-
- News
- Books
Featured Books
- design007 Magazine
Latest Issues
Current IssueCreating the Ideal Data Package
Why is it so difficult to create the ideal data package? Many of these simple errors can be alleviated by paying attention to detail—and knowing what issues to look out for. So, this month, our experts weigh in on the best practices for creating the ideal design data package for your design.
Designing Through the Noise
Our experts discuss the constantly evolving world of RF design, including the many tradeoffs, material considerations, and design tips and techniques that designers and design engineers need to know to succeed in this high-frequency realm.
Learning to Speak ‘Fab’
Our expert contributors clear up many of the miscommunication problems between PCB designers and their fab and assembly stakeholders. As you will see, a little extra planning early in the design cycle can go a long way toward maintaining open lines of communication with the fab and assembly folks.
- Articles
- Columns
Search Console
- Links
- Media kit
||| MENU - design007 Magazine
Estimated reading time: 4 minutes
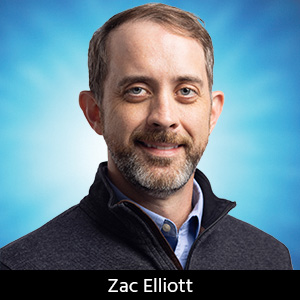
Lean Digital Thread: DFM Is Now as Easy as Spellcheck
In past columns, I’ve written about topics mostly related to the shop floor, including (1) data collection and the basic questions you can answer, (2) material management and its impact, and (3) data-driven decisions and micro-solutions in manufacturing.
In my September column, I planned to present a few micro-solutions for electronics manufacturing, but I’ve decided to “swim upstream” or simply to shift left. It is clear to everyone in the Industry 4.0 era that the holy grail is to close the loop between design and manufacturing. Mergers and acquisitions of billions of dollars were initiated to support this vision. In this column, I will talk about design for manufacturing (DFM).
A Prime Example
I’ll start with an anecdote from my retinal imaging startup company. One of our features was multi-spectral imaging using four different wavelengths. We developed a high-speed filter wheel that was synced to the retinal camera and the xenon bulb. The filter wheel had to spin twice along 125 milliseconds (the camera took eight images during that time—two per wavelength).
The prototype worked well, so we decided to move forward and go to mass production. I vividly remember our meeting with the CNC contractor. He took the filter wheel and just looked around; however, he did not even open the CAD drawings, nor did he use any test or measurement equipment. After a few minutes, he said, “You should have talked to me in advance. I don’t want to take this job. It’s not manufacturable.”
Left Shift: How to Overcome the Barriers
Shifting left is not easy. The environment is still pretty much in silos. While there’s still a good link between engineering and design or between engineering and manufacturing, it is still pretty difficult to communicate between design and manufacturing.
In a smart factory operation, people and machines are able to use this digital thread to provide feedback in a continuous flow of information. Languages that can communicate from people to machines, as well as between machines and processes, facilitate the data flow. They are the building block for a digital thread.
ODB++ is a data exchange format extended to the ODB++ family for a complete end-to-end digital solution, covering design, process, and manufacturing information flows. Each of these intelligent data exchange modules—ODB++Design, ODB++Process (previously known as OPM), and ODB++Manufacturing (previously known as OML)—is designed to be neutral and open, supporting all SMT machine vendors and all EDA software providers. With a complete digital twin of the electronics manufacturing flow—product, process, and performance—you can realize your smart factory or Industry 4.0 initiatives with confidence and efficiency.
Figure 1: Maintaining a digital thread with open, intelligent data exchange formats.
Challenge: Too Many NPIs or Complex Tools
New product introduction (NPI) in the electronics space is inefficient and expensive, with a cost of up to $20,000 per NPI. Taking a product from design through production requires time-consuming back and forth between electronics companies and contract manufacturers.
In the past, a company might do one NPI per month and could afford multiple iterations. However, the accelerating pace of the industry means that companies may do as many as five or 10 NPIs per day—and they need to speed up the process. In addition, data flows between the design and manufacturing ecosystems are hampered by trust issues. Designers can be reluctant to share their full IP, and manufacturers may not want to share processing constraints.
Current on-premise DFM solutions don’t talk to each other easily and are often out of reach for smaller companies. Solutions that can streamline the process and improve data flow can have a huge impact on budgets and productivity (Figure 2).
Figure 2: I bet you don’t want to make such mistakes.
Online Cloud-Based DFM: Accelerating Electronics Manufacturing
I assume that you all spellcheck your emails and that many of you already use Grammarly or similar services on a regular basis. You can now do the same with your designs, taking the first step in improving the communication and outcome with engineering and manufacturing.
A new platform could help you “spellcheck” your designs easily—an online solution making DFM checks easy and available for everyone, anywhere. It will also simplify your collaboration and data sharing (can you imagine software developers communicating with product managers without using collaboration tools, such as Miro or Asana?). The platform allows designers and manufacturers to safely share sensitive data that is vital to a smooth handoff. The platform can also recommend manufacturers suited for a particular design, and designers can submit their designs to different manufacturers to compare results.
Opening such a dialog will surely make it simple for designers to get actionable feedback from manufacturers and fix problems immediately, resulting in higher-quality designs. It also enables customers to easily connect with manufacturers that can meet their needs. The platform ensures that manufacturers receive designs that are ready to go, saving them time and money as well.
In my next column, I will talk about the next step: engineering and programming. In the meantime, feel free to drop me a note on LinkedIn.
Sagi Reuven is a business development manager for the electronics industry, Siemens Digital Industries. Download your free copy of the book The Printed Circuit Assembler's Guide to… Advanced Manufacturing in the Digital Age from Mentor, a Siemens Business, and visit I-007eBooks.com for other free, educational titles. You can also view Siemens’ free, 12-part, on-demand webinar series “Implementing Digital Twin Best Practices From Design Through Manufacturing.”
More Columns from Lean Digital Thread
Lean Digital Thread: The Manufacturing Metaverse RevisitedLean Digital Thread: The Secure Digital Thread
Lean Digital Thread: The Manufacturing Metaverse
Lean Digital Thread: Closing the Loop on Manufacturing
Lean Digital Thread: Keeping an Eye on Quality
Lean Digital Thread: Streamlining the Internal Supply Chain
Lean Digital Thread: Achieving Supply Chain Resilience
Lean Digital Thread: (Pro)curing the Supply Chain Virus