-
- News
- Books
Featured Books
- design007 Magazine
Latest Issues
Current IssueShowing Some Constraint
A strong design constraint strategy carefully balances a wide range of electrical and manufacturing trade-offs. This month, we explore the key requirements, common challenges, and best practices behind building an effective constraint strategy.
All About That Route
Most designers favor manual routing, but today's interactive autorouters may be changing designers' minds by allowing users more direct control. In this issue, our expert contributors discuss a variety of manual and autorouting strategies.
Creating the Ideal Data Package
Why is it so difficult to create the ideal data package? Many of these simple errors can be alleviated by paying attention to detail—and knowing what issues to look out for. So, this month, our experts weigh in on the best practices for creating the ideal design data package for your design.
- Articles
- Columns
- Links
- Media kit
||| MENU - design007 Magazine
Residual/Free TBBPA in FR-4
January 31, 2020 | Sergei Levchik, ICL-IP AmericaEstimated reading time: 4 minutes
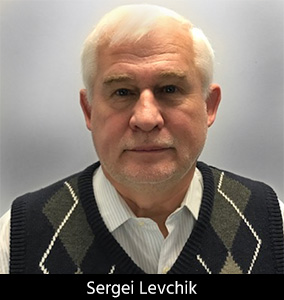
FR-4 laminates and prepregs are important fiberglass epoxy materials for printed circuit boards (PCBs). FR-4 base materials are the most popular grade used today because they offer a cost-effective and versatile solution for electrical engineers and product designers. The FR-4 designation was created by NEMA in 1968 and denotes the laminate is flame-retarded to meet a UL94 V-0 fire rating.
Trade associations such as IEC, IPC, and JEDEC have separated FR-4 into two distinct categories based on the flame-retardant mechanism—one using brominated chemistries and the other being comprised of flame retardants, such as phosphorus, nitrogen, and synergistic fillers. FR-4 base materials using bromine as the flame-retardant mechanism are made, so the bromine-containing molecules are chemically bonded in the epoxy resin polymer. Tetra-bromobisphenol-A (TBBPA) is an important and widely used flame retardant for FR-4 base materials. Difunctional epoxy resin is reacted with TBBPA to produce oligomers of epoxy resins (Figure 1). Once cured, there is no opportunity for TBBPA to leach out.
Figure 1: Reaction of TBBPA to form epoxy polymers.
In recent years, market and regulatory interest have grown regarding potential exposure to flame retardants found in consumer and industrial goods. This has come with greater expectations that manufacturers can estimate exposures over the life cycle of their product. In some jurisdictions, there are also regulatory reporting considerations (e.g., California Prop 65) that demand a higher level of manufacturing understanding of their goods. Product designers have long presumed TBBPA is fully reacted in laminates to optimize costs and material performance and do not generally report on TBBPA levels. However, there has been little public data documenting this or defining potential “free TBBPA” within the epoxy polymer.
Testing
Laminate samples were obtained from TUC (Taiwan), Shengyi Technology (China), and Ventec (China)—all major suppliers to the electronics supply chain. The laminates tested were selected to cover both ends of the glass transition temperature (Tg) range for FR-4 products used from 140°C to over 170°C. In addition, non-brominated FR-4 laminates were tested as controls.
Laminate samples were prepared for analysis according to EPA Method 3545A (Pressurized Fluid Extraction). Method 3545 is a procedure for extracting water-insoluble or slightly water-soluble organic compounds from soils, clays, sediments, sludges, and waste solids. The method uses elevated temperature (100–180°C) and pressure (1,500–2,000 psi) and is applicable to the extraction of semi-volatile organic compounds, organophosphorus pesticides, organochlorine pesticides, chlorinated herbicides, PCBs, and PCDDs/PCDFs, which may then be analyzed by a variety of chromatographic procedures. Prepared samples were analyzed for TBBPA by EPA Method 8321B, which covers the use of high-performance liquid chromatography (HPLC), coupled with both thermospray-mass spectrometry (TS-MS) and an ultraviolet (UV) detector, for the determination of a variety of solvent-extractable nonvolatile compounds.
Before analyzing FR-4 laminate samples from the three manufacturers, the test method was independently validated with respect to TBBPA detection and quantification. Two control samples of reportedly TBBPA-free epoxy resins were obtained. One gram of each board material was ground and extracted by sonication in toluene for 90 minutes at 27°C (as described in above EPA methods) to make sample solutions. Sonication equipment was set to maximum power to ensure an aggressive extraction of any background TBBPA. Sample solutions from this process were retained and fortified with pure TBBPA at three recovery levels: 2, 4, and 10 ppm.
