-
- News
- Books
Featured Books
- design007 Magazine
Latest Issues
Current IssueProper Floor Planning
Floor planning decisions can make or break performance, manufacturability, and timelines. This month’s contributors weigh in with their best practices for proper floor planning and specific strategies to get it right.
Showing Some Constraint
A strong design constraint strategy carefully balances a wide range of electrical and manufacturing trade-offs. This month, we explore the key requirements, common challenges, and best practices behind building an effective constraint strategy.
All About That Route
Most designers favor manual routing, but today's interactive autorouters may be changing designers' minds by allowing users more direct control. In this issue, our expert contributors discuss a variety of manual and autorouting strategies.
- Articles
- Columns
- Links
- Media kit
||| MENU - design007 Magazine
Estimated reading time: 3 minutes
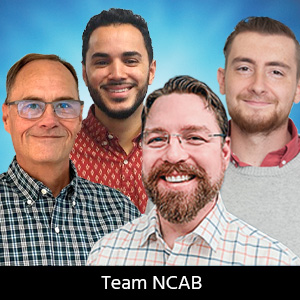
Fresh PCB Concepts: How Do You Calculate Finished Copper?
How do you calculate finished copper on a PCB? This may sound simple. But we have seen copper thickness called out either on the drawing or the specification, which can lead to additional engineering questions (EQs) and, in some cases, additional costs. These are unintentional results as a misunderstanding of what is requested—not in all cases, but some. Let’s start with some terminology.
Ounces relates to the weight of copper that covers one square foot (Figure 1). The area of the board itself cannot change; it’s fixed. But as the weight of copper increases, so does the thickness of the copper deposit. What does ½ ounce, 1 ounce, or 2 ounces really mean? There is a perception that ½ ounce equals 17 microns (0.669 mils), 1 ounce equals 35 microns (1.377 mils), and 2 ounces will give you 70 microns (2.756 mils). While that’s pretty close, it’s not strictly true.
Figure 1: A sheet of copper.
This brings us to IPC—specifically IPC-6012, which is the qualification and performance standard for rigid PCBs. Let’s start with the internal layer foil thickness (Table 1).
Table 1: Table 3-13 in IPC-6012. (Source: IPC)
If we consider 1 ounce, we can see that this actually equates to 34.3 microns, (1.350 mils) as the target for the foil manufacturer. However, this also allows for a 10% tolerance on the produced foils, which means that a 1-ounce inner layer foil could be received at the PCB factory with a thickness of 30.9 microns (1.217 mils). From there, we also see that there is a 6-micron (0.236-mil) reduction allowed for the pretreatment of the copper foil during the process at the PCB factory before imaging and bonding. After processing, the minimum copper foil thickness for 1 ounce of copper foil may be 24.9 microns (0.980 mils), which is a little different than the 35 microns perceived.
Where we see the potential challenges is when we see the thickness for inner layers specified as 35 microns minimum. This means that to achieve the 35 microns (1.377 mils) as the foil thickness after processing, we would need to start with 2 ounces, which would provide 55.7 microns (2.193 mils).
Let’s now look at external or outer layers, where this becomes a little bit more complex. As the industry standard, IPC-6012 relates to base copper weights rather than finished copper (Table 2).
Table 2: Table 3-14 in IPC-6012. (Source: IPC)
IPC Table 3-14 shows us that the minimum surface conductive finish of the finished copper is equal to the absolute minimum copper foil thickness, plus an average copper plating thickness of 20 microns (0.787 mils) for Class 2, and 25 microns (0.984 mils) for Class 3, minus the maximum processing reduction allowance. Let’s see what happens when a customer calls for 1 ounce finished.
We know that IPC minimum for 1-ounce copper weight equates to 30.9 microns (1.217 mils). If we start with ½ ounce, 15.4 microns (0.606 mils), plus plating of 20 microns (0.787 mils) for Class 2 or 25 microns (0.984 mils) for Class 3, and then allow for process reduction of 2 microns (0.079 mils), we can see that we will finish with 33.4 microns (1.315 mils) for Class 2 and 38.4 microns (1.512 mils) for Class 3.
This is pretty clear, and again, close to the 1-ounce (35-micron) perception. But this is a different story as copper weights increase. If we look at the 2-ounce (70-micron), this is based on the perception that we have 35 microns to start, plus an additional 35 microns or 1-ounce base plating. If we start with 1 ounce or 30.9 microns (1.217 mils), plus plating of 20 microns (0.787 mils) for Class 2 or 25 microns (0.984 mils) for Class 3, and then allow for processing reductions of 3 microns (0.118 mils), we will finish with 47.9 microns (1.886 mils) for Class 2 or 52.9 microns (2.083 mils) for Class 3.
When we see drawings that call for a specific thickness such as 70 microns (2.756 mils) or 70 microns minimum, we have to start with 2-ounce base copper foil and plate up to achieve a finished thickness of 78.7 microns (3.098 mils) for Class 2 products or 83.7 microns (3.295 mils) for Class 3.
This has a notable impact on costs as there is a difference when quoting with a 1-ounce copper base or 2 ounces. This is why you may see questions from your PCB supplier as we seek to clarify what copper thickness you need, and what base copper thickness we should be starting with. We always want to help you avoid any unneeded additional costs in your PCB design. And, as always, if there are any questions on this or anything to do with your PCB design, I am happy to help.
Ruben Contreras is a program manager and field application engineer at NCAB Group.
More Columns from Fresh PCB Concepts
Fresh PCB Concepts: More Than Compliance—A Human-centered Sustainability ApproachFresh PCB Concepts: Assembly Challenges with Micro Components and Standard Solder Mask Practices
Fresh PCB Concepts: The Power of a Lunch & Learn for PCB Professionals
Fresh PCB Concepts: Key Considerations for Reliability, Performance, and Compliance in PCBs
Fresh PCB Concepts: Traceability in PCB Design
Fresh PCB Concepts: Tariffs and the Importance of a Diverse Supply Chain
Fresh PCB Concepts: PCB Stackup Strategies—Minimizing Crosstalk and EMI for Signal Integrity
Fresh PCB Concepts: PCB Plating Process Overview