-
-
News
News Highlights
- Books
Featured Books
- smt007 Magazine
Latest Issues
Current IssueSpotlight on India
We invite you on a virtual tour of India’s thriving ecosystem, guided by the Global Electronics Association’s India office staff, who share their insights into the region’s growth and opportunities.
Supply Chain Strategies
A successful brand is built on strong customer relationships—anchored by a well-orchestrated supply chain at its core. This month, we look at how managing your supply chain directly influences customer perception.
What's Your Sweet Spot?
Are you in a niche that’s growing or shrinking? Is it time to reassess and refocus? We spotlight companies thriving by redefining or reinforcing their niche. What are their insights?
- Articles
- Columns
- Links
- Media kit
||| MENU - smt007 Magazine
Estimated reading time: 4 minutes
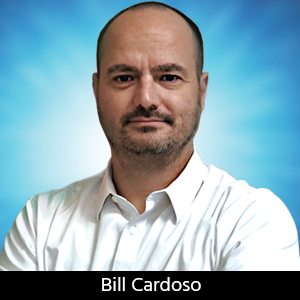
The X-Rayted Files: Was CS Model 101 Built on Industry 4.0?
While smart devices like sleep trackers that monitor the quality of our ZZZs are exciting to some, for others it induces the fear of becoming subject to robot overlords. Regardless on where you stand on such devices, the age of the Internet of Things (IoT) is upon us, and as manufacturers, IoT is just one facet of the broader Industry 4.0. As one who takes the adage, “You can’t manage what you don’t measure,” to heart, I’m inclined to lean into this new paradigm.
I confess, I’m not particularly moved by a washing machine that texts me when it has finished a cycle, or a fridge that alerts me that I’m low on milk, but I am pretty bullish on Industry 4.0 and what it means for the future of manufacturing.
For a while now there has been talk of Industry 4.0, and for many it was reminiscent of talk of a future full of flying cars (still looking forward to those). While much of the technology that will support this fourth industrial revolution already exists, and much of it is maturing rapidly, it can still feel like a far-off sci-fi future. But the pandemic may have provided a catalyst for advancing the adoption of the technologies that make up Industry 4.0, and for some, our willingness to embrace them.
Industry 4.0 will mean different things to different manufacturers, but for most, it will include the integration of some key elements. Data collection and analytics will be the cornerstone of advanced manufacturing, made possible on the factory floor by industrial IoT sensors collecting an array of data from equipment, lighting, environmental sensors and more. Machine learning and artificial intelligence, supported by cloud storage and software will make this treasure trove of data actionable. For example, sensing an increase in power consumption of a CNC mill might indicate tool wear and initiate a tool change, thus optimizing tool life while maintaining quality and consistency.
Autonomous robots will continue to replace human labor for repetitive and dangerous tasks, adding to efficiency and shifting talent to more productive work (more on talent in a bit). As additive manufacturing matures, 3D printing will become a staple of production, no longer relegated to product development and prototyping. Imagine that the CNC with the worn tool can trigger a set of 3D printers to start manufacturing replacement parts as needed. With that, we close the loop to achieve self-healing production lines. Augmented reality (think Google Glass) will change the way we do employee training and execute maintenance.
An important aspect of all this data collection is information sharing. Not only will machines share information, but information within an entire organization will be shared across all departments. All this measuring, combined with analysis and a broad sharing of information will allow for remarkable management of all of an organization’s assets. Resulting benefits will include improved worker safety, increased productivity and flexibility, and significant savings from reductions in unplanned maintenance.
Manufacturing has been derided as dirty, dark, and dangerous, making it difficult to attract top talent. Industry 4.0 or “smart factories” also afford an opportunity to change that narrative. Factories and manufacturing can offer cleaner, safer, more flexible, and career-oriented jobs. Making manufacturing attractive to a new generation of workers is imperative, especially domestically, when so much of the talent in this field is nearing retirement. There aren’t enough uncles taking their adolescent nieces and nephews aside and suggesting “I’ve got one word for you—manufacturing.” Automating some of the most dangerous and tedious work, enabling remote work for many, and the increasingly high skill opportunities available in modern manufacturing should help improve the ability to compete for talent. Manufacturing jobs, in so many cases, are or will become tech jobs. Does your organization currently have a digital twin architect on staff? If not, it likely will down the road.
For our part, Industry 4.0 means reimagining how X-ray inspection equipment fits into the modern manufacturing environment. The prospects are really exciting when we start to integrate inspection technology with things like machine vision tools, cobots and robots, and business management systems. The resulting information can have a positive impact on manufacturing process, resulting in improved quality and consistency, and reduced waste, among other things.
Our experience with the COVID-19 pandemic emphasizes the value of increasing factory automation, as well as improved data sharing and collection. The strains we all experienced due to shutdowns and having to restructure our operations to accommodate social distancing and other safety measures, will likely accelerate the adoption of these emerging advancements in automated, even autonomous manufacturing.
Likewise, the pains we’ve endured due to supply chain failures reinforces the need for greater date transparency and information sharing. For some, this transformation will take the form of a slow evolutionary change. For others, the change will be rapid and revolutionary, and some early adopters will gain competitive advantages that will be downright disruptive. That potential for disruption makes the decision about if and when to adopt such new technologies a strategic one. I’m reminded of another adage I’ve become fond of: “You can either disrupt or be disrupted.”
Dr. Bill Cardoso is CEO of Creative Electron.
More Columns from X-Rayted Files
X-Rayted Files: Best Practices in Buying MachinesX-Rayted Files: ’23 and Me?
X-Rayted Files: Battery-Powered Advancements Keep on Ticking
X-Rayted Files: What’s Cooler Than X-ray?
X-Rayted Files: My Favorite BGA Assembly Ever, Part 3
X-Rayted Files: My Favorite BGA Assembly Ever, Part 2
X-Rayted Files: My Favorite BGA Assembly Ever
X-Rayted Files: Smart vs. Intelligent SMT Factory