-
- News
- Books
Featured Books
- design007 Magazine
Latest Issues
Current IssueProper Floor Planning
Floor planning decisions can make or break performance, manufacturability, and timelines. This month’s contributors weigh in with their best practices for proper floor planning and specific strategies to get it right.
Showing Some Constraint
A strong design constraint strategy carefully balances a wide range of electrical and manufacturing trade-offs. This month, we explore the key requirements, common challenges, and best practices behind building an effective constraint strategy.
All About That Route
Most designers favor manual routing, but today's interactive autorouters may be changing designers' minds by allowing users more direct control. In this issue, our expert contributors discuss a variety of manual and autorouting strategies.
- Articles
- Columns
- Links
- Media kit
||| MENU - design007 Magazine
Estimated reading time: 7 minutes
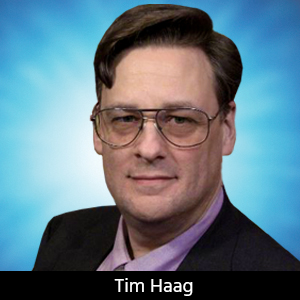
Tim’s Takeaways: Thermal Management for PCB Designers—Staying Out of the Fire
The Life of a PCB
If there’s one thing in life that really feels the pressure of being in the hot seat, it’s the PCBs that we design. After putting up with the trauma of having copper added and then etched away through exposure to ultraviolet light and various chemical baths, you would think that the PCB would deserve a little break. Instead, the board goes from the frying pan into the fire, so to speak, as the different layers get laminated together. This involves a great deal of heat and pressure, as the epoxy in the prepreg is melted to fuse the PCB layers together. Next comes drilling and plating, which is also no picnic, and by this point, the heat and pressure should finally be over for this little guy, right? But now the board needs to be assembled.
Our plucky hero has gone through all kinds of processes to complete its fabrication, including some intense scrutiny by both automated equipment and human inspection. Now, it’s back into the oven again—literally—for PCB assembly. Once the board has had its components pasted down onto it, it will be subjected to temperatures in the solder reflow oven that can get up to 255°C. That is almost 500°F for those of you who are thinking that perhaps it really isn’t so bad. Let me just say this; there isn’t a sunblock in the world with an SPF-value high enough to help with this kind of heat.
Not every PCB that is manufactured will go through the solder reflow oven—you’re right. But if they don’t go through reflow, they’re most likely go through wave solder instead. If you’re thinking that going through a wave sounds a little more pleasant than going through an oven, think again. We’re talking about a molten wave of solder, which can get up to 270°C if lead-free solders are used. How would you like to dip your toes into that kind of a wave?
As you can see, the PCB deserves our admiration for all the heat and pressure it has to deal with during manufacturing, but that is just the beginning. Next comes the regular day in and day out thermal stress of the board’s normal operating environment. All those electronic components can generate a lot of heat in themselves, and life for the board can get pretty toasty. That is what PCBs are created for, though, and why PCB designers like you put so much effort into designing them to survive and flourish in all that heat.
A PCB Designer’s Job
We start by designing boards with symmetrical layers of precisely-controlled copper evenly spread out to help with the fabrication process. We also take care in the placement and routing of PCB components to ensure there aren’t any problems with soldering during assembly. Additionally, we design the boards with their operating temperatures in mind by giving hot parts the space they need, as well as placing them where they can leverage the airflow across the board for cooling. We also use thermal vias to distribute heat throughout the board and incorporate heat sinks, fans, and other thermal management tools and devices, as necessary.
As PCB designers, we are accustomed to using a variety of procedures to manage the heat on our PCBs. However, the question is, “Do we give the same level of attention to managing the heat in our jobs as PCB designers?” Many designers tell me that they often find themselves under a lot of pressure while doing their work, which puts them squarely in the hot seat, looking for a fresh breeze of relief.
Four Techniques
We are already good at PCB design thermal management, so let’s consider four techniques in thermal management for PCB designers that might help.
1. Plan a Schedule
A lot of folks will ride the wave of the day in the performance of their jobs without any sort of planning at all. While this works for repetitive tasks, it can create a lot of stress for those who have schedule obligations that must be met. Certainly, we have our meetings and other company events planned in advance, so why not put a schedule around our design work too? The goal here is to prevent everything from piling up at the last moment and creating a catastrophic train-wreck with your deliverables. By planning regular milestones as you work, you can better manage the project’s long-range delivery dates and give yourself plenty of room to make schedule adjustments along the way, if necessary.
2. Manage Interruptions
When working in an environment where there are continual interruptions, it can be easy to get frustrated as each new interruption raises our temperature another notch. For PCB designers, this can be especially troublesome as the design process involves keeping several sequential tasks going all at the same time. “This via can move over as soon as this resistor is rotated, which I can do as soon as these traces are re-routed, which can only happen after I slide the capacitor a little down and to the left…” You can almost see the tasks floating around a designer’s head like little bubbles until an interruption causes all the bubbles to simultaneously pop, taking all those ideas crashing to the floor with them. To avoid this, try scheduling times when you shut down electronic interruptions and go dark to the outside world for a while. Of course, this requires planning so that other team members (and your boss) know what you are doing, but carving out blocks of uninterrupted time in your schedule can be a real game changer.
3. Document the Process
The temperature in the design room often gets elevated through poor communication. People may not know what they are supposed to be doing, or they may not know what you are doing. The best way to remedy this is through documentation. Make sure that everyone knows who the stakeholders are and who is calling the shots. It is also helpful if everyone has access to project schedules and timelines. Also, take the time to take some notes. I’m not talking about writing a novel here; just keep up with some simple entries in the project log. This makes it much easier for people to pick up where you left off, or for you to demonstrate why or why not certain tasks have or have not been completed.
4. Relax a Little
When the heat is on us, it is easy to get really wrapped up in our work. I’m sure that all of us have found ourselves working through the night on more than one occasion to get an important project out the door. The concern, though, is that having such a tight hold on what we are doing may make it difficult to let go when we need to. Sometimes, board designs change in mid-stream or even get canceled, and that can be really tough to deal with if we are hanging on too tight. What’s worse is to find out that we’ve made a mistake somewhere along the way and now we have to go back and correct it. Relax. We’re all human, and mistakes happen, so let it go. The important thing is to learn from any errors we have created so that we don’t make those same ones again. Take a deep breath and forgive yourself, and then get back into the game again.
Conclusion
There is one thing in life for certain: when an object gets too hot, it will change. In PCB design, we know this better than most, which is why we design our boards to manage an excess of heat. Objects that overheat tend to get crispy, inflexible or even melt away, which is the last thing we should allow to happen to us as PCB designers. The world of electronics design is constantly changing, and we must remain flexible to stay ahead of the rapidly changing curve and avoid the pressure that could lead to a melt-down.
What do you think? Has this helped to turn the thermostat down in the old design room yet? Remember, you already know how to manage the heat in your design to protect it; now, take the time to do the same for yourself. Until next time everyone, keep on designing.
This column originally appeared in the September 2020 issue of Design007 Magazine.
More Columns from Tim's Takeaways
Tim’s Takeaways: One for the ArchivesTim’s Takeaways: The Art of Technical Instruction
Tim’s Takeaways: PCB Design and Manufacturing—Let’s Work Together
Tim’s Takeaways: Take It From Scotty, Simple Really is Better
Tim’s Takeaways: Human Ingenuity and the Rigid-flex PCB
Tim’s Takeaways: How I Learned Advanced Design Strategies
Tim’s Takeaways: Batter Up—Stepping Up to the Substrate
Tim’s Takeaways: Tribal Knowledge—Not the Villain You Thought