-
- News
- Books
Featured Books
- design007 Magazine
Latest Issues
Current IssueProper Floor Planning
Floor planning decisions can make or break performance, manufacturability, and timelines. This month’s contributors weigh in with their best practices for proper floor planning and specific strategies to get it right.
Showing Some Constraint
A strong design constraint strategy carefully balances a wide range of electrical and manufacturing trade-offs. This month, we explore the key requirements, common challenges, and best practices behind building an effective constraint strategy.
All About That Route
Most designers favor manual routing, but today's interactive autorouters may be changing designers' minds by allowing users more direct control. In this issue, our expert contributors discuss a variety of manual and autorouting strategies.
- Articles
- Columns
- Links
- Media kit
||| MENU - design007 Magazine
Estimated reading time: 6 minutes
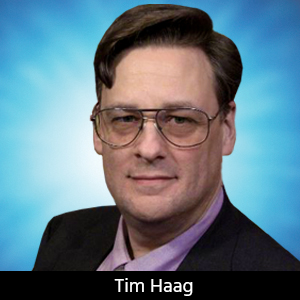
Tim's Takeaways: The Collaborative PCB Design Process—A Necessity for Efficient Manufacturing
It’s been a few months since the June edition of Design007 Magazine was published, but since I missed the Star Trek theme of that issue, I hope you won’t mind if I start with a related anecdote. Star Trek presented many fun gadgets and gizmos to its audience that have influenced ingenuity and invention for over five decades now. Some of these influences are pretty obvious, such as flip cellphones, which enjoyed a lot of free marketing due to Star Trek’s communicator. Be honest, back when you had one of those phones, how many of you were tempted to say “Kirk to Enterprise” when you flipped it open? Other innovations, like phasers and photo torpedoes, thankfully remain solely in the realm of science fiction (at least for now).
Other than the starship itself, though, I think that most people would agree that the most interesting gadget on Star Trek was the transporter system. I am sure that the ability to beam out of danger, or a potentially embarrassing moment in life, has tilted many imaginations other than just mine. But did you know that unlike phasers and warp speed, which are very standard accoutrements for a science fiction show, that the transporter was invented solely for budgetary reasons?
When Gene Roddenberry was developing Star Trek, he realized that he couldn’t afford to land a large spaceship multiple times in every episode. Even with the special effects of the time, it would have been too expensive to make it look even halfway realistic, yet he still needed some method or device to get his characters in and out of the action quickly. To resolve this problem, the transporter beam was conceived and became a basic fixture of the show. The actor would step into the transporter chamber on the sound stage, and then step back out with the camera still running. During post-processing the special effects department would cut and splice that footage together to make it seem like the actor had disappeared. To complement this vanishing act, footage of falling sand filmed under a high-intensity light would be optically merged with the disappearing actor to complete the illusion of futuristic transportation.
I probably should have preceded that revelation with “Spoiler Alert” before writing it, and hopefully I haven’t ruined the show for you. My point, however, was to describe how financial necessity is often the mother of invention, and not just in 55-year-old science fiction television programing either. We can see how efforts to cut expenses and become more efficient can help create a better product in our own industry as well.
Circuit board design used to be a more complicated and lengthy process than it is now with the need to build scores of test circuits, develop multiple prototypes, and toiling with manual design operations. I’m not sure how many designers now have ever had to work with X-Acto knives, Rubylith, and opaque tape on a light table like I used to long ago, but if you did you will know what I’m talking about. Even after CAD systems were introduced into the design cycle, it could still be a lengthy process. The one good thing about all the time it took was that it gave ample opportunity for everyone to be involved. However, with so much automation in use, and with the ever-increasing need for faster time to market, many designs today seem to fly through the design cycle at warp speed. The great thing about speed, of course, is that when everything is going well, it is a glorious achievement. But if something goes wrong, that fast pace can produce a wreck on a wreck.
It has been reported to me that some designers have said that they don’t even know which fabricators will be building their designs until the job is already out the door. On the flip side, I have talked with PCB contract manufacturers who want more interaction with PCB designers but aren’t getting it. They have told me that they prefer to work together with designers prior to PCB layout to review the design and offer their input. Instead, the first they often know of a design is when they receive the completed manufacturing files. This forces them to find ways to make what they already have work, instead of helping the designers optimize their layout for better production yields and circuit board performance.
In our rush to get the product “out the door,” are we sacrificing quality for market share? Are we spending more effort in trying to push a poor design through production rather than taking the time to improve it for error-free manufacturing, higher yields, and less expense? Are we finding out that here, too, financial necessity is going to be the mother of invention; in this case, the invention will be a more collaborative relationship between circuit board design and manufacturing? The plain and simple truth is that the need for better collaboration should be at the heart of all PCB process improvement. Here are some ideas on how we can go about doing it:
1. Build a business relationship with your manufacturer prior to designing the board.
The business of PCB manufacturers is to build circuit boards, and they have a lot of experience building a great many types for different applications. With their experience they can add a lot of value to the project while it is still in the design phase. For instance, a good PCB manufacturer will review the board’s bill of materials to ensure that the parts specified are available and at a good price. If there are problems procuring any of the listed components, the manufacturer will often be able to make recommendations on component or circuitry changes to help. By engaging with the manufacturer early on, you can leverage their knowledge and experience to help design a better board.
2. Involve all members of the design team when working with the manufacturer.
Many business relationships rely on a single point of contact, but that practice can hamper the productivity that a fully collaborative partnership can make possible. It is important that all stakeholders in the design have accessibility to their manufacturing partner in one form or another to speedily resolve issues and get questions answered. As an example, a part change recommendation from the manufacturer should be passed through the design team’s CAD librarians as soon as possible to get new schematic symbols and PCB footprints ready for the design.
3. Use the engineering and other professional resources available at the manufacturer.
PCB manufacturers often have engineering teams that can help with schematic development or changes, design reviews, layout alterations or enhancements, and test development. In many instances, design modifications can be handled by the manufacturer, who will follow up with a completely new set of design documentation of their work. While this may not fit every design team’s workflow, it is a benefit that should not be ignored to help with unscheduled changes or overflow work.
4. Explore the use of more collaborative tool functionality with your manufacturer.
Many design tools now feature utilities that help enhance the communication between circuit board design teams and PCB manufacturers. Using data transfer standards, such as IPC-2581, these design utilities allow design teams and manufacturers to efficiently exchange circuit board layer stackup information and fab and assembly files. Systems like these help the collaborative PCB design process by making it easier for designers and their manufacturing partners to communicate with each other as they work together to build a better product.
More and more designers and manufacturers are facing the financial necessity of finding new ways to improve the efficiency of the business partnership. Fortunately, by continually building on the collaborative relationships they already have, they are already on their way to further streamlining their design processes. As with all aspects of our industry, it will be rewarding to see how these collaborative relationships grow and what new benefits come from them. Until next time everyone, keep on designing.
This column originally appeared in the September 2021 issue of Design007 Magazine.
More Columns from Tim's Takeaways
Tim’s Takeaways: One for the ArchivesTim’s Takeaways: The Art of Technical Instruction
Tim’s Takeaways: PCB Design and Manufacturing—Let’s Work Together
Tim’s Takeaways: Take It From Scotty, Simple Really is Better
Tim’s Takeaways: Human Ingenuity and the Rigid-flex PCB
Tim’s Takeaways: How I Learned Advanced Design Strategies
Tim’s Takeaways: Batter Up—Stepping Up to the Substrate
Tim’s Takeaways: Tribal Knowledge—Not the Villain You Thought