-
- News
- Books
Featured Books
- pcb007 Magazine
Latest Issues
Current IssueInventing the Future with SEL
Two years after launching its state-of-the-art PCB facility, SEL shares lessons in vision, execution, and innovation, plus insights from industry icons and technology leaders shaping the future of PCB fabrication.
Sales: From Pitch to PO
From the first cold call to finally receiving that first purchase order, the July PCB007 Magazine breaks down some critical parts of the sales stack. To up your sales game, read on!
The Hole Truth: Via Integrity in an HDI World
From the drilled hole to registration across multiple sequential lamination cycles, to the quality of your copper plating, via reliability in an HDI world is becoming an ever-greater challenge. This month we look at “The Hole Truth,” from creating the “perfect” via to how you can assure via quality and reliability, the first time, every time.
- Articles
- Columns
- Links
- Media kit
||| MENU - pcb007 Magazine
Estimated reading time: 4 minutes
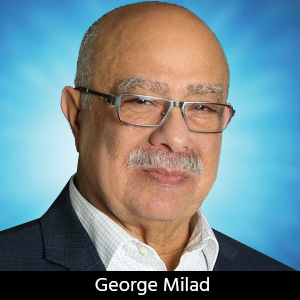
The Plating Forum: Immersion Plating Reaction in Electronics Manufacturing
Plating or metal deposition is a key component in the manufacturing of electronic packages (circuit boards and integrated circuits). Plating occurs when a metal ion in solution (electrolyte) is reduced to the metal. The reduction takes place when electrons are supplied to the ion:
The source of electrons differs with the type of plating as follows:
- Electrolytic plating: Electrons supplied by an external power supply (rectifier)
- Electroless plating: Electrons are supplied by a reducing chemical agent that is present in the electrolyte
- Immersion plating: Electrons are supplied by the oxidation of the (metal) substrate
This column will be dedicated to the immersion reaction.
Immersion reactions occur between metals according to their location in the electromotive (EMF) series. The EMF series is a listing of the elements according to their half potentials or tendency to lose electrons (get oxidized), or their tendency to gain an electron (get reduced), measured in voltage. Elements that lose electrons (reducers) have negative voltage values, and elements that gain electrons (oxidizers) have positive Eo voltage values.
Table 1 shows the half potentials Eo measured in volts of common elements, and metals are ranked with respect to their inherent reactivity. The metals located at the top of the series are considered the noblest with the highest level of positive electrochemical potential.
The electromotive force that drives an immersion reaction is determined by the difference in Eo (half potential) between the reduced and oxidized elements. The reduced element is the element receiving electrons and is derived as follows:
If the cell potential is positive, the reaction is spontaneous. A negative voltage indicates that no reaction will take place.
In printed circuit fabrication, immersion plating plays a key role in the following processes:
Immersion gold in electroless nickel/immersion gold (ENIG)
- Corrosion in ENIG
- Immersion gold in electroless nickel/electroless palladium/immersion gold (ENEPIG)
- Palladium catalyst on copper
- Immersion silver
- Immersion tin
Immersion Gold in ENIG
The deposition of gold on the electroless nickel substrate is an immersion reaction. The presence of nickel metal in an electrolyte containing gold ions creates a spontaneous deposition reaction. The EMF of the cell comes up to + 1.75 v, and the difference between the half potentials of gold +1.5 v (reduced species) and nickel –0.25 v (oxidized species) can be expressed as follows.
ENIG reaction:
Corrosion in ENIG
Corrosion may occur when the electrons released by the oxidation of nickel reduces the hydrogen ion present in solution releasing hydrogen gas. The EMF of the cell is + 0.25 v and is the difference between the half potentials of hydrogen (0.00 v) and nickel (–0.25 v).
Electroless nickel/hydrogen ion corrosion reaction:
The EMF driving force for this reaction is only 14% of the EMF for the gold deposition reaction and would only occur if the availability of the gold ion is interfered with. An example would be localized areas (crevices) where gold is depleted.
Nickel corrosion can be mitigated by:
- Eliminating crevices in the nickel
- Reducing the acidity of the electrolyte (reduced hydrogen ion availability)
- Reducing the half potential of nickel by increasing its phosphorous content
Immersion Gold in ENEPIG
Electroless palladium/immersion gold reaction:
In this galvanic cell, the gold is the reduced species, and the palladium is the oxidized species. Comparing the EMF of this cell to the EMF of the nickel/gold cell, it is clear that this reaction is less driven and would proceed slower than the deposition of gold on nickel. This creates a problem if the underlying nickel is accessible to the gold electrolyte. In this case, the gold would exchange with the nickel layer under the palladium and nickel corrosion would occur. For mitigation of nickel corrosion, refer to my previous column titled Can ‘Nickel Corrosion’ Occur In ENEPIG?
Palladium Catalyst on Copper
For an immersion palladium on copper reaction:
Immersion palladium on copper is an integral part of electroless nickel (EN) deposition. For EN to initiate on the copper substrate, the copper surface must be catalyzed. The catalyst is immersion palladium. In this galvanic cell, the palladium is the reduced species, and the copper is the oxidized species. Palladium ?sits below gold and above copper in the EMF series. Immersion palladium on copper is a spontaneous reaction driven by + 0.72 v. A palladium deposit is specific to the copper substrate and will not deposit on laminate or solder mask.
The uniformity of the palladium catalyst layer is critical. The uniformity depends on the pre-treatment of the copper surface, which must be free of oxidation or any contaminants. An uneven palladium distribution would lead to uneven EN initiation, generating crevices in the EN deposit, which are potential sites for nickel corrosion.
Immersion silver on copper:
The driving force for this reaction is + 0.46 v and would proceed spontaneously. Although the reaction is straight forward, the design of the electrolyte for immersion silver is a differentiating point from one supplier to the other and may include anti-tarnish components.
Immersion tin on copper:
Replacement reaction between Cu and Sn2+ cannot occur in a standard electrolyte because the EMF voltage is negative (- 0.48 v). The half potential of Cu is + 0.337 v, which is much higher than that of Sn is – 0.136 v.
For tin to immerse on copper, the half potential for copper must be reduced below the half potential of tin. The addition of a copper ion complexing agent, such as thiourea, will decreases the half potential of copper to – 0.620 v. ?(E0 for Cu[SC(NH2)2]4 = – 0.620 v).
In the presence of thiourea, the EMF for the immersion reaction is positive and would proceed spontaneously:
A good understanding of the principles of immersion plating goes a long way in eliminating costly defects that may occur during fabrication. It is a powerful tool in analyzing failure, as well as the subsequent assignable cause, and recommending corrective action.
This column originally appeared in the September 2020 issue of PCB007 Magazine.
More Columns from The Plating Forum
The Plating Forum: Reduction Assisted Immersion Gold for ENEPIG Surface FinishThe Plating Forum: Surface Finish Evolution from Conventional to Advanced
The Plating Forum: Plating in Electronic Applications
The Plating Forum: How the Pandemic Impacted PCB Manufacturing
The Plating Forum: The Significance of IPC ENIG Specification 4552 Revision B
The Plating Forum: The IPC Surface Finish Specifications
The Plating Forum: An Overview of Surface Finishes
The Plating Forum: DIG—The Next Generation