-
- News
- Books
Featured Books
- design007 Magazine
Latest Issues
Current IssueAdvanced Packaging and Stackup Design
This month, our expert contributors discuss the impact of advanced packaging on stackup design—from SI and DFM challenges through the variety of material tradeoffs that designers must contend with in HDI and UHDI.
Rules of Thumb
This month, we delve into rules of thumb—which ones work, which ones should be avoided. Rules of thumb are everywhere, but there may be hundreds of rules of thumb for PCB design. How do we separate the wheat from the chaff, so to speak?
Partial HDI
Our expert contributors provide a complete, detailed view of partial HDI this month. Most experienced PCB designers can start using this approach right away, but you need to know these tips, tricks and techniques first.
- Articles
- Columns
Search Console
- Links
- Media kit
||| MENU - design007 Magazine
Estimated reading time: 4 minutes
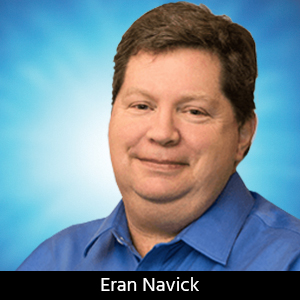
Global Technology: The Importance of Fine Lines
As the electronics “must-have” product invasion is finding its way into all parts of our lives, we are bombarded by advertisements for smaller cellphones and electronic products that do more and more. There are now electronics in every item we own, from powerhouse fuse boxes that can be turned on and off to measure the power used in your house and your cellphone advancing to a completely interconnected house. The one thing they all require is smaller and smaller electronic devices and printed circuits to put in these devices.
As we make circuits smaller and smaller, finer lines and spaces and more layers will be needed. Many PCB manufacturers are now at 25 microns line widths and spaces, and some are well below that. Fabricators are making the vias smaller and the laminate thinner. These smaller microcircuits are required to satisfy the world’s thirst for everything in their life to be smart or connected. For example, the following exchange may become a regular occurrence:
- “Alexa, I need a beer.”
- “Yes, I will send the robot servant right over. Would you like chips with your beer?”
- “Yes, please.”
- “Thanks, Alexa.”
Or your fridge will read barcodes and keep track of the expiration dates and stock in the fridge and reorder more, which will be delivered right to your house. Cameras will watch the delivery person load up your fridge. Someday soon, everything you own or touch will have smart AI-driven microelectronics controlling the device. I recently had experience with the microcomputer Raspberry PI; at one inch by two inches, it could do everything my big laptop could do. It had more computing power than my first 20 computers combined. However, with the explosion of internet connections into our private lives comes the danger of hacking and identity theft. I believe we will solve that with AI. As the hacker is trying to break into your house cameras, AI will know it is not you and shut them out. This all takes a large number of microminiature electronics and very tiny, complicated circuit boards.
The computer invasion is also happening in the printed circuit business itself; more lasers are being used in printed circuit shops, which started first with the cutting of flex and then progressed to drilling. We have computer-driven smart lasers doing fine line imaging and using AI to figure out the tough multilayer scaling and impedance calculations. The manufacturers have added laser optical scanning for quality control to find opens and a high-powered laser to cut away a short from the etcher. Computer-driven, laser-aligned electrical testing allows for processing very fine lines and vias, which was impossible a few years ago. High-accuracy intelligent optics and lasers are mandatory now for processing HDI, fine-line circuits.
Micro miniaturization is invading our life, and everything is getting smaller. Even your hearing aid now is equipped with Wi-Fi Bluetooth to talk to your phone, so you can adjust the settings on the go.
3D printed electronics is another trend to watch. Soon, we will be printing pure copper onto low-temperature parts, utilizing nanocopper formulated to melt using a laser at a low temperature. A laser scans the part covered with copper powder. During each pass, more copper powder is spread over the laminate, and after a half dozen passes, you have real copper traces. A liquid epoxy is ink-jetted in and laser cured, where required. Developing spray removes the excess liquid solder mask. Even through-holes in multilayer will be possible by lasering copper up the hole on each pass.
An exciting new area is the malleable aluminum heat sink with thermal material laminated for use in LED applications, such as your car’s fancy headlights and dash and rear light lamination. This market is growing quickly, with more heat spreading laminates being introduced.
Heavy copper printed circuits were once rare and difficult to get manufactured. Now, many shops are processing increasingly thicker circuits as the demand for higher currents increases. Some manufacturers are doing three-dimensional boards with 1-oz circuitry for the SMT soldering of small parts and chips and then an interconnected circuitry of 5-oz for driver circuits, which powers a 15-oz section for the main, high power IGCT outputs to drive your electric car motor or your home from solar panels.
High-voltage circuits are becoming more common, too. Manufacturers are using a layer of Kapton as the insulators within the circuit isolating layers voltages. With ratings of up to 20,000 volts, they can be designed and manufactured for applications directly to the grid.
Tactile feedback circuits are also utilizing pressure-sensitive circuits to sense the amount of pressure the robot is applying with its hands. The feedback circuits are being used in car displays to control the electronics in the car as they sense your finger’s pressure. These pressure-sensitive devices are being intergraded right into the flex circuits.
Microbiological circuits for medical applications are using chemical additives plated or added to the circuit to sense various chemicals used for blood analyses, checking for diabetic readings, heart ECG, and other important boldly functions. All can be done automatically and reported quickly back to the doctor’s office.
The next few years will be exciting, as we watch how the PCB will be adapted and advanced to keep up with the demand for more smaller electronics in our everyday products. We seem to have a desire to have everything we own be automatic, smart, and interconnected. That’s why lines are only going to get finer and PCBs denser.
Eran Navick is CEO of FineLine USA.
More Columns from Global Technology
Global Technology: The Importance of Laminate CTE in PCB DesignGlobal Technology: Assembling High-current, Heavy Copper PCBs