Estimated reading time: 7 minutes
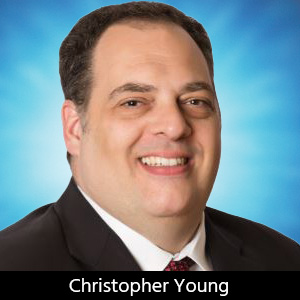
Adventures in Engineering: ‘Precision’ Resistors (With First Column Introduction)
Hi, I’m Chris Young and I’d like to take this opportunity to introduce myself.
I have more than 20 years of experience as an electrical engineer, but I have always had a fondness for designing circuit boards—which actually took root when I was about 11 years old, and I got to see the insides of a computer mainframe. I immediately wanted to know what those cool-looking, greenish boards were and who made them. Even then, I knew that was what I wanted to do in my future, and here I am now, over 30 years later, living that dream.
My experience has been working predominantly in the avionics/aerospace industry, supplemented by experience in the semiconductor and medical fields.
I have worked on and led teams involved in highly innovative aerospace products, such as:
- SafeRoute: The first certified ADS-B IN solution in avionics history and start to certification in 12 months
- T3CAS: The first fully integrated TCAS/Transponder/TAWs solution in avionics history
- Orion spacecraft: Designed test station for pyro driver module housed within the power and data units on the Orion spacecraft. I co-designed the test station for the vehicle management computer on the Orion spacecraft
I have a broad range of experience from the first phases of product design, certification testing, and through product sustaining. I have well over 100 circuit board designs used in flight hardware, space test systems, avionics specific test system instrumentation (Discrete IO, ARINC 429, 717, 644, etc.), experimental flight test, semiconductor test and characterization, medical product test, military test systems, and aircraft harness level simulated interface load boards for HIRF.
I’m looking forward to sharing my extensive knowledge in experience in system design/architecture, hardware design, product test development (hardware and software), and product support, all within the realm of mil/aero.
I welcome your comments and suggestions as I embark on this monthly column. I am the owner/lead engineer of Young Engineering Services LLC, and chief hardware engineer at The Goebel Company. I can be reached at chris.young@young-eservices.com.
Now, on to my first column …
'Precision' Resistors
Precision resistors (tolerance < 1%) are known to be of great use in the Mil/Aero industry and are commonly under analyzed in the design/sustaining processes a product typically goes through. Design mistakes caught during certification testing are expensive because the units under test are under a heightened level of quality control (typically referred to as conformity), test equipment/facilities are being leased, and changes may require regression testing. Mistakes made in the sustaining process create yield issues in manufacturing and/or worse, failures in the field. Most problems I encounter with precision resistors are related to their temperature coefficient of resistance (TCR). TCR is specified in parts per million (PPM) per degree Celsius. Precision resistor TRC impact on design and sustaining processes will be our area of focus.
Typical applications for precision resistors are amplifiers, resistor dividers, current sensing, and voltage bias applications. The design challenge with amplifiers and resistor dividers is to maintain a precise resistor ratio to provide stable gain and reference voltages. Current sensing has many useful applications such as power monitoring, 4-20mA current loops, current fault detection, and motor control. The design challenge with current sensing is maintaining a stable resistance so that the current flowing through the current sense resistor can be accurately measured. These design challenges must be met not only on the lab bench, but over the application’s specified temperature range. The operating temperature range of an electronics bay in a commercial aircraft is -55–70°C and full military operating temperature range is -55–125°C.
An inverting amplifier is a straightforward application, the gain is set by the ratio of two resistors (Figure 1). The design requirement is that the gain must be -5 within a tolerance of 0.25% and the input range is 0-3V. Let us choose R1 = 5k ohms and R2 = 1k ohms (-5k/1k = -5). If we choose resistors with a tolerance of 0.1%, then we should have a gain tolerance within 0.21%. Furthermore, if the TCR of the resistors are the same, then the resistors should maintain a relatively stable ratio over temperature, so TCR is not critical. Power dissipation in R1 and R2 should be upward of 3mW and 45mW, respectively. To be safe, we choose to use 1206 resistors (250mW) so that self-heating is kept to a minimum and a higher TCR, 50 PPM because it costs less, and being the cost-conscious engineer most of us are, this is where I see the analysis stop in most cases.
