Estimated reading time: 5 minutes
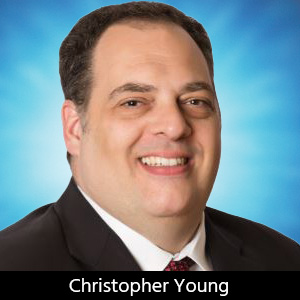
Adventures in Engineering: Component Unavailability
Component unavailability is a thorn in the side of everyone from engineering to manufacturing, and is manifested in many ways: obsolescence, long lead times, raw material shortages, and catastrophic events (fires, natural disasters), just to name a few.
Not having the components available to fabricate/assemble prototypes or manufacture products affects product development schedules and causes missed deliveries. This is especially problematic in the avionics industry because these problems cause aircraft to be held up on the manufacturing line and cause a shortage of units available for aircraft maintenance. Late delivery of new aircraft and lack of replacement parts for repair impairs everyone’s ability to fly without delays and cancelled flights. Severe resistor and capacitor component shortages in the late 2010s, as well as today’s fabless semiconductor component lead time expansions, warrant a top-down evaluation of the avionics product life cycle. Let us focus and explore some of the design and manufacturing aspects of an aircraft line replaceable unit (LRU).
A typical development program for an aircraft LRU, in my experience, is between 12 to 36 months, depending on the complexity of the program; meeting the schedule becomes critical. Component availability directly affects the build of conceptual, early implementation, and certification prototypes needed to meet design milestones. A key factor in product development in the aerospace industry is demonstration of a working product. Aircraft LRUs such as transponders, TCAS (traffic collision avoidance systems), and NAV/COM radios have a regulatory required minimum operating specification (MOPS) that are intended to demonstrate acceptable functionality in an aircraft environment.
You cannot demonstrate what you do not have. A delay in component availability is a delay in schedule. Unfortunately, component shortages have been all the rave lately, at least in my opinion. Seriously though, the prevalence of component unavailability suggests that design steps should be taken to mitigate this risk. Let us help our friends in supply chain management.
Easily enough said, but what are the steps to make this happen? I have found the following design practices to be helpful as a design mitigation to component unavailability.
- Design products using a platform approach so that multiple products use the same or similar components. This may seem counterintuitive, but it reduces the scope of work involved in the design mitigation of risk across a large range of products.
- When performing the design stress and derating analysis of a circuit, I will include not only the optimal components but also similar parts that may meet the requirement. This may mean evaluating several specific operational amplifier components for an amplifier or active filter circuit to identify suitable alternatives. These alternatives would then be subject to testing in prototypes, eventually making their way to parts lists, bill of materials, and approved components lists.
- When it comes to RF, instead of using large multi-pole (more than four) filters, use multiple cascaded smaller filters separated/isolated by a gain block or unity gain amplifier. A bandpass filter with many frequency poles typically means using very precise and specific value components that are hard to come by even in a flush distribution environment.
- If you need a six-pole bandpass filter to meet your design requirements, then consider breaking this down into two cascaded three-pole filters. This alternative will be easier to tune and will not require such an exact component selection.
- Resistors used for power supply feedback and setting switching frequency in a switch mode power supply can easily be an uncommon value like 344K ohms. You may be able to find a lot of part numbers that support this value, but distributors may not have this part readily available.
- It is prudent to perform cursory searches on distributor websites to get an overall sense of component availability as your design firms up and becomes finalized. Remember, an important aspect of practical design is component availability over component possibility.
Production of avionics hardware is often done in batches to avoid the cost of small or single piece builds. I typically see batch builds of circuit boards ranging from quantities of 25 to several hundred every few months. The biggest issue I encounter is that part availability is only considered at the onset of a new batch build. I have seen components cleared out of distribution supply chains in just a few weeks and this seems to be becoming normal behavior, since the passive component shortages that became painfully noticeable in 2018. Almost all the circuit board builds I deal with directly are batch builds and here are some practices that I find helpful.
First, inexpensive (less than 5% BOM cost) passive components are purchased at least one batch ahead, so there is time to mitigate simple component shortages. I design for and document (in parts lists and approved alternatives lists) a means of using a defined range of simple pull-up/down resistor alternatives so that a distributor run on 100K, 20K, 10K, and 1K, and 330-ohm resistors does not cause a stop work on my builds. Purchasing full reels of passive components for groups of products on the same design platform is less expensive and wasteful than using cut tape quantities. A common practice is to sacrifice a portion of the cut tape to put the parts into a SMT feeder. I have witnessed upward of 30% of a cut tape be sacrificed in order to load a feeder. Having a distributor put a leader on a cut tape will cost around $7 per tape, but the cost of sacrificing 200 0402 resistors is typically less than $3 and that is why contract manufacturers tend to over-purchase cut tape quantities for single product type builds. This places a false demand on passive products that can otherwise be put to good use.
As component shortages seem to be becoming the norm, design mitigation of component unavailability needs to become standard practice in the avionics industry. Also, as we strive to continuously improve our manufacturing practices, our “least waste way” of product assembly should find a way to avoid the waste commonly associated with cut tape component reels.
Christopher Young is owner/lead engineer of Young Engineering Services LLC and chief hardware engineer at The Goebel Company.
More Columns from Adventures in Engineering
Adventures in Engineering: A Penny Primer on PCB Design FundamentalsAdventures in Engineering: 5G Expansion and Radar Altimeters
Adventures in Engineering: Supply Chain Management
Adventures in Engineering: Data Management Not Just Checking the Boxes
Adventures in Engineering: Connectors—The Right Fit
Adventures in Engineering: A Purpose-Driven Prototype
Adventures in Engineering: Test Points—The Other Side
Adventures in Engineering: The Ecosystem of Autonomous Flight