-
- News
- Books
Featured Books
- smt007 Magazine
Latest Issues
Current IssueSupply Chain Strategies
A successful brand is built on strong customer relationships—anchored by a well-orchestrated supply chain at its core. This month, we look at how managing your supply chain directly influences customer perception.
What's Your Sweet Spot?
Are you in a niche that’s growing or shrinking? Is it time to reassess and refocus? We spotlight companies thriving by redefining or reinforcing their niche. What are their insights?
Moving Forward With Confidence
In this issue, we focus on sales and quoting, workforce training, new IPC leadership in the U.S. and Canada, the effects of tariffs, CFX standards, and much more—all designed to provide perspective as you move through the cloud bank of today's shifting economic market.
- Articles
- Columns
- Links
- Media kit
||| MENU - smt007 Magazine
Estimated reading time: 5 minutes
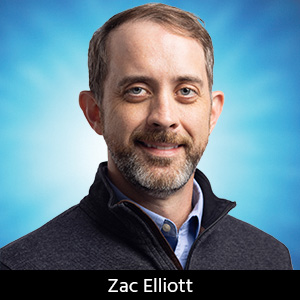
Lean Digital Thread: Realizing ROI Starts With Making Smart Data
Sometimes, you think too much about the bits and bytes, and you forget why you started this journey; we’re all caught up in a tornado of marketing buzzwords. To be honest, a tiny fraction of this tornado was generated by me. In my column, I plan to keep away from high-level discussions and overused buzzwords and instead focus on the fundamentals. My idea is to use this space as a “sandbox” for brainstorming and business process thinking (yes, you are most welcome to send me questions, ideas, and dreams for analysis and discussion).
I would like to start with the basics. Lord Kelvin once said, “When you can measure what you are speaking about, and express it in numbers, you know something about it.” Further, Merriam-Webster Dictionary defines digitalization as, “The process of converting something to digital form.” This sounds simple, but it’s not.
If you combine the two (numbers and digitalization), you must start with digital data—smart numbers. Smart data means a constant flow of normalized information—volume, velocity, variety, value, and validity—that can be used and shared for understanding processes (Figure 1).
Smart factory implementations must start with traditional process analysis and improvement. Focusing on data collection should be the first step to be able to efficiently monitor and analyze. In my experience, executives and operators are often fully committed to going digital in every aspect of manufacturing. Many already started the digitalization journey (I don’t think we can simply call it a project). However, there’s still a misconception about the return on investment. Approximately half of the executives believe digitalization will not increase their profits. I assume that it also depends on the motivation; sometimes, management is willing to invest only if customers require it.
There are many reasons to digitalize, including the potential for financial ROI, lower labor costs, higher yields, and added capacity motivates the senior management. The marketing tornado I previously mentioned is making it hard to decide on when, where, and how to do it. Some are worried that every slight change will result in staff cuts or even threaten the midlevel manager’s position, in addition to change and the learning curve to adopt new technologies. I would assume that most factories still have a lot of room for improvement without replacing employees with collaborative robots or “cobots.”
It’s Not Just About the Technology
Having worked with various customers from the smallest to the largest corporations with 300–400 lines globally dispersed, “IoT” is a buzzword in all the Industry 4.0 areas, whether it’s in the process industry or the electronics industry. Everyone is talking about industrial IoT (IIoT) and its importance from obvious reasons I mentioned earlier; we must have smart data to begin. In some cases, manufacturers acknowledge this but choose to develop their own data acquisition platform. In my opinion, these business leaders are looking in the wrong direction.
While these individuals are domain experts with valuable IT knowledge, their capabilities should not be invested in building an IoT platform. Today, it would be much easier to get a data acquisition platform out-of-the-box; their resources should be invested in leveraging the data to describe, analyze, and improve the process and material handling. Simple analysis can identify bottlenecks in production, and this insight can translate to action—how to improve yield and profitability. This is where I think IT needs to focus their expertise on—leveraging the knowledge to drive excellence in manufacturing with less focus on the technology, which is not the real target of this digitalization journey.
It’s Not Just About Collecting Data; It’s About Making the Data Smart
Industry 4.0 is not just about connecting another machine and collecting the data. It’s really about the mindset of understanding how problems can be solved, looking at improving, and moving toward excellence. You can buy a digital solution out-of-the-box from most companies in this area and focus on how to leverage the knowledge with the data and the software solutions implemented to improve the business.
Many customers are looking at overall equipment efficiency (OEE) or overall line efficiency (OLE) only from the placement point of view, not the overall line; the bottleneck can be in the oven. They also do not consider that changeover is actually a plant stop. I would like to share a simple example that shows the importance of data.
Table 1: An example showing the importance of data.
Let’s say that in a given week, we have 10,080 minutes, and we need to run maintenance, a few changeovers, inventory count, and shift changes—all planned stoppages (Table 1). Next, we have weekends and holidays. Thus, we already lost a chunk of the available production time. In this example, you can see there is no third shift (we need to reduce 2,400 minutes), so by design and plan, we can get 100% OEE, but in fact, not 100% utilization rate (CuR). Next, we have planned meetings—30 minutes of stopped production to discuss things. The planning factor is important. OEE/OLE is how well we succeeded from the full realistic potential.
Let’s proceed to the availability breakdown (Table 2). We have a line waiting upstream, such as if the printer had to wait for the pick-and-place machines. We also have a line waiting downstream, such as if the oven is waiting. From the total time, we “wasted” 76% on the planned factors, and out of the total availability, my performance was not good enough.
Table 2: Availability breakdown.
Table 3: The overall picture.
If the printer is really slowing down upstream, maybe we should take the SP+SPI offline. But to make a case and prove it, we need a baseline with which to compare. With such a simple step, we can increase the line performance by 10%, and we will never have soldering issues on the line itself.
In this example, we can see the overall picture, including the real numbers factored into the OEE/OLE that is presented with the current utilization rate (CUR) and how efficiently we used my actual available production time (Table 3); one may notice that if we improve the change over time, the OEE/OLE can also go down if we don’t use the time properly.
To summarize, making the data smart means taking the aforementioned example and automating the process. Have this data continuously monitored and analyzed for better decision-making. Digitalization has to start by turning data into smart data.
Sagi Reuven is a business development manager for the electronics industry, Siemens Digital Industries. Sagi’s columns will offer PCBA manufacturers advice on Lean manufacturing with a focus on ROI and customers’ stories. Download your free copy of the book The Printed Circuit Assembler's Guide to… Advanced Manufacturing in the Digital Age from Mentor, a Siemens Business, and visit I-007eBooks.com for other free, educational titles.
More Columns from Lean Digital Thread
Lean Digital Thread: The Manufacturing Metaverse RevisitedLean Digital Thread: The Secure Digital Thread
Lean Digital Thread: The Manufacturing Metaverse
Lean Digital Thread: Closing the Loop on Manufacturing
Lean Digital Thread: Keeping an Eye on Quality
Lean Digital Thread: Streamlining the Internal Supply Chain
Lean Digital Thread: Achieving Supply Chain Resilience
Lean Digital Thread: (Pro)curing the Supply Chain Virus