-
- News
- Books
Featured Books
- smt007 Magazine
Latest Issues
Current IssueSupply Chain Strategies
A successful brand is built on strong customer relationships—anchored by a well-orchestrated supply chain at its core. This month, we look at how managing your supply chain directly influences customer perception.
What's Your Sweet Spot?
Are you in a niche that’s growing or shrinking? Is it time to reassess and refocus? We spotlight companies thriving by redefining or reinforcing their niche. What are their insights?
Moving Forward With Confidence
In this issue, we focus on sales and quoting, workforce training, new IPC leadership in the U.S. and Canada, the effects of tariffs, CFX standards, and much more—all designed to provide perspective as you move through the cloud bank of today's shifting economic market.
- Articles
- Columns
- Links
- Media kit
||| MENU - smt007 Magazine
Estimated reading time: 6 minutes
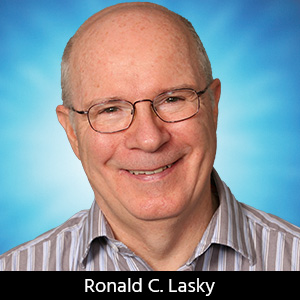
Maggie Benson's Journey: SMT Process Optimization
(Editor’s note: Indium Corporation’s Ron Lasky continues this series of columns about Maggie Benson, a fictional character, to demonstrate continuous improvement and education in SMT assembly.)
Professor Patty Coleman of Ivy University (IU) was excited to see her two best former students, Maggie and John, to help them develop a continuous improvement plan for Benson Electronics (BE). Since both Maggie and John were captains of IU’s student golf teams, Patty suggested that they might want to play nine holes first. Truth be told, Patty also needed the break; she had been working too hard and golf was one of her favorite pastimes. In fact, both Patty and her husband Rob were top notch golfers. Annika Sörenstam had even encouraged Patty to become a professional golfer, but Patty decided against it.
On the other end of the phone, Maggie Benson was delighted by the invitation; she had another chance to try and beat Professor Coleman at golf. She had played with her about five times in the past and lost every time.
On the golf course, a short time later…
Patty just couldn’t help herself; she always wanted to win at golf, and she now found herself one stroke behind Maggie going into the last hole. It wasn’t that she was playing poorly; she was one under par, but Maggie was two under. The last hole was a 510-yard par 5. Maggie hit first—a beautiful 260-yard drive right down the middle.
“Nice drive, Maggie,” Patty remarked.
Maggie is 5 feet 9 inches tall and 145 pounds. She hit that drive as hard as she could.
Patty got up and smoked a 275-yard drive, considerably farther than Maggie’s. Both women drove the ball farther than LPGA pros.
“Why can’t I hit it farther than Professor C?” Maggie thought. “I’m two inches taller and 15 pounds heavier.”
Maggie hit her second shot five yards short of the green and Patty’s was just off the green hole high, 30 feet away. Maggie was savoring a potential victory, or at least a tie, when she chipped up about eight feet from the hole.
However, Patty chipped it in the hole for an eagle 3. Maggie would now need to sink her 8-footer for a tie.
When the ball lipped out, Maggie almost swooned. “Foiled again,” she thought to herself.
John didn’t have any better luck: he shot a 1-under par round, but was crushed by Rob’s 4-under par.
“Professor Coleman, I don’t think I will ever be able to beat you,” Maggie groaned.
“You will someday, Maggie. And remember: it’s ‘Patty,’” Patty said.
“Yes, Professor Coleman,” Maggie responded.
They all burst into laughter.
Patty was a hardworking and dedicated mother, wife, and professor. She cared deeply about her current and former students, but she just couldn’t help herself; she always wanted to win, and she couldn’t help but revel in her small victory.
After golfing, they retired to the Simon Pearce restaurant for lunch to discuss Maggie and John’s improvement plans for Benson Electronics, and to share the details of Maggie and John’s engagement and emerald ring.
Figure 1: An image of the Simon Pearce Restaurant. (Source: roadfood.com.)
