-
- News
- Books
Featured Books
- smt007 Magazine
Latest Issues
Current IssueSupply Chain Strategies
A successful brand is built on strong customer relationships—anchored by a well-orchestrated supply chain at its core. This month, we look at how managing your supply chain directly influences customer perception.
What's Your Sweet Spot?
Are you in a niche that’s growing or shrinking? Is it time to reassess and refocus? We spotlight companies thriving by redefining or reinforcing their niche. What are their insights?
Moving Forward With Confidence
In this issue, we focus on sales and quoting, workforce training, new IPC leadership in the U.S. and Canada, the effects of tariffs, CFX standards, and much more—all designed to provide perspective as you move through the cloud bank of today's shifting economic market.
- Articles
- Columns
- Links
- Media kit
||| MENU - smt007 Magazine
Estimated reading time: 5 minutes
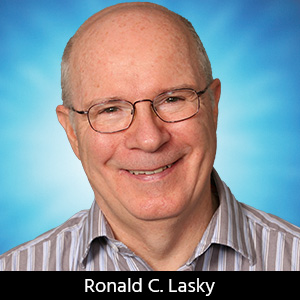
Maggie Benson's Journey: Making Progress on Uptime
Editor’s note: Indium Corporation’s Ron Lasky continues this series of columns about Maggie Benson, a fictional character, to demonstrate continuous improvement and education in SMT assembly.
Maggie was entering the main engineering building of Ivy University to see her mentor, Professor Patty Coleman. Patty had suggested that Maggie hire several Ivy U engineering students to work on the process improvement projects at Benson Electronics to improve productivity and reduce costs. Maggie and Patty planned to discuss the status of the projects at this meeting.
Maggie had to admit that she was a bit intimidated by her mentor. Maggie was never able to beat her in golf, and clearly Patty was Maggie’s superior in technology knowledge. Maggie hoped someday she would find something she was better at than Professor Coleman.
Maggie knocked on Patty’s door, and Patty opened it.
“Hi Maggie! Come on in,” said Patty cheerfully.
“Hello Prof… Patty,” replied Maggie.
“Hey, it’s working! You almost called me Patty,” Patty joked.
They exchanged a few more pleasantries and then Maggie asked, “Did you see the partial eclipse a few days ago?”
“You know, I was thinking about it, but even though I was up early enough, I got side-tracked,” Patty responded.
“It was really neat,” Maggie said. “Also, I saw the Milky Way recently on Mount Ascutney. There was little light pollution and it looked striking. I think the Bortle scale here is better than three… maybe even two.”
“What is the Bortle Class and how can you see the Milky Way?” Patty asked.
“Yes, yes!” Maggie thought, “I know something that she doesn’t know.”
So, Maggie explained that the Bortle scale was a metric that described the darkness of the night sky and that the area in New England where Ivy U was located had quite good night skies for viewing. Maggie then explained that the Milky Way was visible on some clear nights.
“Maggie, that’s really neat,” Patty said. “Maybe sometime my husband Rob, I, and our twin boys can join you to see the Milky Way. I didn’t really think it was possible to see it here.”
Maggie was beaming.
Three days before…
Let’s look in on Maggie, John, and Frank's meeting with Chuck “The Tower”.
“Maggie, John, and Frank, it was an enlightening experience to measure the uptime and develop an improvement plan,” Chuck began.
Maggie and John could sense that it was hard for Chuck to use their first names.
“Fill us in,” Maggie said.
“Well, the uptime is actually 19%, a little better than originally thought. But during the time we measured it, the team was working on the improvement plan, and I think they started paying attention to what they did that caused lost time,” Chuck said. “A big surprise to all of us at the improvement plan meeting was that we didn’t have the sense that if the lines are not running, BE is not making money. In a way, the lines being up pay our salary and secure our future. Tanya Brooks said it best, ‘How can I be such a big dummy? This is so obvious.’ When she said it, the whole group burst into laughter and one person said, ‘Tanya, we are all big dummies.’”
“Chuck, tell us about the results of the improvement plan meeting,” John said.
“Here was what the three of us discussed as a starting point,” Chuck said.
- Feeder racks, though available, were not used. They were in storage and there was never time to learn how to use them.
- Even with the white boards, there was usually “shopping time” required to locate a needed component or a stencil.
- There was not a sense of urgency to replenishing solder paste or components on feeders. Often when these actions were needed, the operators would use this time to take a break, hence stopping the line.
- The lines were shut down for the 30-minute lunch hour, but the line was down much more than 30 minutes.
Chuck continued, “As a result of our meeting, we are now using the feeder racks; they are up and running. What a blessing as they save several hours on a new job. We fill the feeder racks with components for the next job. When it is time to start the next job, we just roll the feeder racks in. For each new job, we assign a ‘feeder rack person’ to assure that this happens.”
“Chuck, that is terrific,” Maggie told him. “Tell us about the white boards and ‘shopping time.’”
“The white boards were one of our bright spots,” Chuck said. “They list what is needed for the next job and who is responsible. Unfortunately, there has not been a sense of urgency, which almost always caused a lack of a few components, a stencil, etc., to start the job. This situation resulted in ‘shopping time’ to find the needed items. So, a sense of urgency has been added to the team. Also, our stock room has been reorganized as some components were mislabeled or in the wrong spot.”
“Wow, sounds like a great success,” John said. “What about paste and component replenishment?”
“Again, having a sense of urgency was the main issue,” Chuck replied. Now, the line is only stopped when absolutely necessary. But I have to say, there was one big disappointment.”
“And that was?” John and Maggie asked in union.
“Shutting down for lunch,” he replied. “We couldn’t work out a way to do it. The folks on each of the lines are friends and they want to eat lunch together.
Frank was silent during the meeting until now. He then commented, “If we gave everyone a $2/hour raise, then we could figure out a way to keep the lines running over lunch?”
Epilogue: Even without running the lines over the lunch hour, uptime went up to over 30% with the changes Chuck and the BE team implemented. BE could now take on almost twice the business they could before the changes.
There was also a rumor that Chuck Tower and Tanya Brooks were now an “item” after spending so much time working together on the uptime project.
Stay tuned:
What is Frank Emory’s plan to keep the lines running during lunch? Could Benson Electronics really pay the workers $2 more per hour and make it work financially?
What is the story on Chuck and Tanya?
This column originally appeared in the September 2021 issue of SMT007 Magazine.
More Columns from Maggie Benson's Journey
Maggie Benson’s Journey: The Journey Was Worth ItMaggie Benson’s Journey: A Lesson From Elon Musk’s Playbook
Maggie Benson’s Journey: It’s Just One of Those Days
Maggie Benson’s Journey: Truth Revealed, Balance Restored
Maggie Benson’s Journey: The Big Reveal
Maggie Benson’s Journey: What Is the Profit Potential?
Maggie Benson’s Journey: A Tale of Two Lawn Mowers
Maggie Benson’s Journey: A ‘Cost of Ownership’ Project