-
- News
- Books
Featured Books
- design007 Magazine
Latest Issues
Current IssueProper Floor Planning
Floor planning decisions can make or break performance, manufacturability, and timelines. This month’s contributors weigh in with their best practices for proper floor planning and specific strategies to get it right.
Showing Some Constraint
A strong design constraint strategy carefully balances a wide range of electrical and manufacturing trade-offs. This month, we explore the key requirements, common challenges, and best practices behind building an effective constraint strategy.
All About That Route
Most designers favor manual routing, but today's interactive autorouters may be changing designers' minds by allowing users more direct control. In this issue, our expert contributors discuss a variety of manual and autorouting strategies.
- Articles
- Columns
- Links
- Media kit
||| MENU - design007 Magazine
Estimated reading time: 7 minutes
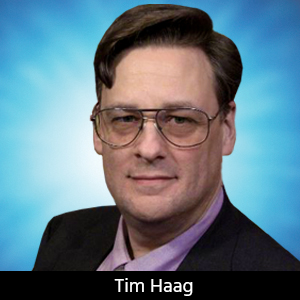
Tim’s Takeaways: PCB Vias, ‘You Have a Go’
Do you remember the old TV show “Stargate SG-1?” Debuting in 1997, it was a continuation of the 1994 movie “Stargate” and ran for 10 seasons, spawning two additional shows in the Stargate franchise. “Stargate SG-1” was known for its unique blend of sci-fi action and adventure, as well as a generous amount of humor.
The show also showcased a variety of well-done special effects, including creature design, makeup, and amazing starships and battles in space. The signature effect, of course, was the stargate itself, which was described as a wormhole through space. With the exhortation of “SG-1, you have a go” from their commanding officer, the stargate would instantaneously transport an intrepid band of heroes to new and exciting locations each week.
In addition to the general fun factor of the show, there was something else about it that appealed to me on a deeper level as a PCB design professional. It took me a long time before I figured it out, but when I finally did, I was stunned to realize that the stargate is nothing more than a giant via in space!
Okay, that may sound pretty lame, but if you think about the nature of a via, you can see where I’m coming from. Just as the stargate fictitiously conducted people directly from one place to another without the need for intergalactic space travel, a via will conduct a signal directly from one layer of the board to another. Of course, when you start adding time travel, energy weapons, and little gray aliens that aren’t wearing any trousers, the analogy falls apart pretty quickly. But at least we’re on the topic of vias now, which is where we wanted to be all along.
There was a time early in my career as a PCB designer, where we didn’t give much thought to the vias that we used. The signal speed of the designs we were working with was very slow compared to today’s standards, and except for fabrication costs, it didn’t really seem to matter how many holes got punched on the board. But as you know, that level of design technology is a long way behind us now. Vias are now much more than just a hole in the board to connect a signal from one layer to another; they are an integral part of the overall signal integrity of the design.
Take high-speed transmission lines, for example. For the best signal integrity, the traces of a transmission line should be contained on a layer that is sandwiched between two ground plane layers in a stripline configuration. This gives the best impedance control and shielding for the signal, plus the signal return path on the adjacent reference plane will be coupled directly to the signal.
The problem, of course, is that you can rarely contain a trace on just one internal layer. Even if the routing can be done on that one layer, you still need to transition to a surface layer to connect to the components through a via. Back in the day, we would have simply dropped a through-hole via and been done with it, but the high-speed routing requirements of today’s designs need a via solution with a little more finesse.
A through-hole via can act as an antenna and radiate energy, so we’ve come up with some ways to guard against that. Back-drilling the via is one of those ways while using blind vias is another. For high-density interconnect routing on boards with large pin-count ICs, microvias are often the best option. All of this is done to keep the signal path as short as possible through the via, with the added benefit of opening up some more routing channels where the through-hole via used to be. But using vias on a high-speed transmission line opens up yet another can of worms that, interestingly enough, requires the use of even more vias to resolve.
