” answer to the question, "Will radiation damage my electronic component?" stop reading now. Things will get complicated. You may feel like I did not answer the question at all, and you would be correct. There are whole conferences dedicated to this question (check IEEE’s Nuclear and Space Radiation Effects Conference), so the goal of this column is to give you some background to guide you to the right answer for your specific situation. Ultimately, the best way is to ask an expert. Some of the parameters we take into consideration when analyzing potential radiation damage to electronics include the type of radiation, time of exposure, radiation flux (which includes distance and power), and fabrication technology of the electronic component itself.
The reality is radiation is all around us, from concrete walls to cat litter to cosmic rays. To help you figure out this topic, let’s start breaking down what ionizing radiation is. There are two types of ionizing radiation: electromagnetic waves and subatomic particles. Electromagnetic waves are X-rays and gamma rays, while subatomic particles can be protons, neutrons, electrons, pions, muons, and others. You find subatomic particles at the place I used to work at—the Fermi National Accelerator Laboratory (Fermilab).
At Fermilab, we collided protons and antiprotons to create a soup of subparticles. We also looked for subparticles never seen before, so we had to design electronics to image the trajectory of these tiny objects. Needless to say, our electronics were subjected to an immense amount of radiation—the “bad” type of radiation for electronics, meaning particles. Waves are not as bad because they travel through components, but particles, on the other hand, like to “stop” inside of the component, thus depositing all its energy; this, in turn, causes lots of damages.
Since few people out there are using components inside particle accelerators, I will focus on X-ray inspection only. There are three different damage mechanisms: bulk damage, surface damage, and single event upset. Bulk damage is when the energy transferred to the silicon atom is sufficient to remove it from the crystal lattice. This damage is permanent. However, most X-ray inspection systems simply don’t have enough energy to cause this kind of damage. While X-ray systems used for electronic inspection range from the 80–160 kV, bulk damage can happen in the mega-volt range (1,000 times more power).
Meanwhile, surface damage is when the passage of ionizing radiation in the silicon oxide on semiconductors can cause a buildup of trapped charge in the oxide layers and potentially alter microcode or configware resident on certain devices, such as FPGAs and memory circuits. This can cause “bit flips” in digital circuits, or voltage spikes in analog circuits. This is permanent damage.
A single-event upset (SEU) is a change of state caused by one ionizing particle striking a sensitive node in a microelectronic device, such as in a microprocessor, semiconductor memory, or power transistors. This damage mechanism is dynamic, as it happens when the device is powered up and operating. This is not permanent damage and can be corrected by rewriting the memory bit that was flipped, for example.
Since you want to know if your X-ray machine will damage the component you are inspecting (most likely, someone else is asking you that), it is unlikely the low power X-ray system in your lab can cause bulk damage to the part. You will not be operating the component during an inspection, so SEU is also not an issue. That leaves us with surface damage. Let’s see what we can do to minimize the chances of this damage mechanism.
Going back to the beginning of this column, radiation damage depends on radiation type (X-rays), energy (low, in the 80–160 kV range), radiation flux, and exposure time. We cannot change the radiation type or energy, but we can minimize the radiation flux and exposure time. So, to reduce the radiation flux, move the sample as far as possible from the source. The image will get darker, and you’ll have less magnification, but instead of cranking up the power, you want to change the settings in the sensor to achieve a good image.
The exposure time can be minimized with automation. Instead of relying on an operator to look at the image to make a pass/fail judgment, use an algorithm, or even artificial intelligence (AI). We have designed several autonomous systems that use AI to replace operators. You also want to minimize radiation to all those components around the field of view that are receiving radiation for no reason. All it takes is the design of a shield that will protect components not under inspection.
Once you have done all you can to minimize the number of X-ray photons going through your electronic component, it is time to figure out how much radiation you are exposing it to. That can be calculated using the kV and mA of the source, distance between the source and the sample, and the time of exposure. You will also need to know the fabrication technology of the component. A 0.8-µm HP and 0.25-µm TSMC semiconductor fabrication processes have different susceptibilities to radiation. There are also big differences between a GaAs and Si semiconductor.
Likely, a component you are inspecting in the X-ray machine in your lab has already been irradiated by much more powerful X-ray machines. From the time the component exits the manufacturer, the part will be X-rayed by the screening equipment at airports, border crossings, and ports of entry and shipping warehouses. Some of these organizations use very powerful X-ray machines in the hundreds (and sometimes thousands) of kV. It’s always good to put things in perspective.
So, we come back to one simple question: Will radiation damage my electronic component? The best answer I can give you is that it depends.
Dr. Bill Cardoso is CEO of Creative Electron.
More Columns from X-Rayted Files
X-Rayted Files: Best Practices in Buying MachinesX-Rayted Files: ’23 and Me?
X-Rayted Files: Battery-Powered Advancements Keep on Ticking
X-Rayted Files: What’s Cooler Than X-ray?
X-Rayted Files: My Favorite BGA Assembly Ever, Part 3
X-Rayted Files: My Favorite BGA Assembly Ever, Part 2
X-Rayted Files: My Favorite BGA Assembly Ever
X-Rayted Files: Smart vs. Intelligent SMT Factory