-
- News
- Books
Featured Books
- design007 Magazine
Latest Issues
Current IssueProper Floor Planning
Floor planning decisions can make or break performance, manufacturability, and timelines. This month’s contributors weigh in with their best practices for proper floor planning and specific strategies to get it right.
Showing Some Constraint
A strong design constraint strategy carefully balances a wide range of electrical and manufacturing trade-offs. This month, we explore the key requirements, common challenges, and best practices behind building an effective constraint strategy.
All About That Route
Most designers favor manual routing, but today's interactive autorouters may be changing designers' minds by allowing users more direct control. In this issue, our expert contributors discuss a variety of manual and autorouting strategies.
- Articles
- Columns
- Links
- Media kit
||| MENU - design007 Magazine
Estimated reading time: 5 minutes
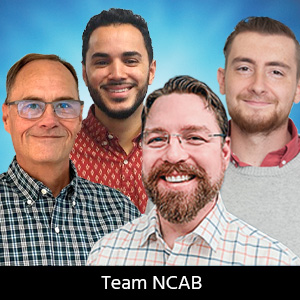
Fresh PCB Concepts: Attacking the Loophole That Does Not Exist
When producing PCBs, we follow IPC standards for Qualification Performance and Acceptance from design, through production, to customer incoming inspection and acceptance. However, there is always a way of writing a standard and a different way of interpreting it.
Today I will attack a loophole that does not exist yet is still used by many. Let’s dig into the term “workmanship” as written in IPC-6012E 3.3.1, which represents the Qualification and Performance Specification for Rigid Printed Boards. You find the same section in IPC-6013 and IPC-6018. The requirement says:
IPC-6012E 3.3.10: Workmanship
Printed boards shall be processed in such a manner as to be uniform in quality and show no visual evidence of dirt, foreign matter, oil, fingerprints, tin/lead or solder smear transfer to the dielectric surface, flux residue and other contaminants that affect life, ability to assemble and serviceability. Visually dark appearances in non-plated holes, which are seen when a metallic or non-metallic semi-conductive coating is used, are not foreign material and do not affect life or function. Printed boards shall be free of non-conformances in excess of those allowed in this specification. There shall be no evidence of any lifting or separation of platings from the surface of the conductive pattern, or of the conductor from the base laminate in excess of that allowed. There shall be no loose plating slivers on the surface of the printed board.
Are We Misinterpreting the Standards?
A typical understanding of this requirement is often limited to “no visual evidence of dirt, foreign matter, oil, fingerprints, tin/lead or solder smear transfer to the dielectric surface, flux residue and other contaminants that affect life, ability to assemble and serviceability.”
Also note: “There shall be no evidence of any lifting or separation of platings from the surface of the conductive pattern, or of the conductor from the base laminate in excess of that allowed. There shall be no loose plating slivers on the surface of the printed board.”
As written, there is a requirement here; not measureable, but it’s still quite clear. But, are we missing something here?
In my daily work I often discuss what is acceptable with suppliers. We read the related standards, explain, and give examples. We try to agree on how to understand the specific requirement or a combination of several requirements. Then we inspect the related boards and agree on what we observe. Some years ago, the defects we found were functional, such as open circuit, short circuit, and via hole, that will cause functional problems.
The Difference Between Cosmetic Issues and Cosmetic Failure
Today’s factories have better process control and improved functional testing, meaning that most of the claims are what can be called cosmetic. The challenge is knowing what is cosmetic, and what is purely a cosmetic issue that could lead to a failure in the application.
This leads me back to the standard, and the sentence that many PCB suppliers often overlook: “Printed boards shall be free of non-conformances in excess of those allowed in this specification.”
The last revision of the standard, and still written in IPC-6013 and IPC-6018, says: “Printed boards shall be free of defects in excess of those allowed in this specification.”
The word defect has then, if we are kind to the reader, been understood as functional:
- What is a defect?
- Is a cosmetic imperfection a defect?
The next revision uses the term non-conformance, and we hope that helps. Here, it must be understood as any imperfection to the PCB design.
Before we discuss this further, it is important to understand that even an up-to-date PCB factory will have some handling, and smaller cosmetic issues will occur. It is very important that the user understands and does not reject fully functional products.
For further understanding I suggest reading my April 2020 column, keeping in mind what I discussed last year that it is still important for the PCB supplier to understand the standard and have a goal to reduce such cosmetic issues.
Workmanship: What Does the Standard Really Say?
What the standard says about workmanship is, in reality, that the PCB shall be free of any imperfection not allowed in this specification. But what are we talking about? I would say that more than 60% of customer claims are related to solder masks in one way or the other. Let me give some examples:
All of us producing and using PCBs know that handling in production will lead to scratches in the solder mask. But what is the criteria to accept a scratch? How many scratches, and how deep? The immediate answer is that IPC does not specify what is acceptable or not. The only requirement we have is the workmanship rule that says a scratch is an imperfection that is not allowed.
So, what is the solution? We need to talk together and agree upon reasonable inspection criteria.
The processing of solder mask today is in a much cleaner environment than before. The clue is cleanroom areas that enable the factory to deliver a clean solder mask, free from unwanted particles that mostly come from the application room condition and workers' clothes. Still, we are not yet at a level where we can guarantee the solder mask will be 100% clean from unwanted particles. Such room conditions are costly and many factories trade between a defect free solder mask and the cost of such conditions.
But what are the requirements? Even though not written specifically in IPC-6012 series, an unwanted particle can in worst case lead to a defect in the application. And, with the miniaturisation of PCB designs, existing clearance rules may not be sufficient. Again, the rule is such that unwanted particles are not allowed. We know it happens, so we need an inspection criterion just like the solder mask scratch issue.
Discuss and Accept Acceptability Criteria for Both Parties
Both of these issues represent a condition not allowed according to the workmanship specification. These issues happen daily, and in most cases, the PCB supplier will handle it as a cosmetic issue and therefore the customer shall accept it. But that is not what IPC says. It is important to know the standard and understand the requirements, but even then, you will have a grey zone situation where the only solution is to talk together and discuss acceptability criteria that is satisfactory to both parties. The user should also understand that the workmanship standard may have different effects on different base materials, and between a prototype or small volume order compared to volume manufacturing.
Conclusion
What can we learn from this? The most important is to know the standard and how to use it. Most people read the measurable requirements, while a requirement like the workmanship rule is left out. It is hard to deal with because it requires at least two parties to find a solution that works for both. This, however, leads to my next article, which will focus on the term AABUS (As Agreed Between User and Supplier), meaning these open requirements shall be discussed with the supplier, be part of the article specification, or agreed in a general procurement requirement.
Until next time …
This column originally appeared in the February 2021 issue of PCB007 Magazine.
More Columns from Fresh PCB Concepts
Fresh PCB Concepts: More Than Compliance—A Human-centered Sustainability ApproachFresh PCB Concepts: Assembly Challenges with Micro Components and Standard Solder Mask Practices
Fresh PCB Concepts: The Power of a Lunch & Learn for PCB Professionals
Fresh PCB Concepts: Key Considerations for Reliability, Performance, and Compliance in PCBs
Fresh PCB Concepts: Traceability in PCB Design
Fresh PCB Concepts: Tariffs and the Importance of a Diverse Supply Chain
Fresh PCB Concepts: PCB Stackup Strategies—Minimizing Crosstalk and EMI for Signal Integrity
Fresh PCB Concepts: PCB Plating Process Overview