-
- News
- Books
Featured Books
- design007 Magazine
Latest Issues
Current IssueAll About That Route
Most designers favor manual routing, but today's interactive autorouters may be changing designers' minds by allowing users more direct control. In this issue, our expert contributors discuss a variety of manual and autorouting strategies.
Creating the Ideal Data Package
Why is it so difficult to create the ideal data package? Many of these simple errors can be alleviated by paying attention to detail—and knowing what issues to look out for. So, this month, our experts weigh in on the best practices for creating the ideal design data package for your design.
Designing Through the Noise
Our experts discuss the constantly evolving world of RF design, including the many tradeoffs, material considerations, and design tips and techniques that designers and design engineers need to know to succeed in this high-frequency realm.
- Articles
- Columns
- Links
- Media kit
||| MENU - design007 Magazine
Chapter 1 Excerpt: The Printed Circuit Assembler’s Guide to Process Validation
December 31, 2020 | Graham Naisbitt, Gen3 SystemsEstimated reading time: 2 minutes
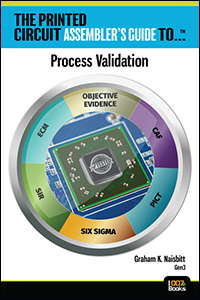
Quick and Convenient Contamination Testing
The original principle underlying the IPC’s ionic cleanliness requirement was that the mobility of surface ions, detectable from SIR measurements, would correlate to a maximum value of detectable ionic elements permissible on the circuit surface.
The industry required a test that was both fast and accurate for process control. Thus, a simplified ion chromatograph that was able to detect ionic elements without differentiation was created. Due to patent restrictions, there were—and still are—only two different instrument configurations: closed-loop and open-loop, which became referred to as static and dynamic instruments. Each instrument configuration must be capable of measuring the presence of a known amount of ionic contamination.
Based on an extrapolation of insulation resistance measurements, it was determined that there was an upper limit beyond which ionic elements would become mobile on the assembly surface, thereby potentially compromising electrochemical reliability. The number, although occasionally altered during the infancy of this test, was 1.56 µg/cm² NaCl equivalence. Despite the many technology changes employed in the period after the mid-1970s, many—if not most—felt it convenient to simply continue applying this rule as adequate evidence of the electrochemical reliability of their end-product.
The IPC has now withdrawn the requirement for 1.56 µg/cm² NaCl equivalence for a number of reasons as explained in IPC-WP-019A, which states, “For many years, military (e.g., MIL-STD-2000) and commercial (e.g., IPC-J-STD-001) manufacturing standards have required manufactured circuit card assemblies (CCAs) to meet an ionic cleanliness requirement of 1.56 microgram (µg) of sodium chloride (NaCl) equivalence per square centimetre (cm2) of extracted surface, using resistivity of solvent extract (ROSE) testing per IPC-TM-650, method 2.3.25.”
Therefore, it is the position of the IPC committees that the value of 1.56 µg NaCl equivalence per square centimetre should be considered as obsolete for the following seven reasons:
- This test methodology was originally developed in the 1970s. It was never intended to be used as a cleanliness test, nor as a test for product acceptability; it was only intended to be used as a process control method.
- The use of the ionic contamination value as a measure of product acceptance was the result of a U.S. Department of Defense desire to implement pass/fail criteria.
- This ionic contamination value, and those derived from them, were originally developed for high solids (35% solids) rosin fluxes and ozone-depleting chemical (ODC) cleaning. The flux chemistries and cleaning solutions used today are completely different from those used when the ROSE limits were established.
- Modern assemblies are simply too complex in terms of residues to have a single “one-size-fits-all” cleanliness criterion.
- There is mounting evidence that as CCA component density increases, so does the sensitivity of the circuit to ionic contamination. Modern circuit assemblies have far greater component densities than found in the 1970s. This also means that residues that had minimal impact on component technologies from the 1970s can now have a significant impact on component reliability.
- For many assemblies, ROSE testing is no longer a sufficient test regimen to adequately predict acceptable levels of ionic residues. IPC has compiled a list of technical presentations showing the inadequacy of ROSE to predict ionic residues for high-performance electronics.
- It is recognized that ionic residue testing is critical for reliable circuit function, so the ROSE test has continued in use until a more suitable alternative can be identified and implemented.
To download The Printed Circuit Assembler’s Guide to Process Validation, click here. You can also view other titles in our full library.
To view the Gen3 roundtable on the PICT standard, click here.
Suggested Items
The Global Electronics Association Releases IPC-8911: First-Ever Conductive Yarn Standard for E-Textile Application
07/02/2025 | Global Electronics AssociationThe Global Electronics Association announces the release of IPC-8911, Requirements for Conductive Yarns for E-Textiles Applications. This first-of-its-kind global standard establishes a clear framework for classifying, designating, and qualifying conductive yarns—helping to address longstanding challenges in supply chain communication, product testing, and material selection within the growing e-textiles industry.
IPC-CFX, 2.0: How to Use the QPL Effectively
07/02/2025 | Chris Jorgensen, Global Electronics AssociationIn part one of this series, we discussed the new features in CFX Version 2.0 and their implications for improved inter-machine communication. But what about bringing this new functionality to the shop floor? The IPC-CFX-2591 QPL is a powerful technical resource for manufacturers seeking CFX-enabled equipment. The Qualified Product List (QPL) helps streamline equipment selection by listing models verified for CFX compliance through a robust third-party virtual qualification process.
Advancing Aerospace Excellence: Emerald’s Medford Team Earns Space Addendum Certification
06/30/2025 | Emerald TechnologiesWe’re thrilled to announce a major achievement from our Medford, Oregon facility. Andy Abrigo has officially earned her credentials as a Certified IPC Trainer (CIT) under the IPC J-STD-001 Space Addendum, the leading industry standard for space and military-grade electronics manufacturing.
Magnalytix and Foresite to Host Technical Webinar on SIR Testing and Functional Reliability
06/26/2025 | MAGNALYTIXMagnalytix, in collaboration with Foresite Inc., is pleased to announce an upcoming one-hour Webinar Workshop titled “Comparing SIR IPC B-52 to Umpire 41 Functional & SIR Test Method.” This session will be held on July 24, 2025, and is open to professionals in electronics manufacturing, reliability engineering, and process development seeking insights into new testing standards for climatic reliability.
IPC Rebrands as Global Electronics Association: Interview With Dr. John W. Mitchell
06/22/2025 | Marcy LaRont, I-Connect007Today, following a major announcement, IPC is embracing the rapid advancement of technology with a bold decision to change its name to the Global Electronics Association. This name more accurately reflects the full breadth of its work and the modern realities of electronics manufacturing. In this exclusive interview, Global Electronics Association President and CEO Dr. John W. Mitchell shares the story behind the rebrand: Why now, what it means for the industry, and how it aligns with the organization’s mission.