The assumptions made in the above analysis is that the resistors would reside in the same environment. This is not always true and accounts for almost all the precision resistor design issues I have encountered in my career. PCB board layout can dramatically affect the stability of a resistor ratio over temperature. Two common layout issues are placing hot components next to precision resistors and placing paired resistors on opposite sides of the PCB (Figures 2, 3, and 4 show a simplified inverting amplifier circuit layout). Placing a precision resistor near a hot component (load resistors, power MOSFETs, linear regulators, and amplifiers) on the same side of the PCB can result in an increase in temperature by 5–10°C (Figure 2).
It is usually acceptable to place these resistors near hot components they are associated with, but away from hot components they are not (Figure 3). The temperature from one side to another on a PCB can vary significantly. I have seen temperatures vary upward of 25°C in avionics applications.
This will directly affect the gain of an amplifier circuit if the resistors in the feedback loop are on opposite sides of the PCB (Figure 4). Let us re-visit our design problem above where we have a solution that will produce a gain accuracy within 0.2%. Our goal is to stay under 0.25% and we have chosen to use resistors with a TCR of 50 PPM/C. In Figure 4, Resistor R1 is on the bottom of the board, and R2 is on the top of the board. The SOIC-8 package is a power op amp with an exposed power pad and vias are used to sink heat to the back of the board. The backside of the PCB will be at a higher temperature than the topside of the board. I have seen designs where the backside is upward of 25 degrees higher, with a TCR of 50PPM/°C (0.005% per degree Celsius). The resistor value on the backside would change by 0.005% X 25 = 0.125% more than the resistor on the top side.
The additional uncertainty due to temperature differences of the resistors in the feedback of the amplifier has now pushed the total uncertainty to 0.325%. The design is no longer able to meet the requirement of 0.25% and may fail verification tests during design certification testing. This is an expensive and time-consuming point in the product cycle to find these types of mistakes for an avionics or military product. Certification test units typically are under quality control (CONFORMITY—the quality process/check-out typically used to determine the test units are built and configured similarly or exactly like a production unit) and any changes to the product to fix (use 5 PPM/C part) design issues become inundated by process and paperwork. This inundation translates to project delays and budget overruns.
Product sustaining has its own challenges regarding maintaining the integrity of the design while keeping the cogwheels of production running. Issues like obsolescence, component availability, and cost reduction initiatives will often lead to component substitutions when a product is in active production. Mil/Aero life cycles can be upward of 30 years in some cases so the chances that a product will undergo change or have component replacements is very, very high. This is where documentation is important. If you have chosen a precision resistor for your design, then put a note in the schematic/parts list about why it is there and specify the TCR. Leave some breadcrumbs for future engineers to service your design while it’s in production. Bad component replacements in production can lead to severe yield issues in the factory. I have personally experienced entire production line shutdowns because of this and worked 100+ hour weeks (along with fellow employees) to get production back up and running. I have also seen where a bad resistor replacement caused failures in the field resulting in airplanes being grounded for repair. In this case, a transistor bias compensation circuit was not working properly over temperature and was causing a transistor to fail after repeated cold temp startups. This was due to a resistor that had a high TCR (300 PPM/C). The original design had a 25 PPM/C component. In avionics reliability issues in the field left unresolved can lead to regulatory authorities grounding airplanes and suspending certification of products used in aircraft because the reality is that people’s lives depend on the instruments on aircraft to work properly.
The seemingly mundane task of picking a resistor can have significant effects on a product throughout its life cycle and care should be taken to make sure it is done right.
Chris Young is owner/lead engineer of Young Engineering Services LLC and chief hardware engineer at The Goebel Company.
More Columns from Adventures in Engineering
Adventures in Engineering: A Penny Primer on PCB Design FundamentalsAdventures in Engineering: 5G Expansion and Radar Altimeters
Adventures in Engineering: Supply Chain Management
Adventures in Engineering: Data Management Not Just Checking the Boxes
Adventures in Engineering: Connectors—The Right Fit
Adventures in Engineering: A Purpose-Driven Prototype
Adventures in Engineering: Test Points—The Other Side
Adventures in Engineering: The Ecosystem of Autonomous Flight