A signal needs a return path, and this is usually accomplished through a ground plane. For a high-speed transmission line, however, the return path becomes even more important and must be clearly defined in order to avoid problems that can disrupt the function of the circuit. The reference planes in a design are looked at very carefully now to make sure that there aren’t any plane splits, slots, and other congested areas that can clog up the signal return paths. Without a clear return path for the signal, the circuit may develop unwanted noise resulting in crosstalk, interference, and even false triggering of the signal.
Therefore, to maintain the best signal integrity, the transmission line needs to be directly adjacent to the ground plane that it is using for its signal return path, and the plane must supply a clear path. When the signal transitions to another layer through a via, however, the return path will be severed unless there are ground stitching vias nearby for the return path to hitch a ride on. These ground vias provide the means for the signal return to continue its path back to the source in what is known as layer paired routing.
There’s still more to how we choose which vias to use and where they should be placed, as well as the need for transmission line signal integrity. For instance, power circuits will need a larger via to handle the current that they are carrying. Without an adequate size, things can get a little toasty for the smaller vias, which is why power pins are usually routed with wider lines and larger diameter vias.
In some cases, vias are also used to transfer heat. Since a circuit board with all its different internal layers and metal planes makes for an excellent heatsink, adding vias under hot components will dissipate that heat throughout the board. This can bring a lot of heat relief to those parts instead of allowing the heat to build up in those areas of the board where the parts are located.
Circuit board test is another important use of a via. To test the connectivity of a fabricated board—as well as the assembly integrity of a fully manufactured board—a variety of tests are conducted on the PCB. These include using test fixtures with probes for every net on the circuit board that contact all the points designated as testpoints simultaneously.
Another method is known as a flying probe test, which is a machine that probes each testpoint individually. The important part of these different testing methods, however, is that vias usually serve as the testpoints which the probes come in contact with.
To facilitate this testing, a PCB designer will use some specialized features in their CAD tools to flag specific vias as testpoints. With a via marked as a testpoint, the location of that via and the net it is attached to then can be extracted from the CAD database in order to create a testpoint file. This data is then used for building test fixtures and programing the test machines. In some cases, the size and shape of the testpoint vias will even be changed on the layout to visually identify them as a testpoint on the fabricated circuit board.
Additionally, these testpoint vias are usually subjected to additional design rules and constraints than a regular via is. For obvious reasons, they can’t be placed under components, and they need to have specified clearances from each other to ensure that the probes on the bed-of-nails test fixture can easily access them.
Considering all that they are used for and what is required of them, vias are actually subjected to a lot more action and adventure than I would have expected. I wouldn’t put them on the same level of excitement as SG-1, but vias do have a lot of intricacies to them that commands respect. There is a lot to consider when working with them to ensure that your PCB design performs up to specification and is manufacturable the way you intended it to be.
Thankfully, there are people in the design community who are a whole lot smarter than I am about the best way to work with vias. You have the opportunity to learn from them in this edition of Design007 Magazine. I’m looking forward to reading myself what I-Connect007 and its experts have to say about vias when I receive my own copy. Until next time then, keep on designing, and vias, you have a go!
Tim Haag writes technical, thought-leadership content for First Page Sage on his longtime career as a PCB designer and EDA technologist.
This column originally appeared in the November 2020 issue of Design007 Magazine.
More Columns from Tim's Takeaways
Tim’s Takeaways: One for the ArchivesTim’s Takeaways: The Art of Technical Instruction
Tim’s Takeaways: PCB Design and Manufacturing—Let’s Work Together
Tim’s Takeaways: Take It From Scotty, Simple Really is Better
Tim’s Takeaways: Human Ingenuity and the Rigid-flex PCB
Tim’s Takeaways: How I Learned Advanced Design Strategies
Tim’s Takeaways: Batter Up—Stepping Up to the Substrate
Tim’s Takeaways: Tribal Knowledge—Not the Villain You Thought