-
- News
- Books
Featured Books
- design007 Magazine
Latest Issues
Current IssueProper Floor Planning
Floor planning decisions can make or break performance, manufacturability, and timelines. This month’s contributors weigh in with their best practices for proper floor planning and specific strategies to get it right.
Showing Some Constraint
A strong design constraint strategy carefully balances a wide range of electrical and manufacturing trade-offs. This month, we explore the key requirements, common challenges, and best practices behind building an effective constraint strategy.
All About That Route
Most designers favor manual routing, but today's interactive autorouters may be changing designers' minds by allowing users more direct control. In this issue, our expert contributors discuss a variety of manual and autorouting strategies.
- Articles
- Columns
- Links
- Media kit
||| MENU - design007 Magazine
Estimated reading time: 4 minutes
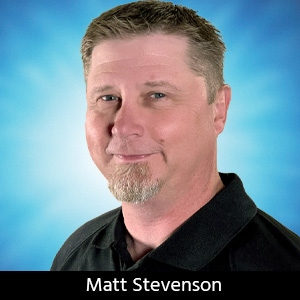
Connect the Dots: Unraveling the Mysterious BGA Routing Mess
A ball grid array (BGA) device can be a daunting component to route, especially in fine-pitch arrays featuring solder ball counts in the hundreds and pitch values as tight as 0.5 millimeters. With so much new technology requiring high-functioning processors and boards in increasingly miniaturized devices, it’s safe to say higher pin density, reduced lead inductance, and finer-pitch BGA devices will become even more common in our industry.
That means the foreseeable status quo will be less and less space to route traces and vias between pins. BGAs represent a challenge from design through prototyping and manufacturing, but with some sharp attention to detail and a plan focused on best practices, this is by no means an impossible task. Let’s look at how you can take the mystery out of BGA routing and create a PCB design that can handle all those pesky narrow spaces.
Start With a Little Research
BGAs have been around a while, so there are many resources available to provide some guidance and help you not to reinvent the wheel. There are some good online resources that can be very helpful, such as YouTube videos, blog posts, and technical papers. Most of these resources are free to access, leaving you to sift through the marketing noise and extract available learning that will be useful to you.
Know Where Trouble Can Lurk
Solder joints are where you really need to mind your Ps and Qs. Smaller surface areas reduce the strength of the solder connection and increase the risk of fracture. Thermal issues can create flex between the component and board and put additional stress on the solder joints. Keep this in mind as you conduct research into BGA best practices.
Vet Your Information Sources
Device manufacturers will often have helpful information on their websites, such as routing examples and land patterns. Typically, the part manufacturer’s footprint is optimized for soldering the part to the board but can leave you with an impossible routing solution. It’s important to learn when to follow their guidance and when to improvise in the name of manufacturability and functionality.
In most cases, it’s acceptable to reduce the BGA pad size sufficiently to allow for vias between the BGA pads. Typically, the BGA pad can be reduced to the same diameter as the BGA ball (nominal dimension) shown on the component datasheet.
Planning Is Key
BGAs of any size require a lot of room around them for all the wires and vias you will need to effectively make all the desired connections. Different board patterns will need optimal fan-outs or escape routing tailored to fit them. Examine each pattern carefully, scrutinizing spacing between solder balls, confirming if they are parallel and equidistant or have greater spacing in one direction, and establishing minimum trace width and spacing (Figure 1).
Figure 1: BGA solder.
Make sure that the critical signal paths and decoupling capacitors are well situated to maintain signal integrity and reduce inductance. Starting with the via escapes and fan-outs, keep some tried and true tricks in mind, such as high aspect ratio vias, micro-vias, or buried vias that will allow you to utilize real estate on all layers. These can be especially critical in the very large and fine pitch devices. Traces required to route between these pads and vias can also be reduced to provide an escape. You may need to use traces and spaces considerably smaller than the rest of the board in this case.
Adding signal layers is another trick to effective routing. Typically, one signal layer is needed for every two rows of pins, but if the BGA pitch is below 0.8 mm, you will need one signal layer per row. Keep in mind that increasing layers can be a relatively simple way to route the traces, but it can also increase the cost of the board and open the door for reliability issues. In many cases, it’s probably worth evaluating if a change to your layout can reduce the layer requirements.
Pro Tip
Make sure that you are working with a PCB manufacturer up front and understand their capabilities, especially as it relates to these aspects for the BGA routing. It is never fun to spend lots of time on a design and find your preferred vendor simply cannot manufacture it.
Use Your Design Tool
Many of the design tools today have functions to help make you more successful in your design efforts. Explore some of these functions and use them when they make the most sense for your design. Often, you can assign specific rules around your BGA that may differ from the rest of the board, saving you the time and effort of doing it on a trace by trace basis.
Good luck! Remember these best practices, and you too can make friends with the mysterious BGA.
Bob Tise is an engineer at Sunstone Circuits, and Matt Stevenson is the VP of sales and marketing at Sunstone Circuits. To read past columns or contact Tise and Stevenson, click here.
More Columns from Connect the Dots
Connect the Dots: How to Avoid Five Common Causes of Board FailureConnect the Dots: Sequential Lamination in HDI PCB Manufacturing
Connect the Dots: The Future of PCB Design and Manufacturing
Connect the Dots: Proactive Controlled Impedance
Connect the Dots: Involving Manufacturers Earlier Prevents Downstream Issues
Connect the Dots: Stop Killing Your Yield—The Hidden Cost of Design Oversights
Connect the Dots: Designing for Reality—Routing, Final Fab, and QC
Connect the Dots: Designing for Reality—Surface Finish