-
- News
- Books
Featured Books
- design007 Magazine
Latest Issues
Current IssueProper Floor Planning
Floor planning decisions can make or break performance, manufacturability, and timelines. This month’s contributors weigh in with their best practices for proper floor planning and specific strategies to get it right.
Showing Some Constraint
A strong design constraint strategy carefully balances a wide range of electrical and manufacturing trade-offs. This month, we explore the key requirements, common challenges, and best practices behind building an effective constraint strategy.
All About That Route
Most designers favor manual routing, but today's interactive autorouters may be changing designers' minds by allowing users more direct control. In this issue, our expert contributors discuss a variety of manual and autorouting strategies.
- Articles
- Columns
- Links
- Media kit
||| MENU - design007 Magazine
Estimated reading time: 7 minutes
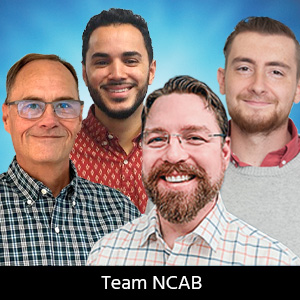
Fresh PCB Concepts: Controlled Impedance—Design to Testing
I often get questions from customers on one of my favorite subjects in PCB design: controlled impedance. Controlled impedance is a science, which is why I like it; therefore, it must be designed and tested comprehensively. But before I get into that, what is controlled impedance?
Probably the most common example of a controlled impedance component is the down lead or cable connecting a receiving antenna/aerial to a television set. Aerial cable leads usually take the form of low-loss coaxial cable, which consists of a round, inner conductor separated from the outer cylindrical conductor (the shield) by an insulator. The dimensions of the conductor and insulator, and the electrical characteristics of the insulator, are carefully controlled to achieve the requested impedance. Such cables may also be a "flat twin" cable (commonly supplied with VHF broadcast receivers). In both cases, the impedance of the feeder is controlled by the physical dimensions and material of the cable.
At high frequencies, PCB traces do not behave like simple connections, so we need to take special care with the PCB design because the signals will degrade as the traces route around the PCB. Theory shows that maximum signal power is transferred when impedances are matched. If the impedances do not match each other in the transmitter, trace, and receiver, the signal cannot flow properly and will be distorted.
Consider this example of a powerful light and a mirror. The powerful light is the transmitter, and the hole in the wall of the mirror could be considered the trace. We can see that the hole is smaller than the lens of the light (Figure 1).
When we turn on the powerful light and try to shine through the smaller hole in the mirror, then there will be a considerable reflection, and the amount of light that passes through the hole in the mirror will be a lot less (Figure 2).
There will be the same effect if the trace on the PCB does not have the same impedance matching as the transmitter and receiver. Then, a part of the signal will bounce back along the trace creating a standing wave that will distort the signal.
Trends Toward Higher Speed
The demand for speed is a major driver in the need for impedance control. All new applications need to be faster, smaller, and more accurate. Since the PCB normally is a vital part of the design, the traces on the board need to be controlled. Historically, only exotic, high-speed devices required controlled impedance PCBs. These amounted to perhaps 10–20% of PCBs manufactured. Now, around 90–95% of all multilayer PCBs are manufactured with controlled impedance traces.
Specific product types that previously were the main drivers for impedance:
- Telecommunications
- Video signal processing
- High-speed digital processing
- Real-time graphics processing
- Process control
Even consumer products need impedance control to work. Examples of applications include:
- Routers
- GPS devices
- Smartphones
- Digital cameras and digital video cameras
- Blu-ray players
- Personal computers and tablets
- Auto engine control modules
When Is Control Needed?
When do I need to use impedance controlled traces? It depends on how sensitive the application is. How much distortion can be accepted/lived with?
The length of a track is also critical. A very long track in a backplane, for example, needs to be controlled from 100-MHz frequency or even lower. But a shorter track can, in some case, be left without impedance control even if the frequencies are much higher. Signal traces longer than critical length (1/16 wavelength in DK) need impedance control to prevent return loss due to reflections. Shorter circuit elements don’t require impedance control, but it usually does no harm.
Good Design Practices
Once using broadside-coupled impedance, it is always recommended to use a core layer in the middle instead of having two cores facing each other because it is much easier to control the tracks that are placed correctly on the core layer than between two different cores. Position problems between two cores can easily be up 150 µm or more, and that can affect impedance value with 5–10 ohms (Figure 3).
