-
- News
- Books
Featured Books
- design007 Magazine
Latest Issues
Current IssueAll About That Route
Most designers favor manual routing, but today's interactive autorouters may be changing designers' minds by allowing users more direct control. In this issue, our expert contributors discuss a variety of manual and autorouting strategies.
Creating the Ideal Data Package
Why is it so difficult to create the ideal data package? Many of these simple errors can be alleviated by paying attention to detail—and knowing what issues to look out for. So, this month, our experts weigh in on the best practices for creating the ideal design data package for your design.
Designing Through the Noise
Our experts discuss the constantly evolving world of RF design, including the many tradeoffs, material considerations, and design tips and techniques that designers and design engineers need to know to succeed in this high-frequency realm.
- Articles
- Columns
- Links
- Media kit
||| MENU - design007 Magazine
Real Time with... American Standard Circuits: Flex and Rigid-Flex PCBs
September 30, 2021 | Pete Starkey, I-Connect007Estimated reading time: 3 minutes
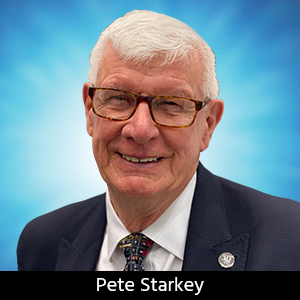
In the first of a series of three Real Time with…American Standard Circuits interviews, I-Connect007 Managing Editor Nolan Johnson got some no-nonsense answers from Anaya Vardya and Dave Lackey on the topic of flex and rigid-flex PCBs. I was impressed by ASC’s generosity in sharing knowledge and technology.
President and CEO Anaya Vardya introduced American Standard Circuits, a well-diversified PCB manufacturer, founded in 1988 and skilled in the fabrication of flex and rigid-flex, RF microwave, digital boards, and a host of different thermal management solutions. As a total solutions provider, ASC focuses on working with designers up-front in the process, minimising the number of churns, ensuring good manufacturability, and a high first-time success rate.
It was refreshing to have the opportunity to witness a down-to-earth Q&A session: intelligent questions from Nolan Johnson and knowledgeable answers from ASC’s flex specialist Dave Lackey with an emphasis on in-depth, practical know-how and the importance of getting involved in the design process as early as possible.
Johnson remarked on the number of different approaches to flex design. Lackey used a series of clear photographs and schematics to describe three main categories:
- Pure flex circuits, whether simple single-sided or complex multilayer, were constructed from all-flexible materials, copper-clad substrates, adhesives, and bond-plies, with laminated polyimide cover layers. In certain instances, liquid photoimageable solder mask could be used as an alternative.
- Flex with stiffeners to add rigidity in certain areas. Different stiffening materials were used for different applications, temporary or permanent, in component-assembly areas or to reinforce connectors.
- Rigid-flex, a combination of flexible and rigid materials, with flex layers incorporated within the rigid areas enabling the elimination of cables and connectors to achieve more compact packaging and higher reliability.
In response to Johnson’s enquiry about typical applications, Lackey declared that there was an unlimited number, from simple connecting ribbons to complex devices with 90- and 180-degree turns enabling smaller-volume higher-reliability packaging.
Regarding criteria for successful design and reliability, Lackey drew a distinction between static and dynamic flex, the being bent to fit, the latter being subject to continuous motion. It was essential to recognise the actual mechanical performance requirement in a particular application and to understand bend radius in relation to the thickness of the flexible materials and the geometry and orientation of the conductors.
The contribution of the mechanical designer was as fundamental as that of the electronics designer, and both could benefit enormously by involving the PCB fabricator as early as possible in the design cycle. The fabricator could advise on the choice and suitability of materials and constructions, as well as the benefits of details like cross-hatched ground planes and knowing how to properly model characteristic impedance. “A lot of factors to balance: here’s what we can do to make this work.” Lackey quoted case histories and examples of improving manufacturing yield and reliability while saving on overall cost.
His opinions were echoed in Vardya’s closing words: “If the viewer takes nothing else away from this discussion, it is to really involve your PCB fabricator right from the word ‘Go.’ The most important thing any designer can do in designing a flex circuit is to work with the PCB fabricator. They will save you tons of time and you will be much better off for having done that.”
Finally, in answer to Johnson’s question about critical things for me to keep in mind, Lackey advised giving careful consideration to what IPC classification was required, avoiding specifying name-brand material by referring to IPC slash-sheets and providing clear fabrication notes, particularly if quick turnaround was needed.
In my opinion, taking the time to view this Real Time with…American Standard Circuits video is 15 minutes well-spent; excellent information professionally presented, and the opportunity to submit further questions by email. Thank you, ASC.
Visit I-007eBooks to download your copies of American Standard Circuits’ micro eBooks today:
The Printed Circuit Designer’s Guide to… Fundamentals of RF/ Microwave PCBs
The Printed Circuit Designer's Guide to... Flex and Rigid-Flex Fundamentals
The Printed Circuit Designer’s Guide to …Thermal Management: A Fabricator’s Perspective