Two days later…
Maggie and John gave everyone at Benson Electronics an SMT-101 test. Expecting some concern from the employees, they held an all-employee meeting to explain that the test was to help them understand what type of training was needed. They mentioned to the employees that all training would be paid as overtime and staff would receive time-and-a-half pay. The workers could also opt out of the test and would be in the “SMT Trainee” section of the workshops; 50% of the workers opted for this choice.
As Fred Clinton said, “Better to not take the test and be thought a big dummy than to take it and remove all doubt.”
In general, the staff was happy for the opportunity to get paid training. In addition, it was important to Maggie and John that all the operators learned how to program and run every machine, as there were times in the past when the few operators who knew how to run the stencil printer were out sick and the lines stopped.
Within weeks, much cross training on machines was accomplished and morale was very high. Numerous employees stopped Maggie or John and thanked them for these chances for self-improvement. On two occasions, workers stopped Maggie to thank her, and they burst into tears and gave her a hug. Neither saw that Maggie had tears in her eyes, too.
Maggie, John, and John’s friend, Frank Emory, had spent scores of hours working out a continuous improvement plan. Frank was mainly responsible for optimizing the business processes while Maggie and John would manage the operational processes. They agreed that quick turnaround time, customer satisfaction, high operational efficiency, profitability, and employee morale where their top concerns. The tools would use Lean Six Sigma approaches. A common Lean Six Sigma acronym is DMAIC, which is defined as:
- Define
- Measure
- Analyze
- Improve
- Control
As they were discussing their high-level improvement plan, Frank chimed in, “Hey, you guys, you’re the experts in SMT process optimization, but I have to tell you: BE’s line uptime stinks.[1] This is so fundamental to all that we want to accomplish that we need to address it before we do anything else.”
Both Maggie and John knew Frank was right, but John finally asked, “Frank, how did you come to that conclusion?”
“I’ve been here every day now for weeks,” Frank responded. “Whenever I walk past the shop floor, I make a note in my smartphone if a line is up or not. What do you think the uptime is?”
Maggie groaned, “Don’t tell me it is less than 20%.”
“I get about 15%,” Frank said.
Maggie and John both looked crestfallen.
“Hey, the good news is the business is doing OK right now, and we can easily make it a lot better by getting the uptime to more than 35%,” Frank said.
Maggie and John both nodded in agreement.
What will the trio do to get the uptime to at least 35%? Stay tuned to find out.
I imagine some readers are chuckling at the largesse of Maggie and John, thinking that it would be difficult to be so generous in today’s business climate. Yet, they understand the Law of Exponential Profits (LoEP). (Okay, I made this term up.)
Here is an explanation of the LoEP by a simple example. Suppose a small company like Benson Electronics has $10 million in sales per year, 3% ($300,000) profit, and $700,000 in business expenses, such as labor, rent, depreciation, utilities, etc. Since they are assembling electronics, a low value add but high return on assets business, about $9 million of the cost of their sales is in purchased material such as components, PWBs, etc. Let us assume they increase their productivity by 10%; they will now have $11 million in sales. However, their business expenses increase hardly at all. Labor, rent, and depreciation do not increase, whereas utilities increase only marginally. So, their business expenses might go from $700,000 to $740,000. Therefore, profit is now $360,000 (10% of $11 million—$740,000). Hence, if productivity increases 10%, profits increase 20% ($360K vs. $300K).
References
- Uptime is simply the percentage of time the line is running during production hours. Surprisingly, 35% is very good. I get these values from the scores of factories that I have visited worldwide. If anyone claims to have 70% or more uptime, please invite me to visit.
This column originally appeared in the July 2021 issue of SMT007 Magazine.
More Columns from Maggie Benson's Journey
Maggie Benson’s Journey: The Journey Was Worth ItMaggie Benson’s Journey: A Lesson From Elon Musk’s Playbook
Maggie Benson’s Journey: It’s Just One of Those Days
Maggie Benson’s Journey: Truth Revealed, Balance Restored
Maggie Benson’s Journey: The Big Reveal
Maggie Benson’s Journey: What Is the Profit Potential?
Maggie Benson’s Journey: A Tale of Two Lawn Mowers
Maggie Benson’s Journey: A ‘Cost of Ownership’ Project