Take into consideration the manufacturing tolerances that are applicable in the PCB industry. For example, one parameter is the etch factor. As shown in Figure 4 on the left side, an etch factor of only 25 µm can affect the impedance only a few ohms on a wide track; on the other hand, it can affect the result with up to 10 ohms on a 4-mil track. One good design practice is to use as wide a track as possible when it needs to be controlled (Figure 4).
It is the same concern with dielectric tolerance, which needs to follow all applicable PCB industry manufacturing tolerances. As shown in Figure 5 on the left side, a difference in the dielectric separation factor of only 25 µm can affect the impedance only a few ohms on a wide separation; on the other hand, it can affect the result with up more the 20% on a narrow separation (Figure 5).
Some structures are also more sensitive to variations in dielectric separation, like the offset stripline. As shown in Figure 6 on the left side, a difference in the dielectric separation factor of only 25 µm will have virtually no effect on the impedance of a wide separation and a centered track; on the other hand, it can affect the result up to 20% if the track is too close to one of the planes. A good design practice is to use a dielectric separation as big as possible and try to have a centered and controlled track between the planes (Figure 6).
Always leave at least one separation outside the impedance controlled area. This leaves room for your PCB supplier to adjust the build-up slightly and still be able to achieve the overall thickness.
It is a good design practice to always use a unique aperture width for the tracks that need to be controlled. The track width should only be used for the critical tracks and not be used for other less critical tracks. This provides more room for adjustment.
Here are the information and specifications we need to make the board:
- Impedance values and tolerance
- Type of structure
- Identify the layers where the structure is placed on
- Reference layer(s) used for each structure
- Track width (separation) of the structure.
- Build with dielectric spacing/copper weights
Support During the Design Phase
At NCAB Group, we use a sophisticated tool from Polar Instruments that allows us to generate customer build-ups and implement impedance tracks inside the stack and calculate these tracks. This tool also contains a full library of materials, such as cores and prepregs, copper foil, and material libraries from several globally recognized material vendors can be download and imported in the system.
With this powerful tool, we can generate our stackup report with all the calculations inside. These reports can be used by the customer with either a new design or to verify already existing designs. We recommend to be flexible with your material requirements, but it is important to make sure your supplier is held accountable by requiring them to submit impedance calculations and stackup for approval before production. This will demonstrate that the boards will be acceptable.
Testing
Due to many practical reasons, the testing is not normally performed on the PCB but on a test coupon manufactured at the same time and on the same panel as the PCB. Procurement indicates the level of verification; otherwise, factories normally use some AQL level to test. The test coupon is a miniature circuit boards, representing the actual boards, with the same impedance structure, all impedance controlled tracks, the same plane layers, and the same dielectric separation as on the PCB.
Here are the benefits of using a test coupon:
- Dielectric builds will replicate the impedance structure on printed boards
- Test connection holes shall be plated through to access all inner layer test conductors
- Square pads identify plated through-hole connections to access all ground/power reference planes
- Conductor widths will replicate critical conductors on each impedance layer
- 150-mm straight line is created for correct testing
- All planes to be interconnected on coupon
- Allows fast testing with standardized probes
To test or verify the calculated result, a time-domain reflectometer (TDR) is used. Whenever there is a change in impedance value (discontinuity), part of the signal power is reflected back to the TDR instrument, which is capable of measuring this reflected signal. The time delay between the transmitted pulse and the receipt of the reflected signal is proportional to the distance of the discontinuity. The magnitude of the reflected signal is related to the value of the discontinuity. From this data, a graph is plotted. TDR is a highly complex/sophisticated laboratory instrument that applies a very fast electrical step signal to the coupon via a controlled impedance cable.
Ultimately, these factors are what I love about helping customers with controlled impedance. There is no room for error, and I get excited once I’ve helped in the design phase, with reporting and testing, and, eventually, when the end product works as intended. I could keep going because I have much more useful information on additional terminology, common structures, material recommendations, and more, but let’s save those for another column.
Ruben Contreras is a field application engineer at NCAB Group.
More Columns from Fresh PCB Concepts
Fresh PCB Concepts: More Than Compliance—A Human-centered Sustainability ApproachFresh PCB Concepts: Assembly Challenges with Micro Components and Standard Solder Mask Practices
Fresh PCB Concepts: The Power of a Lunch & Learn for PCB Professionals
Fresh PCB Concepts: Key Considerations for Reliability, Performance, and Compliance in PCBs
Fresh PCB Concepts: Traceability in PCB Design
Fresh PCB Concepts: Tariffs and the Importance of a Diverse Supply Chain
Fresh PCB Concepts: PCB Stackup Strategies—Minimizing Crosstalk and EMI for Signal Integrity
Fresh PCB Concepts: PCB Plating Process Overview