Results
Control and fortified samples were analyzed for TBBPA in duplicate, and the data, are shown in Table 1. The TBBPA concentration in control samples was below the 1 ppm limit of detection. TBBPA recovery in fortified sample solutions was very consistent and repeatable across all samples and, on average, was greater than 80%. There was some slight decline in percent recovery with increasing TBBPA fortification. However, in all cases, percent recoveries were well above the 70% limit of acceptability for such methods and excellent confirmation of the methods for analyzing epoxy boards.
Table 1: Fortified sample method results.
Commercially produced FR-4 laminate results are shown in Table 2. The data show all the TBBPA FR-4s had less than 1 ppm (< LOD) of “free TBBPA” demonstrating essentially complete reaction of TBBPA with the epoxy. Non-brominated samples (6, 7, 8, 9) showed the same, demonstrating the methodology consistency. The results demonstrate that the full conversion of TBBPA is independent of the glass transition temperature (Tg) of the final product and show the robustness of these production processes with respect to TBBPA conversion. Tests 10 and 11 were high-performance laminates for high-speed/high-frequency applications (not FR-4), where TBBPA-based epoxy resin was a modifying polymer in the system.
Table 2: Free-TBBPA test results.
Conclusion
In summary, it is clear FR-4 products in the market today, comprised of reacted-in brominated chemistries, do not contain “free TBBPA” after curing. As such, these products demonstrate how reactive brominated flame retardants can be used effectively to enhance the fire safety of product designs. This information will be provided to the IPC (Association Connecting Electronics Industries) for inclusion in their next revision of IPC-WP/TR-584: “IPC White Paper and Technical Report on the Use of Halogenated Flame Retardants in Printed Circuit Boards and Assemblies.”
In addition, the information will be supplied to the IEC (International Electrotechnical Commission, Geneva, Switzerland) for consideration in their standardization activities. If any manufacturers of FR-4 would like to have data on their products included in the future reports, there is still time to have FR-4 products analyzed. Please email me at Sergei.Levchic@ICL-Group.com for the contact information of the test laboratory.
I would also like to thank the analytical laboratory Applied Technical Services in Atlanta, Georgia.
Sergei Levchik is R&D director at ICL Group.
Suggested Items
Seeing a Future in Mexico
07/09/2025 | Michelle Te, I-Connect007The Global Electronics Association (formerly known as IPC) has been instrumental in fostering a partnership with Guanajuato, a state north of Mexico City with 12 industrial clusters and close to 150 companies involved in electronics. This past spring, Alejandro Hernández, the undersecretary for investment promotion in Guanajuato, attended IPC APEX EXPO 2025 at the invitation of IPC Mexico Director Lorena Villanueva, where he met with several companies to discuss the opportunities available in Mexico. He is inviting electronics-related companies seeking long-term investment in a centrally located area with access to highways, railways, and ports.
The Global Electronics Association Releases IPC-8911: First-Ever Conductive Yarn Standard for E-Textile Application
07/02/2025 | Global Electronics AssociationThe Global Electronics Association announces the release of IPC-8911, Requirements for Conductive Yarns for E-Textiles Applications. This first-of-its-kind global standard establishes a clear framework for classifying, designating, and qualifying conductive yarns—helping to address longstanding challenges in supply chain communication, product testing, and material selection within the growing e-textiles industry.
IPC-CFX, 2.0: How to Use the QPL Effectively
07/02/2025 | Chris Jorgensen, Global Electronics AssociationIn part one of this series, we discussed the new features in CFX Version 2.0 and their implications for improved inter-machine communication. But what about bringing this new functionality to the shop floor? The IPC-CFX-2591 QPL is a powerful technical resource for manufacturers seeking CFX-enabled equipment. The Qualified Product List (QPL) helps streamline equipment selection by listing models verified for CFX compliance through a robust third-party virtual qualification process.
The Knowledge Base: A Conference for Cleaning and Coating of Mission-critical Electronics
07/08/2025 | Mike Konrad -- Column: The Knowledge BaseIn electronics manufacturing, there’s a dangerous misconception that cleaning and coating are standalone options, that they operate in different lanes, and that one can compensate for the other. Let’s clear that up now. Cleaning and conformal coating are not separate decisions. They are two chapters in the same story—the story of reliability.
Advancing Aerospace Excellence: Emerald’s Medford Team Earns Space Addendum Certification
06/30/2025 | Emerald TechnologiesWe’re thrilled to announce a major achievement from our Medford, Oregon facility. Andy Abrigo has officially earned her credentials as a Certified IPC Trainer (CIT) under the IPC J-STD-001 Space Addendum, the leading industry standard for space and military-grade electronics manufacturing.